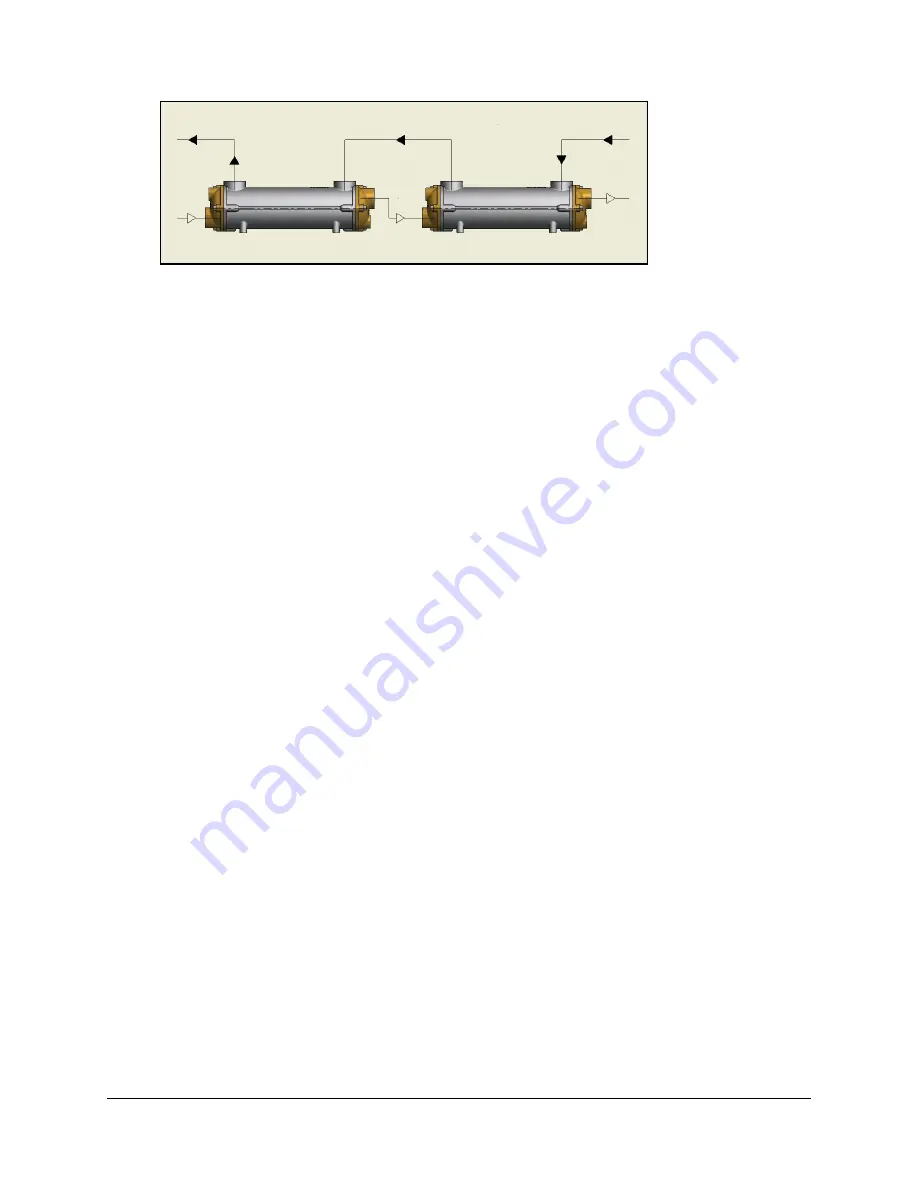
Rev D
6
Or in series:
A filter with a maximum permeability of 2.0mm should be used prior to the inlet of each circuit of the
oil cooler.
Nothing should be welded to any part of the oil cooler. Each unit has threaded holes on its underside to
facilitate mounting.
2.3 Connecting the heat exchanger
Shut off all drainage valves in the flow and return pipes of the primary and secondary circuits.
When fitting the heat exchanger into the pipe work care must be taken to ensure that no debris has been
introduced into the primary or secondary circuit of the heat exchanger.
Unsupported lengths of pipework should be avoided so as not to subject the heat exchanger to
excessive loads.
Water side pipework diameter should not reduce to less than the connection size within a distance of
1m from the oil cooler.
Measures should be taken to isolate the oil cooler from excessive vibration.
Taper fittings are not recommended as these can split the shell and end cover castings if over tightened.
The correct length of fitting should be used as too long a fitting will damage the tubestack.
Pipework materials must be compatible with the oil cooler materials. Stainless steel sea water pipes and
fittings should not be used adjacent to the heat exchanger.
If the sea water supply is taken from the ships main, ensure that the recommended flow rate
cannot be exceeded. This will normally mean that an orifice plate must be fitted in the pipe work at
least 1m before the cooler with the orifice size calculated to ensure that the maximum sea water
flow rate cannot be exceeded. If these precautions are not taken, it is possible that the sea water
flow rate through the cooler may be several times the recommended maximum which will lead to
rapid failure.
For our oil coolers, the maximum permitted sea water flow rates are as follows:
EC range
50 l/min.
GK range
300 l/min.
FC range
80 l/min.
JK range
400 l/min.
FG range
110 l/min.
PK range
650 l/min.
GL range
200 l/min.
RK range
900 l/min.