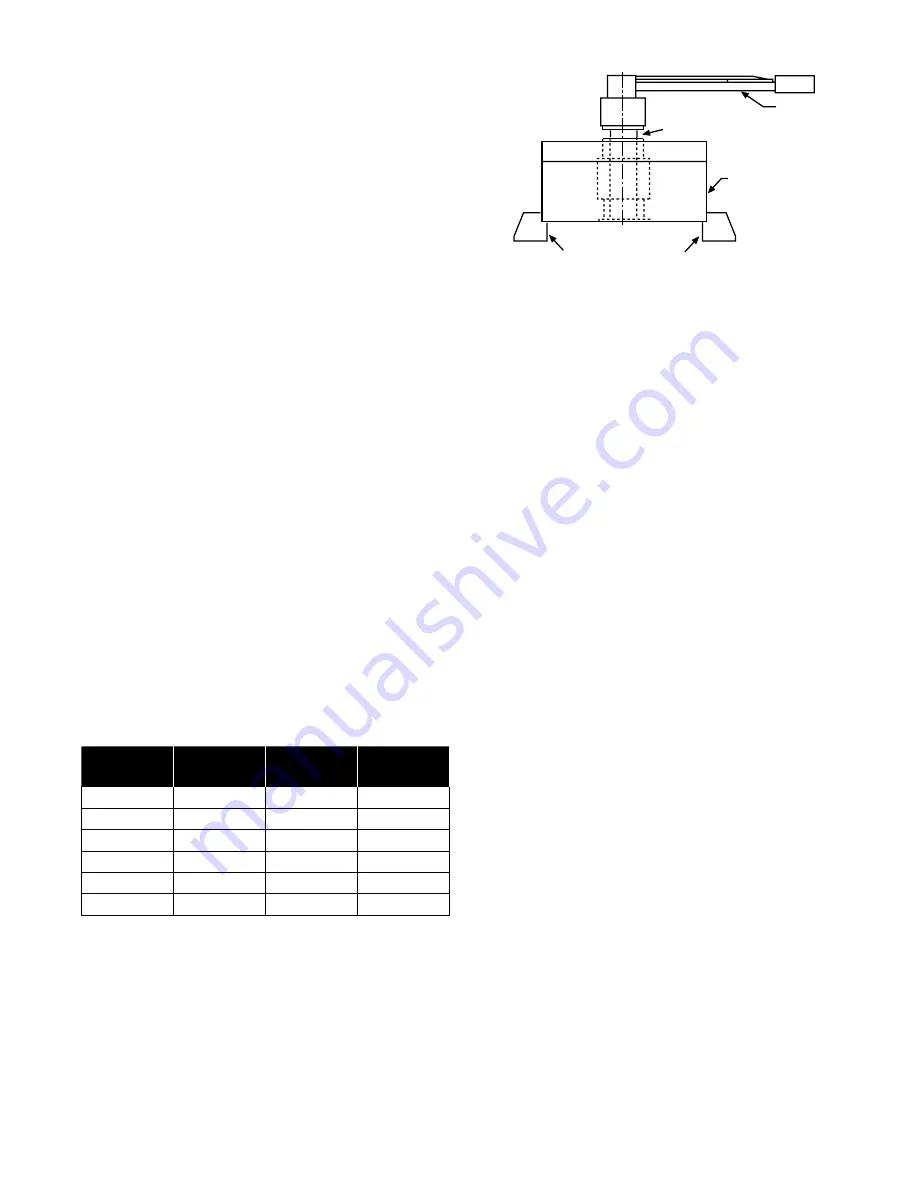
Boston Gear • 800-825-6544
P-3003-BG
13
C. Torque Verification
1. Place the clutch in a chuck or vise with the cover
facing upward.
2. Insert the appropriate size arbor and key into rotor.
(See Figure 18)
3. Turn the drive spring screw (21) clockwise until it is
flush with the surface of the housing.
4. The clutch is supplied with a torque selector dial.
The torque selector dial is the mill marks located at
the hole stamped 9 on the housing. If a drive spring
(18), reset spring (19), and/or a reset spring screw
(14) were replaced, chances are that the stamped
torque values on the dial are no longer valid. It may
be necessary to grind the old numbers off and to
stamp new ones.
5. Tighten the reset spring screw (14) until it reaches
the limit stop pin (4). This will be the maximum
torque position. If the maximum torque is not
desired, tighten the reset spring screw to one of the
locations on the torque selector dial.
6. Disengage the clutch with a torque wrench. Fine
tune the torque by turning the drive spring screw
(21) until the desired release torque is obtained.
7. Refer to Section I, C for further details on torque
adjustment.
8. Once the desired release torque is obtained, tighten
the locking screws (25) located over the drive spring
and reset spring screws to ensure that they will not
move. The unit is now ready for installation. Refer to
Section lll for installation of basic clutch.
Table 10 - Cover Screw Seating Torques
Clutch
Size
Screw Size
Quantity
Seating
Torque
1
1/4-20
3
100 in.lb.
2
5/16-18
3
200 in.lb.
3
3/8-16
3
350 in.lb.
4
1/2-13
4
850 in.lb.
5
5/8-11
4
1,700 in.lb.
6
5/8-11
4
1,700 in.lb.
Figure 18
D. Limit Switch Actuating Mechanism (LSAM)
Assembly
1. Apply a graphite lubricant to the release ring groove
of the cover (8).
2. Insert the actuating stud (40) through the appropriate
hole in the release ring (35). To identify this hole
place the release ring in the groove of the cover.
When the trip pin holes line up with the through
holes of the cover, the actuating stud hole will line
up with the counterbored hole in the groove of the
cover.
3. Install the actuating stud nut (39) onto the actuating
stud (40) and tighten.
4. Install a spring terminal (43) on each end of the
return spring (38). Clutch sizes 5 & 6 require two
return springs.
5. Insert a spring terminal screw (41) through the hole
of the spring terminal (43), and place a spacer collar
(36) on the end of the screw. Insert the end of the
screw into the threaded hole of the release ring (35)
and tighten. The end of the screw may protrude past
the release ring. Grind the end of the screw flush
with the surface of the release ring. Install second
spring terminal screw on clutch sizes 5 & 6 as just
described. Move to Step 13 for clutch sizes 5 & 6.
6. Press the trip pins (32) into the trip plate (31).
7. Install a bowed snap ring (34) into the groove of
each trip pin located next to the trip plate.
8. Place the trip plate flat on a table with counterbored
holes facing up. Insert the thrust springs (37) into the
counterbores.
Torque Wrench
Arbor
Trig-O-Matic Clutch
Vice or Chuck Jaws