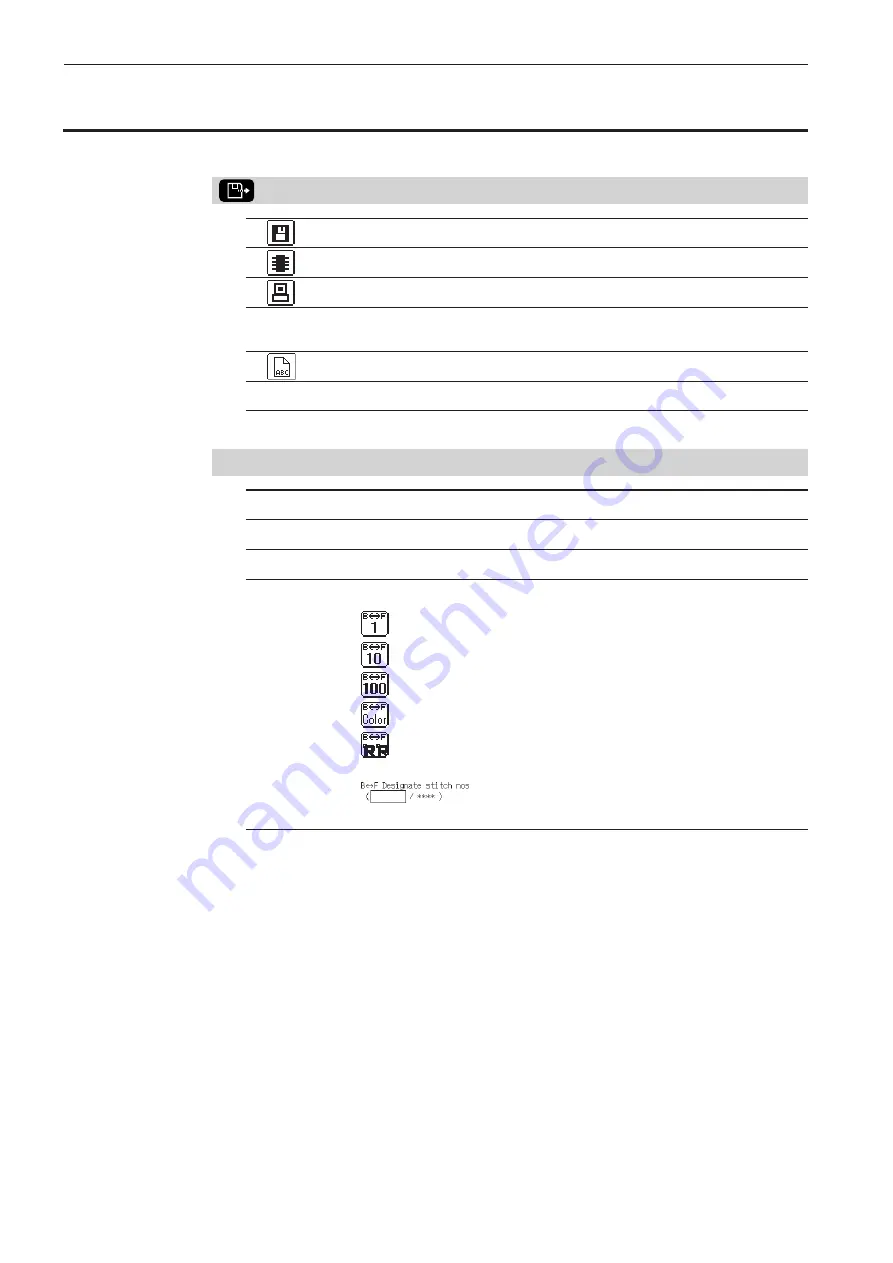
BES-961BC • BES-1261BC
60
Chapter 3 Selection of Data and Embroidering
What Can the Machine Do?
Selection of Embroidery Data
Registration of data from the floppy disk (
→
Page 61)
Reading of data from the memory (
→
Page 64)
Registration of data created by BE-100 (
→
Page 65)
(These icons are displayed in the lower right of the screen.)
Modification of data name (
→
Page 68)
Deletion of embroidery data (
→
Page 66)
Embroidering Operation
Embroidering start (
→
Page 72)
Embroidering feedhold (
→
Page 73)
Embroidering cancel (
→
Page 73)
Step forward/step back (
→
Page 74)
Step forward (back) stitch by stitch
Step forward (back) by every 10 stitches
Step forward (back) by every 100 stitches
Step forward (back) until a next color change
Step forward (back) to the embroidering start point
of a next pattern
Step forward (back) by a specified number of
stitches (
→
Page 74)
Summary of Contents for BES-1261BC
Page 7: ...5 BES 961BC BES 1261BC 2 1 7 1 6 3 4 5 7 3 2 Belt cover Finger guard BES 961BC ...
Page 13: ...11 BES 961BC BES 1261BC Setting of thread breakage sensor page 93 Setting of Machine page 96 ...
Page 18: ...16 BES 961BC BES 1261BC ...
Page 19: ...Chapter 1 Preparation of Embroidery Machine ...
Page 60: ...BES 961BC BES 1261BC 58 Chapter 2 Embroidering Procedures ...
Page 78: ...BES 961BC BES 1261BC 76 Chapter 3 Selection of Data and Embroidering ...
Page 118: ...BES 961BC BES 1261BC 116 Chapter 5 Setting ...
Page 119: ...Chapter 6 Operation of Machine ...
Page 130: ...Chapter 6 Operation of Machine BES 961BC BES 1261BC 128 ...
Page 131: ...Chapter 7 Maintenance ...
Page 140: ...Chapter 7 Maintenance BES 961BC BES 1261BC 138 ...
Page 141: ...Chapter 8 Standard Adjustment ...
Page 153: ...Chapter 9 List of Error Messages ...
Page 161: ...Connection and Installation of Optional Equipment ...