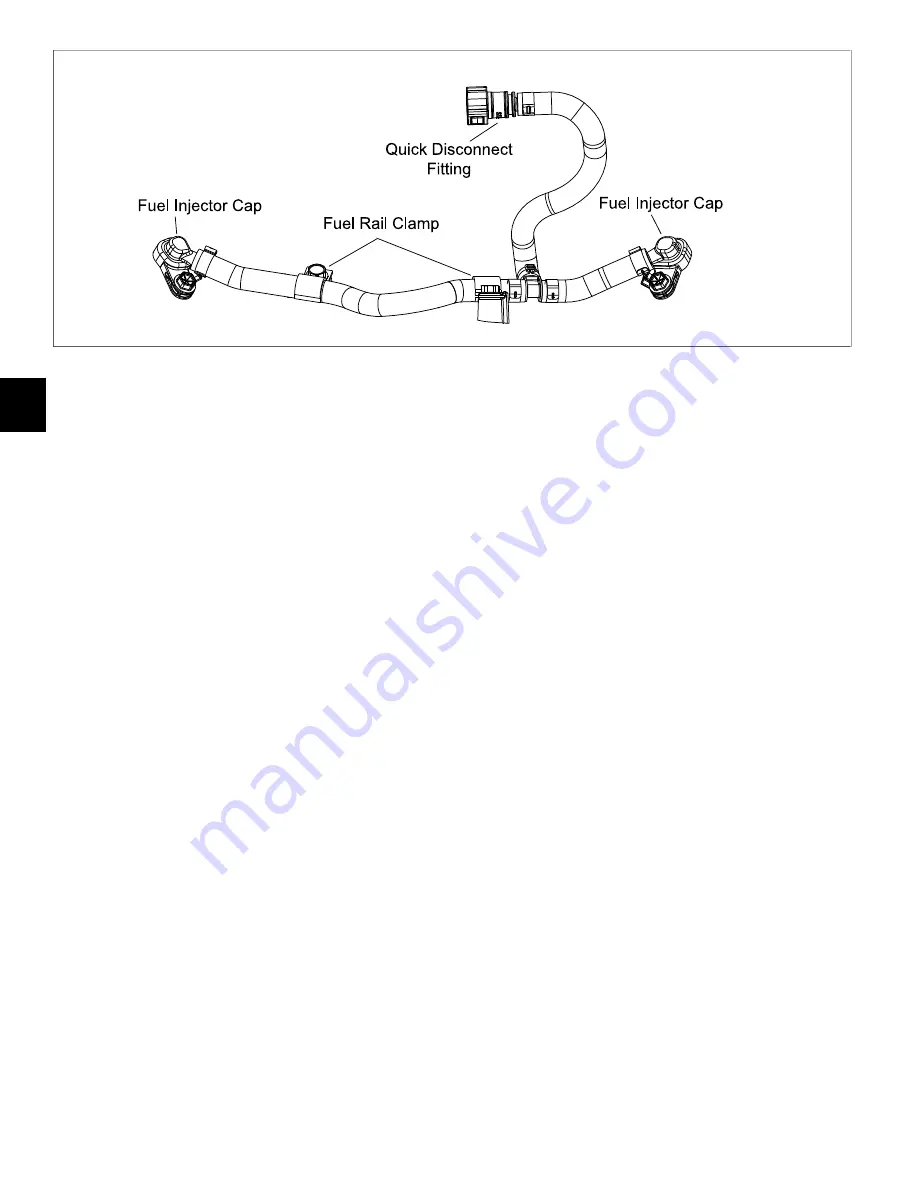
5
126
25
Installation
1. Lightly lubricate fuel injector O-rings with clean
engine oil.
2. Install fuel injectors into intake manifold.
3. Install retaining clips to secure fuel injector caps to
fuel injectors. Orient retaining clips as noted during
removal. Be sure retaining clips are fully engaged.
4. Install two hex flange screws to fasten fuel injector
cap flanges to intake manifold. Tighten screws to
104-122 lb-in
(12-14 Nm).
5. Install two hex flange screws to fasten fuel rail clamps
to intake manifold. Tighten screws to
78-96 lb-in
(9-11 Nm).
6. Connect fuel injector connectors. Push in green
secondary locks to secure.
7. Firmly push quick disconnect fitting onto fuel pump
module. Gently tug on fitting to verify that it is properly
seated and secure.
8. Turn ignition switch ON for two seconds, and then
OFF for 10 seconds. Turn the ignition switch back to
ON and check for fuel leaks.
9. See
Air Cleaner Assembly, Installation
.
10. See
Access Cover/Blower Housing, Installation
.
CKP Sensor
Removal
1. See
Access Cover/Blower Housing, Removal
.
2. Remove two Phillips screws to release CKP sensor
bracket from cylinder mounting bosses.
3. Disconnect CKP sensor connector.
Installation
1. Start two Phillips screws to fasten CKP sensor
bracket to cylinder mounting bosses. Alternately
tighten screws until snug.
2. On side opposite electrical connector, install
mounting plate in groove of CKP sensor housing.
3. Insert CKP sensor into bracket. Align hole in
mounting plate with hole stamped “61” on bracket.
Install TORX screw and tighten to
25-35 lb-in
(3-4
Nm).
4. Loosen two bracket screws and adjust as necessary
until gap between CKP sensor and flywheel tooth is
0.010 inches
(0.254 mm).
5. Alternately tighten CKP sensor bracket screws to
22-35 lb-in
(3-4 Nm).
6. Connect CKP sensor connector.
7. See
Access Cover/Blower Housing, Installation.
Air Cleaner Assembly
Removal
1. Remove plastic knob to release air filter cover.
2. Remove thumb nut from threaded stud.
3. Remove metal retainer plate.
4. Remove air filter element.
5. See A of Figure 26. Remove upper hex flange screws
(
1-2
) to release air cleaner backplate from ECM/fuse
block bracket.
6. Remove lower hex flange screws (
3-4
) to release air
cleaner backplate from fuel pump module bracket.
7. Remove four hex screws (
5-8
) to release carburetor
shield and throttle body adapter from throttle body.
8. See B of Figure 26. Squeeze clip and remove EVAP
tube (to throttle body adapter) from top of fuel pump
module.
Not for
Reproduction
Summary of Contents for VANGUARD M490000
Page 2: ...N o t f o r R e p r o d u c t i o n ...
Page 6: ...N o t f o r R e p r o d u c t i o n ...
Page 84: ...3 80 MODEL 490000 EFI ELECTRICAL SCHEMATIC PAGE 1 OF 2 N o t f o r R e p r o d u c t i o n ...
Page 85: ...3 81 MODEL 490000 EFI ELECTRICAL SCHEMATIC PAGE 2 OF 2 N o t f o r R e p r o d u c t i o n ...
Page 95: ...3 91 MODELS 490000 540000 610000 FUSE RELAY BLOCK N o t f o r R e p r o d u c t i o n ...
Page 96: ...3 92 N o t f o r R e p r o d u c t i o n ...
Page 110: ...4 106 N o t f o r R e p r o d u c t i o n ...
Page 115: ...5 111 This page is intentionally left blank N o t f o r R e p r o d u c t i o n ...
Page 134: ...5 130 30 N o t f o r R e p r o d u c t i o n ...
Page 137: ...5 133 This page is intentionally left blank N o t f o r R e p r o d u c t i o n ...
Page 138: ...5 134 32 N o t f o r R e p r o d u c t i o n ...
Page 140: ...5 136 33 N o t f o r R e p r o d u c t i o n ...
Page 142: ...5 138 This page is intentionally left blank N o t f o r R e p r o d u c t i o n ...