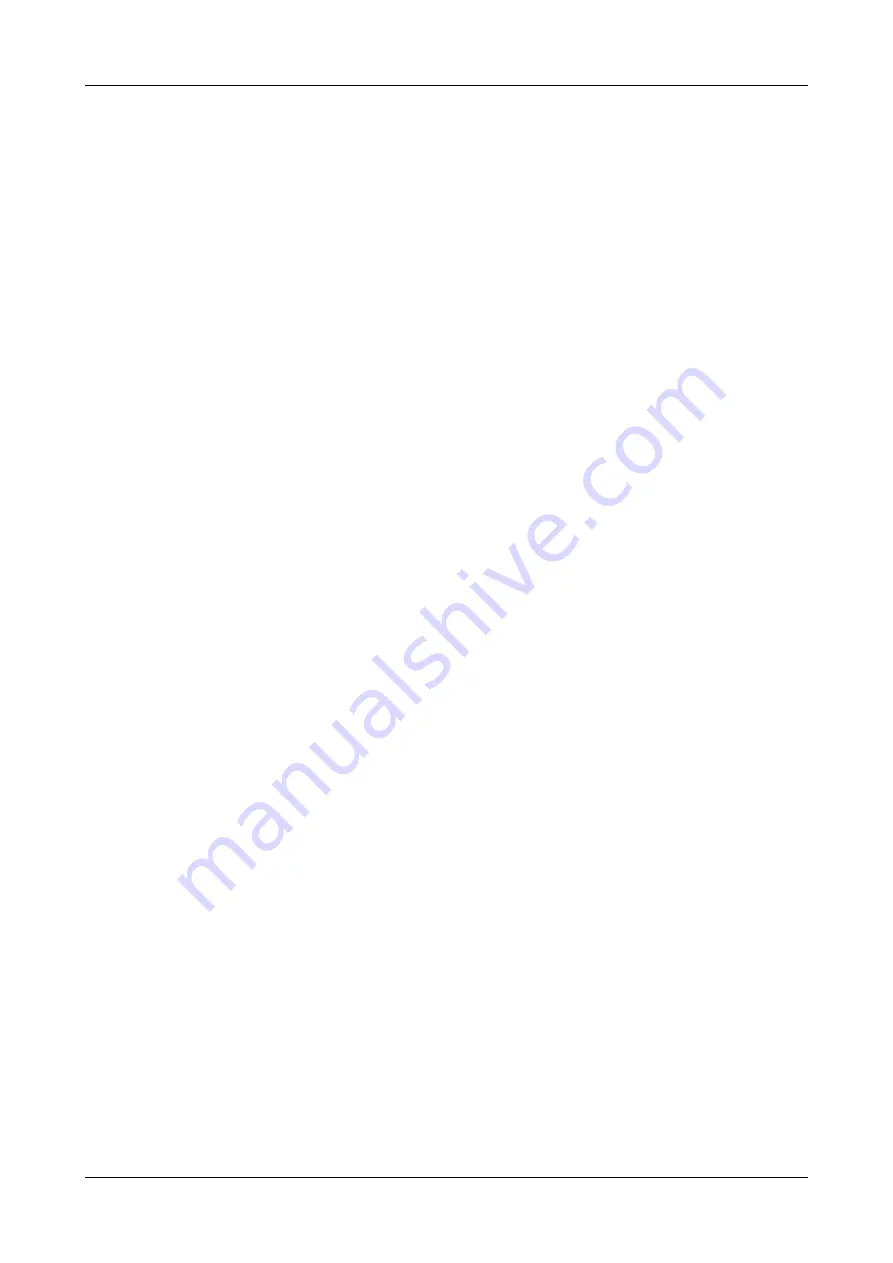
5.5
Filling the tanks
The container outlet must be open during the cleaning process. Thus, it is not a
filling process.
5.6
Inerting
In the case of an explosive atmosphere in the tank and tank dimensions that
exceed the container diameter of 3 m, an inert gas, for example, may only be
introduced so that a formation of mist or sublimate is avoided. Wet steam and
CO
2
are not suitable. Nitrogen and noble gases, for example, are suitable. The
inert gas must be introduced solids-free and slowly through the largest possible
openings.
5.7
Foreign material in the fluids.
There is a risk that a foreign body shoots out of the nozzle when the mesh size of
the sieve has fallen or the sieve is defective (torn). The foreign bodies are
embedded in the liquid, since the operation of the device is only allowed when
liquid is present.
The following applies: The operator must ensure that only permissible media are
used that contain no solids.
Before putting the system into operation, all foreign objects such as screws, nuts
and welding beads must be removed.
The cleaning medium must be removed after spraying and must not be pumped
through the cleaner again. Corresponding preparation is acceptable, the quality
of the medium must be guaranteed and is the duty of care of the operator.
5.8
Petroleum vehicles
The hazardous area for petroleum vehicles is defined in the Ordinance on
Flammable Liquids (TRbF).
5.9
Maintenance / servicing
5.9.1
Authorized personnel / OEM replacement parts
The cleaners may only be serviced and repaired by authorized personnel. Only
OEM spare parts intended for use in potentially explosive atmospheres must be
used, which must be requested from
Breconcherry
.
Changes to the cleaners are not permitted without the consent of the ATEX
officer of
Breconcherry
.
If changes are made or if OEM spare parts are not used for applications in
potentially explosive atmospheres, the enclosed ATEX declarations lose their
validity and their use in potentially explosive atmospheres is no longer permitted.
5.9.2
Maintenance
The cleaner must be regularly checked for damage and function, taking into
account the operating conditions.
Breconcherry
recommends a visual inspection
at every
cleaning process.
Maintenance
Filling the tanks
430BAL011767EN_3
18
28.05.2018