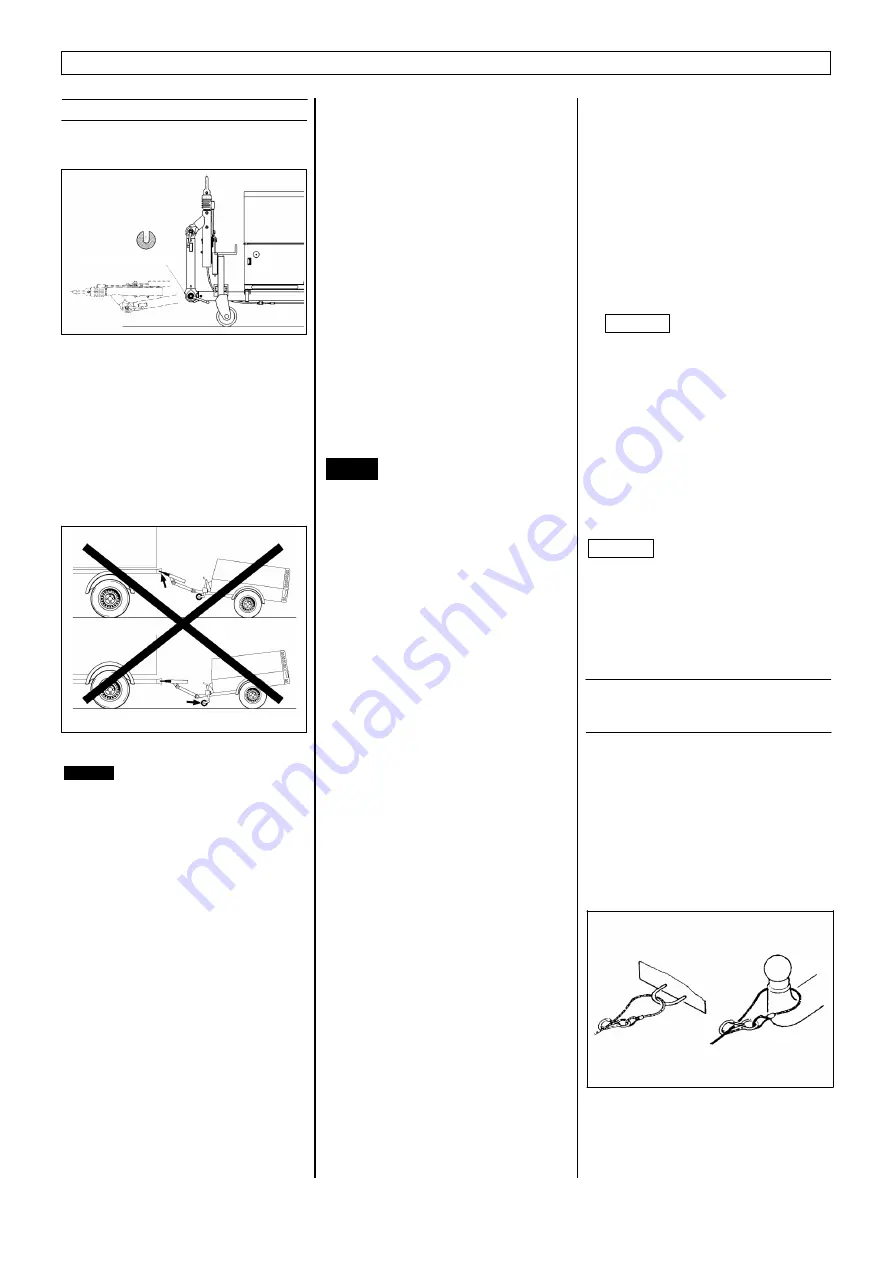
5. Transport and installation on site
20
5.1 Transport
Transport safety locking of the towing
arrangement
Fig. 11
Before moving the compressor for the
first time slacken the ratchet on height-
adjustable towing gear and remove the
transport securement. Then adjust the
towing gear from the vertical transport
position to the required attachment height
for the towing vehicle and lock it in place
in the toothing using the ratchet (see
Section 15. Undercarriage, height-
adjustable towing gear).
Fig. 12
Danger
Make sure to check the torque after
50 kilometers following wheel
mounting and at regular intervals.
Tighten wheel nuts or screws evenly
in a diagonal sequence to the specified
torque using a torque wrench.
Replacing the trailer coupling ring
The coupling arrangements which can
be used:
*
Trailer coupling ring RD 40
*
Coupling 50 dia.
*
Coupling ring 2" dia. (only for UK)
*
Coupling ring 68 x 25 dia. (only for
France)
A different coupling unit in the form of a
complete kit may be ordered, if necessary.
Replacing the trailer coupling ring is
permitted only if proper fitting is carried out
by an inspectorate for the sector covered
by the Regulations Authorizing the Use of
Vehicles for Road Traffic (e.G. the TÜV -
Technical Inspectorate, DEKRA - German
Motor Vehicle Monitoring Association,
etc.). The inspection station provides a
fitting certificate to be kept with the vehicle
documents.
The screw compressor may only
be transported on public roads if
*
The machine group (engine) is
not running,
*
The pressure tank is not under
pressure,
*
The shielding is closed,
*
The blocks are firmly hooked in
place,
*
Hoisted and secured tail wheel,
*
The tyres and brakes are
operationally safe and roadworthy,
*
The lighting is fully functional.
Never exceed the maximum towing
speed! Danger! Observe national
regulations!
Please also observe the safety
instructions in Chapter 3 on the
subject of transporting.
Before transporting the compressor,
check to make sure that the draw gear of
the towing vehicle and the drawbar eye or
trailer hitch ball connection are aligned
exactly to each other.
When transporting the screw compressor
with a vehicle, the following points must
be observed:
*
The shielding is closed.
*
The blocks are firmly hooked in place.
*
The support(s) is(are) retracted and
locked in position (jockey wheel).
*
Drawbar is connected to the towing
vehicle.
*
The drawbar is adjusted to the height
of the towing vehicle (option).
*
The contact-breaking cable is
connected to the towing vehicle. Safety
chains are attached on towing vehicle.
*
The electrical cable (option) is
connected to the vehicle and to the
screw compressor .
*
Check the lights (tail lights, brake
lights, indicator lights, and rear fog
lamp) (option).
*
Check to make sure that the wheels
are properly tightened, the tyres are in
a roadworthy condition.
Check tyre pressure, and adjust if
necessary (risk of accident). A too
high tyre pressure can lead to
overstraining of safety parts.
*
When parking the compressor prior to
uncoupling from the towing vehicle
actuate the handbrake, detach the
contact-breaker cable and the lighting
cable, and secure the compressor
against rolling using chocks. Then
adjust to the horizontal position by
means of a support or support wheel.
Always keep a safe distance from the
edges of foundation ditches and
embankments! Do not travel across
slopes transversely.
5.2 Attachment of the contact-
breaker cable on braked
chassis
If the towing connection becomes
uncoupled, the trailer is braked by the
breakaway cable. Put the breakaway cable
in the eye provided or wind it around the
towing collar and hitch it up to the cable
with the snap link.
The breakaway cable must be attached
in a way that ensures that even on
extremely sharp bends there is no danger
of activating the locking brake.
Fig. 13
Danger
Attention
Attention
Transport safety locking
Summary of Contents for GDP21
Page 8: ...6 2 Foreword Chassis rigid braked Fig 5...
Page 53: ......
Page 61: ......
Page 62: ......