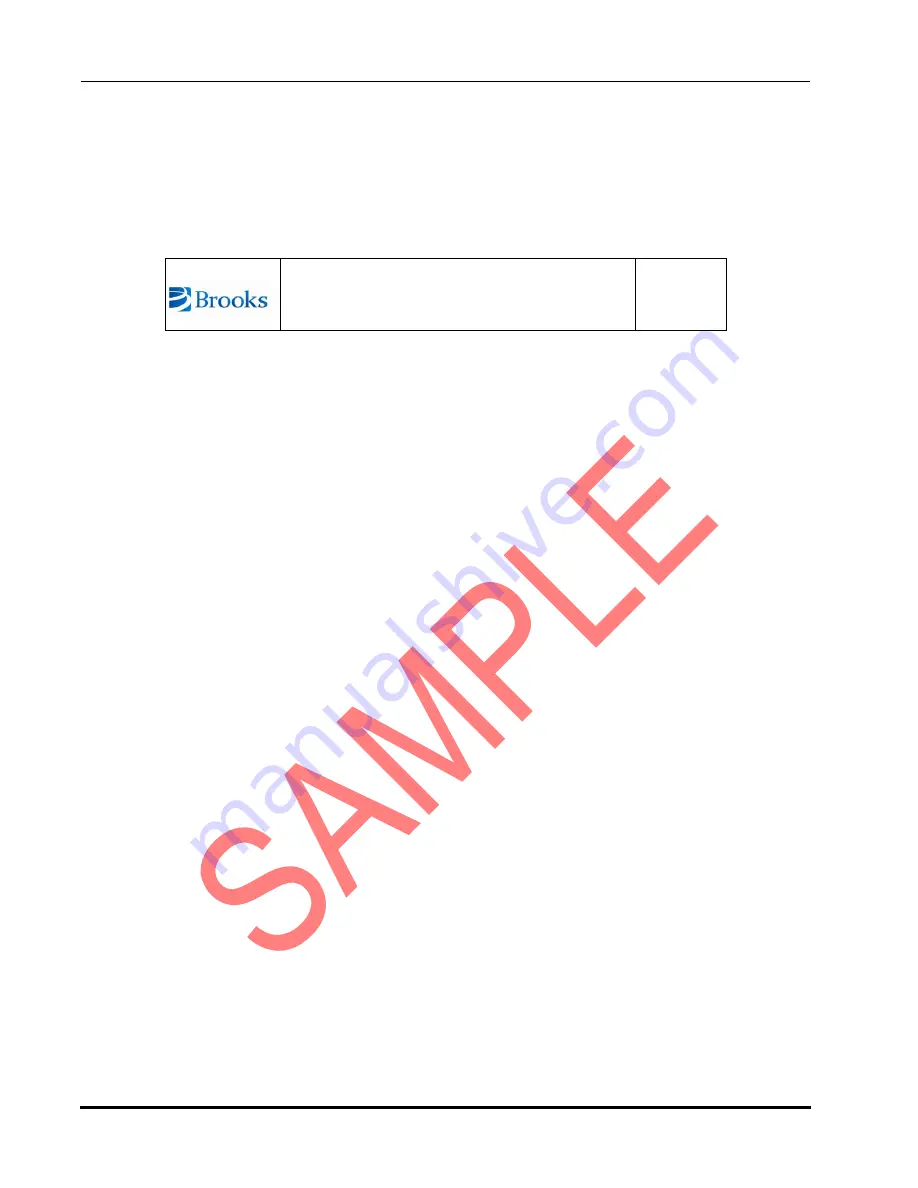
Introduction
Polycold Cryochiller
Regulatory Compliance
Installation and Operation Manual
Brooks Automation
1-14
214072 Revision B
Declaration of Incorporation (DOI)
When the Polycold Cryochiller is supplied for integration into a system, the final integrator is overall
responsible for conformity to the applicable directives and safety systems. When the system has the CE
mark, the Cryochiller becomes an incorporated component and the attached Declaration of Incorpora-
tion applies.
Declaration of Incorporation
of Partly Completed Machinery
For the European Union
Document #:
Rev
Description:
Polycold® Cryogenic Refrigeration Unit,
Function:
Closed loop cryogenic refrigeration water vapor recovery
system
Models:
XC8800 MT, XC8800 HC, MaxCool 4000H, MaxCool 2500L.
Part Number:
Serial Number:
Business name and full address of the manufacturer of the partly completed machinery:
Brooks Automation Inc., 15 Elizabeth Drive, Chelmsford, MA, USA 01824
Name and address of the person, established in the Community, authorized to compile the relevant technical documentation:
Brooks Automation (Germany) GmbH, Ernst-Ruska-Ring 11, 07745 Jena, Germany
The manufacturer declares:
x
That the following essential requirements of Machinery Directive 2006/42/EC are applied and
fulfilled and that the relevant technical documentation is compiled in accordance with part B of
Annex VII:
Annex I sections:
1.1.2, 1.1.3, 1.1.5, 1.1.6, 1.2.1, 1.2.2, 1.2.3, 1.2.4, 1.2.5, 1.2.6, 1.3.1, 1.3.2,
1.3.4, 1.5.1, 1.5.2, 1.5.3, 1.5.4, 1.5.5, 1.5.6, 1.5.7, 1.5.8, 1.5.9, 1.5.11, 1.6.1, 1.6.3, 1.6.4,
1.7.1, 1.7.2, 1.7.3
o
EN 60204-1
x
That the safety objectives set out in directive 2006/95/EC (LVD) have been applied to the partly
completed machinery.
x
That this partly completed machinery conforms with the provisions of Electromagnetic
Compatibility Directive 2004/108/EC.
o
EN 61000-6-4
o
EN 61000-6-2
x
That this partly completed machinery fulfills all the relevant provisions of Directive 97/23/EC
(Pressure Equipment Directive).
o
PED Category:
II
o
Conformity Assessment:
Module A1
o
Notified Body:
TÜV SÜD Industrie Service GMBH (NB #0036)
WestendStrasse, 80686, Munchen, Germany
o
Standards:
EN 378, EN 60204-1, EN ISO 12100-1, -2
x
We will transmit, in response to a reasoned request by a national authority, relevant information
on the partly completed machinery, on paper or in electronic form, without prejudice to our
intellectual property rights.
The partly completed machinery must not be put into service until the final machinery into which it is
incorporated has been declared in conformity with the provisions of Directive 2006/42/EC
Signature
Name of signatory
date of declaration
Title of signatory
place of declaration