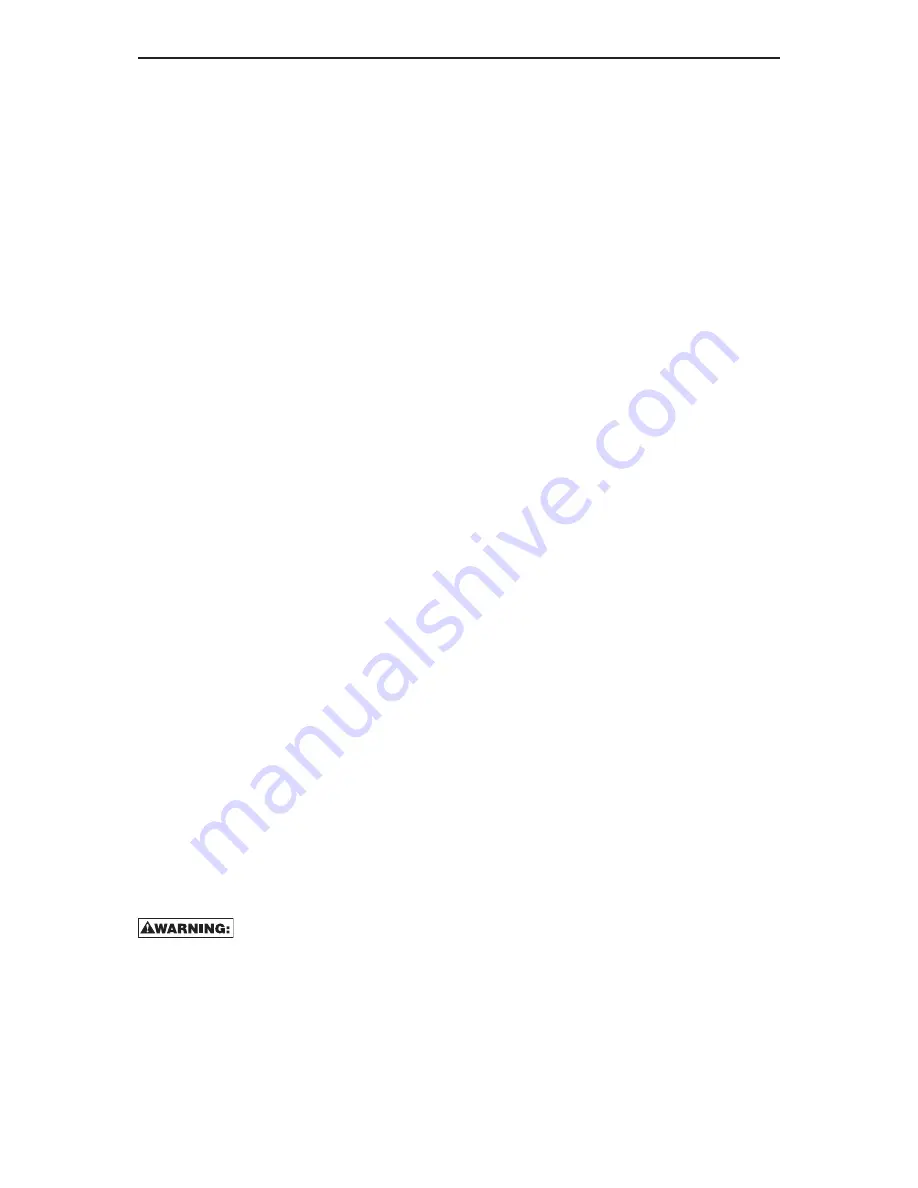
6
7
OPERATION
Pre-Start Procedures:
1. Inspect the compressor for any damaged components Do not operate if compressor is
damaged.
2. Verify that the tanks have been drained and are clear of any moisture or dirt.
(
See “Draining Tank”
).
3.
INSTALLING THE DIPSTICK
To prevent oil from spilling during shipping, the air compressor has a plug installed in the oil
fill hole. Before using the unit the first time, replace the plug with the oil fill dipstick and check
the oil level.
• Remove the plug from the oil fill hole.
• Insert the dipstick into the oil fill hole.
• Remove the dipstick and check the oil level, making sure the oil registers between the
MIN and MAX reference levels on the dipstick. If the level does not register between
those areas, refer to Checking the Oil in the Operation section of this manual.
• Replace the dipstick.
4.
BREAKING IN THE PUMP
Perform the following steps to break in the pump before using the air compressor for the
first time.
• Make sure the plug in the oil fill hole has been replaced with the dipstick and the oil level
falls within the MIN and MAX range.
• Turn the pressure regulator knob fully clockwise to open the air flow.
Lift the knob to adjust the air flow, and push down to lock.
• Place the switch in the
OFF
(O) position.
• Open both drain valves completely.
NOTE
: The air compressor has two separate tanks: an upper tank and a lower tank. Be sure to
open drain valves for both.
• Connect the air compressor to a power supply.
• Place the switch in the
ON
( I ) POSITION and run the air compressor
for 10 minutes to break in pump parts.
• Place the switch in the
OFF
(O) position.
• Close the drain valves.
5.
ATTACHING A HOSE
(Not Supplied)
• Make sure the air compressor is off and unplugged.
• Rotate pressure regulator knob fully counterclockwise.
• Attach hose with male connector to Nitto fitting on air compressor.
Do not attach any tools to the open end of the hose until start-up has been completed.
Summary of Contents for BTFP02040
Page 14: ...11 NOTES 14 ...
Page 15: ...11 NOTES 15 ...