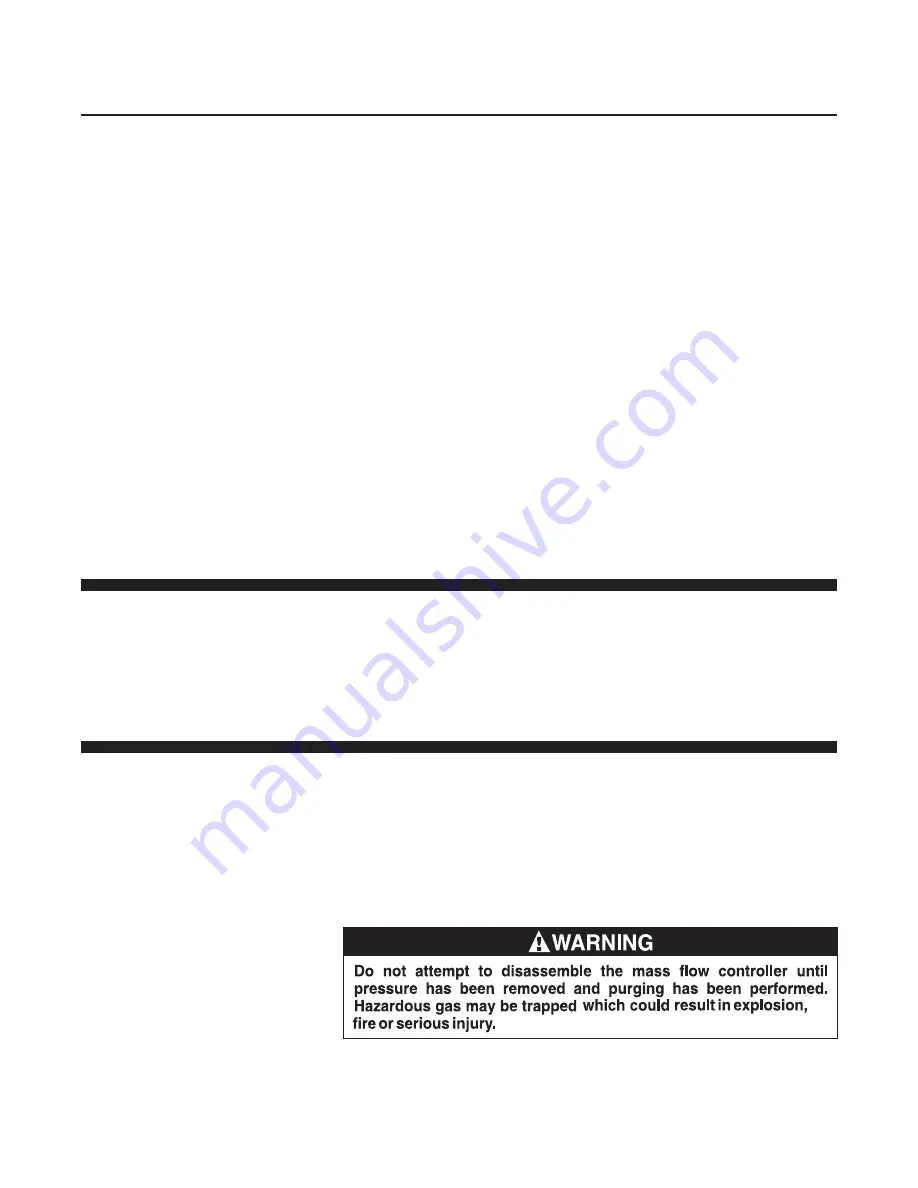
Brooks
®
Model 5860
i
4-4
Section 4 Maintenance
Installation and Operation Manual
X-TMF-5860i-MFM-eng
Part Number: 541B110AAG
November, 2008
An alternate method for flushing out the sensor is to replace the restrictor
element with a low flow plug restrictor. This plug forces all the flow through
the sensor and may dislodge any obstructions. Subject the flow meter to a
high differential pressure. Pressurizing the outlet of the flowmeter higher
than the inlet may help force the obstruction upstream and out of the
sensor tube.
4. Deposits of silicon dioxide may be removed by soaking the internal
parts in solution of 5% hydrofluoric acid (5 parts hydrofluoric acid
(HF), 95 parts water (H
2
O)) followed by Freon TF.
5. Wire mesh and A.C.L.F.E. type restrictor elements can be cleaned in
an ultrasonic bath. Refer to Section 4-7 for the correct restrictor to
use.
6. Blow all parts dry with dry nitrogen and reassemble. Refer to Section
4-4b (assembly).
7. Purge the assembled controller with dry nitrogen.
8. Perform the calibration procedure in Section 3-4.
9. When the flowmeter is reinstalled in the system, the connections
should be leak tested and the system should be purged with dry
nitrogen for 30 minutes prior to start-up to prevent the formation of
deposits.
4-3 Sensor Tube
The sensor tube is part of a calibrated flow divider that is designed to
operate within a preset gas flow range. The sensor assembly may be
removed or replaced by referring to Section 4-4, Disassembly and
Assembly. If the sensor assembly is cleaned and reinstalled, a calibration
check should be performed. Refer to Section 3-4.
4-4 Disassembly and Assembly
The Model 5860
i
Mass Flowmeter may be disassembled in the field by the
user for cleaning, re-ranging or servicing. Disassemble and assemble the
meter as follows:
NOTE: The 5860
i
Mass Flowmeter should be disassembled and
assembled in a clean environment to prevent particulate
contamination.
A. Disassembly
The numbers in ( ) refer to the spare parts exploded view in Figure 5-1.