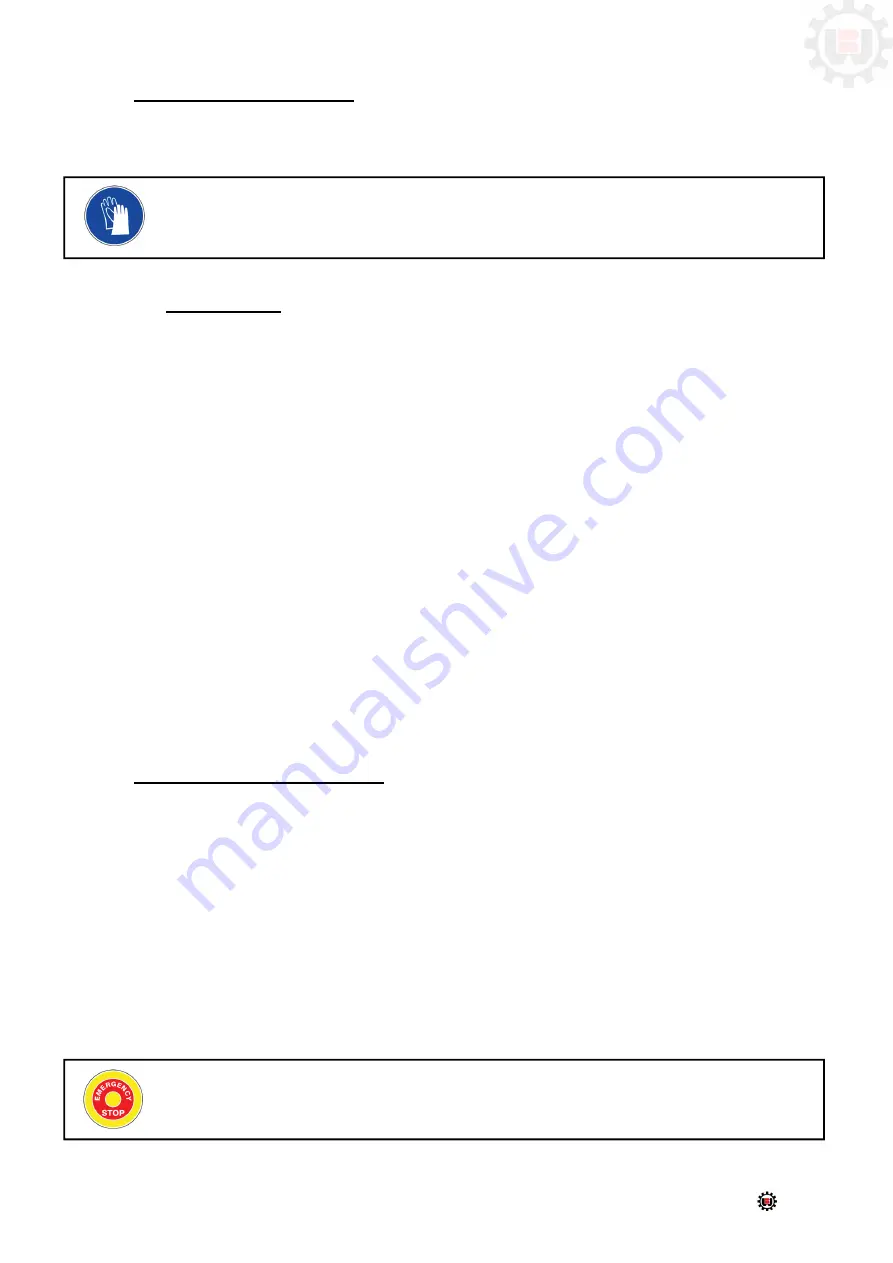
Brobo Group
brobo.com.au
Preparation for Operation
The following procedure is recommended for the correct drilling using the
Brobo Group
Drill
.
PROCEDURE
1) Clean the workpiece to ensure it is free of any grit, swarf or flammable substances. It is highly recommended
that a solvent is used to remove any residue while ensuring the solvent is inflammable and non-toxic.
2) Prior to drilling, clear the drill & the work area around the workpiece of any swarf or/and tools to minimise
the likelihood of the user getting injured during the drilling operation.
3) Load the workpiece into the mechanical vice (sold separately), located on the rack lift, & fastened workpiece
securely. Loosen the rack lift & adjust the height & horizontal position. Once you have positioned the
workpiece into the desired location, relock the rack lift assembly.
4) Check that the correct speed drill speed setting is selected, & the safety eye shield is directly positioned to
deflect swarf & any dislodged particles.
5) Turn the machine on. Proceed by slowly drilling into the workpiece until a guide indent is created. Steadily
increase the feed rate of drilling by applying a constant yet steady force on the feed handle until the desired
hole depth is reached.
6) Reverse the direction of the drill fed until it comes to rest in its start position & turn the drill machine off.
Operation Recommendations
To reduce the amount of frictional contact between the drill bit & workpiece, a light coating of oil or lubricant
can be applied to the drill bit price to drilling.
Do not force the drill bit through the workpiece as this significantly reduces the lifespan of the bit, as well as
increasing the risk of the bit bending and/or breaking & injuring the operator.
When drilling through larger hole diameters through thick materials, it is advisable to split the drilling
operation into two or three stages, starting from drilling a smaller hole size & increasing it until the desired
final hole size.
WARNING – SAFETY GEAR
Protective clothing, safety glasses and gloves should
always
be worn while loading
parts, operating the machine, or undertaking any maintenance work on the
machine
.
WARNING - JAMMING
If the drill jams during a drill, engage the EMERGENCY STOP immediately. Remove the part,
check that the drill bit is not damage and if need be, replace the drill bit.
Summary of Contents for BDF32-1
Page 6: ...1 Outline Drawing Figure 1 BDF 32 1 ...
Page 9: ...Figure 2 Drawing of Transmission System ...
Page 11: ......
Page 14: ...Figure 7 Installation of Foundation ...
Page 17: ...9 Assembly Drawings Spare Parts List ...
Page 18: ......
Page 21: ......
Page 27: ......