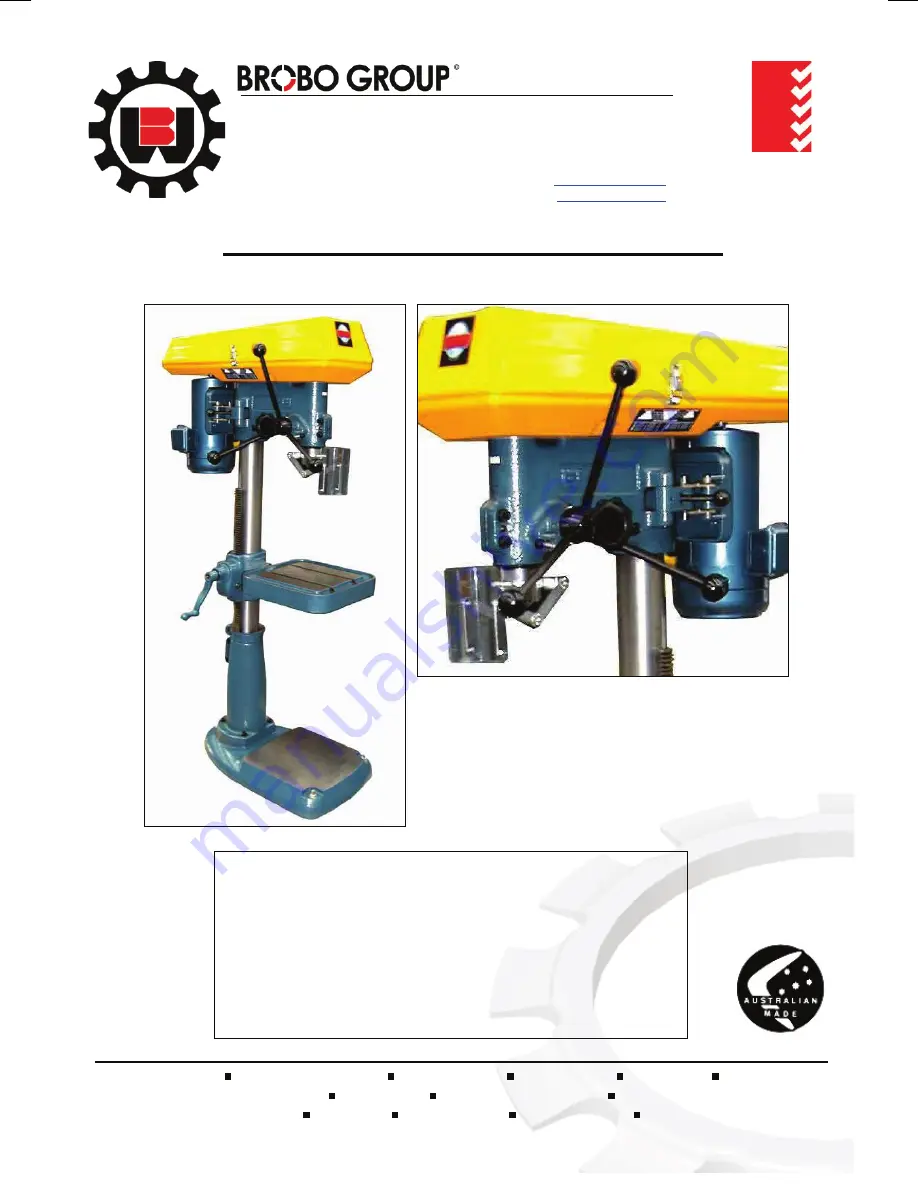
Precision Drilling Machines Tapping Machines Multi Head Drills Tool Grinders
Machine Vices Special Production Equipment
Accessories Pedestal Grinders Metal Cutting Saws
PRODUCT AND MAINTENANCE MANUAL
3M PRECISION DRILLING MACHINE
BROBO WALDOWN (AUST) PTY. LTD.
A.C.N.
098 264 316
A.B.N.
42 098 264 316
65-67 Williams Rd, Dandenong, 3175
PO BOX 4274 Dandenong Sth, 3164
Victoria, AUSTRALIA.
Tel:
61 3 9794 8751
Email:
info@brobo.com.au
Fax:
61 3 9794 8792
Website:
www.brobo.com.au
C
er
ti
fi
ed
S
ys
te
m
Quality
ISO 9001
YOUR
NORTH AMERICAN
BROBO DISTRIBUTOR IS:
Summary of Contents for 3M
Page 12: ...CHAPTER 4 Drawings Layouts Assembly and Spare Parts 4 1 1 Assembly Drawing Sheet 1 of 5 9 ...
Page 13: ...4 1 2 Assembly Drawing Sheet 2 of 5 10 ...
Page 14: ...4 1 3 Assembly Drawing Sheet 3 of 5 11 ...
Page 15: ...4 1 4 Assembly Drawing Sheet 4 of 5 12 ...
Page 17: ...4 2 Switch Assembly 14 ...