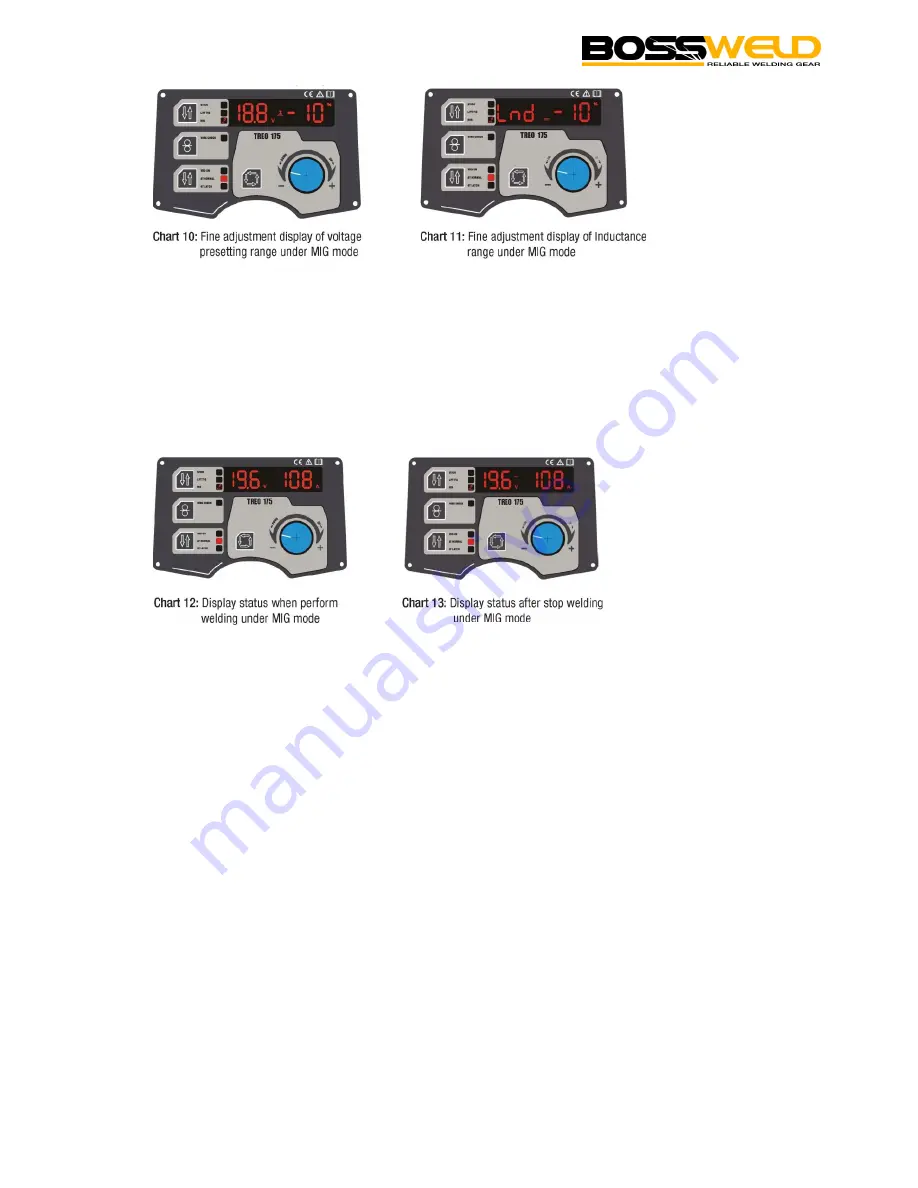
16
g. Three seconds later after setting the welding parameters, the (multifunctional data display) would
flash for one time, which means the data has been saved. The panel will display this data when
you restart the machine.
h. Releasing the torch switch and stopping welding, the panel displays “HOLD” flashes for 3
seconds, this means the welding stops. 2 seconds later, (multifunctional data display) redisplays
the preset current.
Summary of Contents for TREO 175
Page 1: ...User Manual TREO 175 ...
Page 11: ...11 Explanatory drawing for installation of TREO 175 STICK ...
Page 22: ...22 CIRCUIT DIAGRAM ...
Page 30: ...30 Notes ...
Page 31: ...31 Notes ...