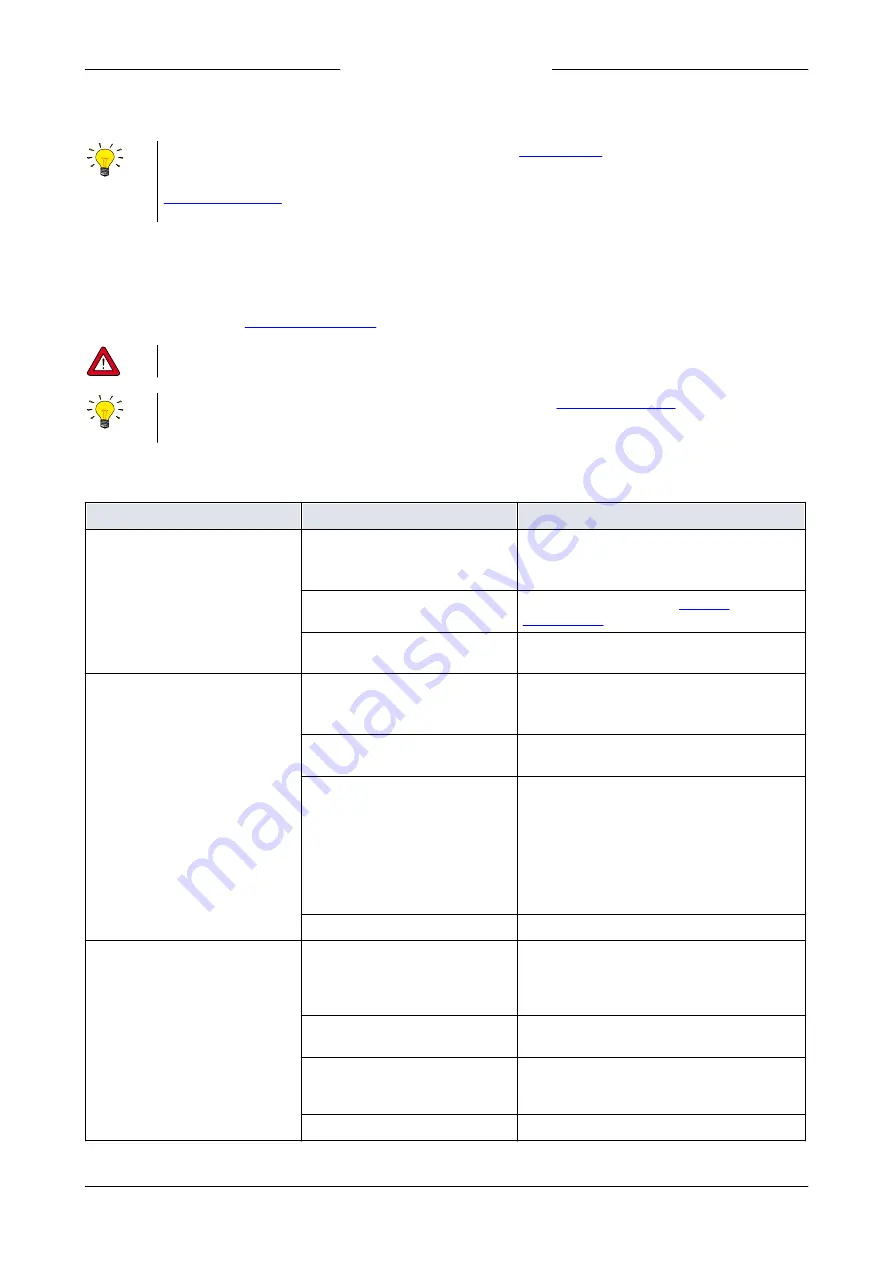
Bronkhorst®
Instruction Manual mini CORI-FLOW ML120
9.17.097G
60
6
Troubleshooting and service
During operation, the LEDs can indicate errors and/or warnings. See
for an explanation of the possible LED
indications.
Error and warning information can also be found by connecting the instrument to FlowDDE and FlowPlot (see section
). FlowDDE puts all errors and warnings on the console screen; in FlowPlot, the Alarm & Count tab
(Instrument Settings) provides several specific alarm and counter indicators.
6.1
Restoring factory settings
In case changes to the instrument configuration leads to non-recoverable erroneous behavior, the instrument can be reset
to the pre-configured factory settings. This can be done in FlowPlot (Instrument Settings > Restore Settings) or with the
multifunctional switch (see
).
Changes made to the network settings (bus address, baud rate, parity) will
not
be restored by a factory reset.
If digital communication with the instrument can not be re-established, see
mode, overrule the 9-pin D-sub communication settings and use the RS232 communication mode to re-establish
communication.
6.2
Common issues
Symptom
Possible cause
Action
No fieldbus communication
No power supply
·
Check power supply
·
Check cable connection
·
Check cable hook-up
Invalid node address
Change node address (see
Other
Reset instrument and/or restart master. Contact
Bronkhorst if problem persists.
No output signal
No power supply
·
Check power supply
·
Check cable connection
·
Check cable hook-up
Inlet pressure or differential
pressure too low
Increase inlet pressure
Piping, filters and/or control valve
clogged or blocked
·
Clean system (flush with clean, dry air or a
non-aggressive cleaning liquid (e.g. ethanol
or isopropyl alcohol)
·
For external proportional control valves:
supply 0…15 Vdc and operational inlet
pressure to valve and slowly increase
voltage. If valve does not open, clean parts
and re-adjust valve
Sensor failure
Return equipment to factory
·
Control behavior unstable
·
Red LED flashes irregularly
Measurement disturbed by
mechanical vibration
·
If possible, avoid installation in close
proximity of mechanical vibration
·
Reduce sensitivity to vibrations by using a
mass block, dampeners, and flexible tubing
Inlet pressure unstable
Eliminate pressure fluctuations, e.g. by
installing a pressure regulator
Gas accumulation in tubing
Flush the system to remove gas
Tip: use frequency or density signal to detect
presence of gas bubbles
Wrong controller settings
Adjust settings (e.g. with FlowPlot)