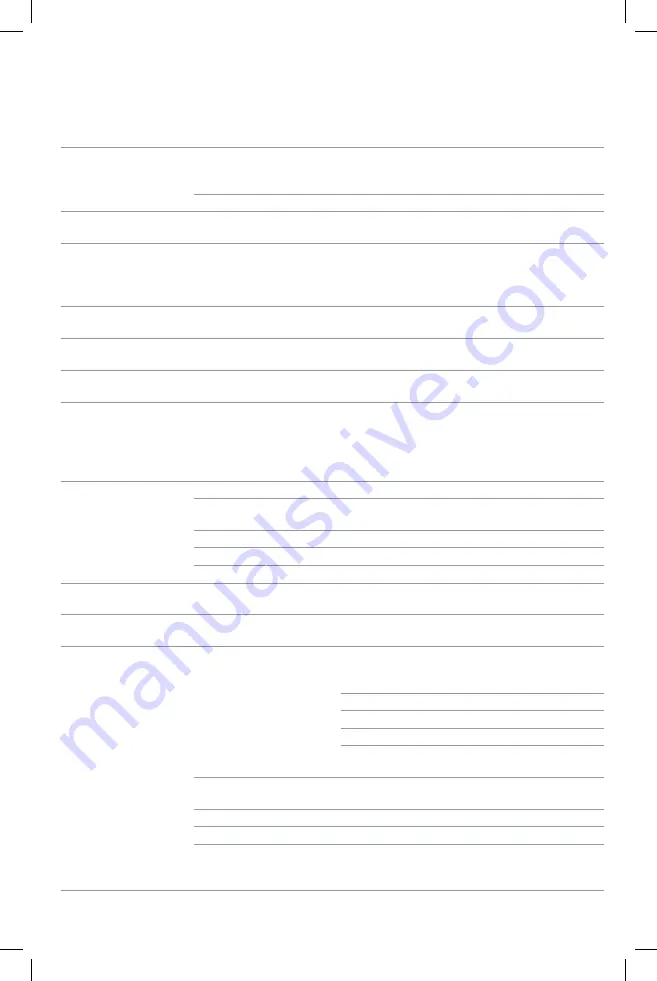
English
9
TROUBLESHOOTING
WARNING:
Risk of Unsafe Operation. Unit cycles automatically when power is on. When servicing, you may
be exposed to voltage sources, compressed air, or moving parts. Before servicing unit unplug or disconnect
electrical supply to the air compressor, bleed tank of pressure, and allow the air compressor to cool.
PROBlEM
CAUsE
CORRECTiOn
Excessive tank pressure - safety
valve pops off.
Pressure switch does not shut off
motor when compressor reaches "cut-
out" pressure.
Move On/Off lever to the "Off" position, if the outfit does not shut off
contact a Trained Service Technician.
Pressure switch "cut-out" too high.
Contact a Trained Service Technician.
Air leaks at fittings.
Tube fittings are not tight enough.
Tighten fittings where air can be heard escaping. Check fittings with
soapy water solution.
Do Not Overtighten.
Air leaks in air tank or at air
tank welds.
Defective air tank.
Air tank must be replaced. Do not repair the leak.
WARNING: Risk bursting. Do not drill into, weld or
otherwise modify air tank or it will weaken. The tank can
rupture or explode.
Air leaks between head and
valve plate.
Leaking seal.
Contact a Trained Service Technician.
Air leak from safety valve.
Possible defect in safety valve.
Operate safety valve manually by pulling on ring. If valve still leaks, it
should be replaced.
Knocking Noise.
Possible defect in safety valve.
Operate safety valve manually by pulling on ring. If valve still leaks, it
should be replaced.
Pressure reading on the regulated
pressure gauge drops when an
accessory is used.
It is normal for "some" pressure drop
to occur.
If there is an excessive amount of pressure drop when the accessory is
used, adjust the regulator following the instructions in the
Description
of Operation
paragraph in the
Operation
Section.
NOTE:
Adjust the regulated pressure under flow conditions (while
accessory is being used).
Compressor is not supplying
enough air to operate accessories.
Prolonged excessive use of air.
Decrease amount of air usage.
Compressor is not large enough for
air requirement.
Check the accessory air requirement. If it is higher than the SCFM or
pressure supplied by your air compressor, you need a larger compressor.
Hole in hose.
Check and replace if required.
Check valve restricted.
Have checked by a Trained Service Technician.
Air leaks.
Tighten fittings.
Regulator knob has continuous
air leak.
Damaged regulator.
Replace.
Regulator will not shut off
air outlet.
Damaged regulator.
Replace.
Motor will not run.
Fuse blown, circuit breaker tripped.
Check fuse box for blown fuse and replace as necessary. Reset circuit
breaker. Do not use a fuse or circuit breaker with higher rating than that
specified for your particular branch circuit.
Check for proper fuse. You should use a time delay fuse.
Check for low voltage problem.
Check the extension cord.
Disconnect the other electrical appliances from circuit or operate the
compressor on its own branch circuit.
Extension cord is wrong length
or gauge.
Check the extension cord.
Loose electrical connections.
Check wiring connection inside terminal box.
Faulty motor.
Have checked by a Trained Service Technician.
Motor overload protection switch
has tripped.
Refer to
Motor Overload Protector
under
Description of Operation
.
If motor overload protection trips frequently, contact a Trained
Service Technician.
Summary of Contents for BTEC25200
Page 35: ......