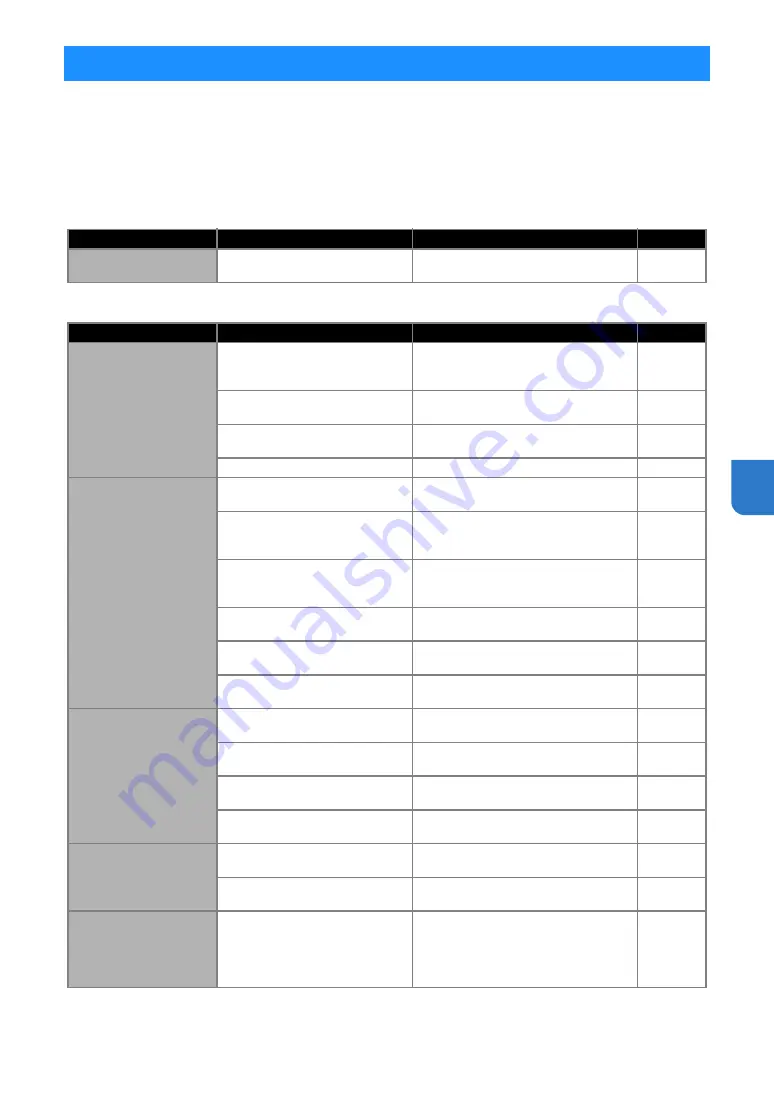
109
7
Please pay attention to all applicable safety warnings when referring to the sections cited below.
If the machine stops operating correctly, check the following possible problems before requesting service.
You can solve most problems by yourself. If you need additional help, the Brother support website offers the
latest FAQs and troubleshooting tips. Visit us at “ http://s.brother/cpoac/ ”.
If the problem persists, contact the retailer who sold you this machine or the nearest authorized service center.
For wireless network troubleshooting, refer to “WIRELESS NETWORK CONNECTION FUNCTION” on page 85.
Power Supply
Mat
TROUBLESHOOTING
Symptom
Possible Causes (or Results)
Solutions
Reference
The machine cannot be
turned on.
The AC power cord is not correctly
connected to the machine.
Check that the power cord is connected
to the electrical outlet.
Symptom
Possible Causes (or Results)
Solutions
Reference
The mat cannot be
inserted.
When the mat was inserted, it was
not placed under the feed rollers.
Insert the mat so that it is placed under
the feed rollers on the left and right sides
of the feed slot.
The mat was not loaded using the
“Feed” button.
Lightly insert the mat into the feed slot,
and then press the “Feed” button.
The feed roller is not positioned
correctly.
Adjust the position of the feed roller.
The shaft is released.
Lock the shaft.
The mat cannot be
recognized.
The dotted marks on the part of the
mat that is inserted are dirty.
Clean the dotted marks on the mat and
their surrounding area.
The dotted marks on the part of the
mat that is inserted are hidden by
material or tape that was attached.
Attach the material or tape while keeping
it within the adhesive area of the mat.
The mat was inserted so that the
side with the material attached is
facing down.
Insert the mat so that the side with the
material attached is facing up.
The mat was inserted in the wrong
direction.
Insert the mat in the correct direction.
The scanner glass is dirty.
Clean the scanner glass inside the
machine.
A mat designed specifically for this
machine is not used.
Replace the mat with one designed
specifically for this machine.
—
The mat is fed in at an
angle.
The mat was inserted into the feed
slot at an angle.
Press the “Feed” button to feed out the
mat, and then re-insert it straight in.
The corners of the mat are
deformed (bent).
Replace the mat with a new one.
The rear tray is not pulled out.
Pull out the rear tray.
The feed roller is not positioned
correctly.
Adjust the position of the feed roller.
The material to be cut/
drawn or original to be
scanned cannot be
attached to the mat.
The material extends from the
adhesive area of the mat.
Attach the material while keeping it
within the adhesive area of the mat.
The mat’s adhesive strength has
decreased.
Replace the mat with a new one.
The mat cannot be fed
out.
The material to be cut/drawn or
original to be scanned is jammed in
the feeding mechanism in the
machine.
Press the “Feed” button while the mat is
being inserted to feed it out.
If the mat does not feed out, turn off the
machine, and then carefully pull out the
mat.