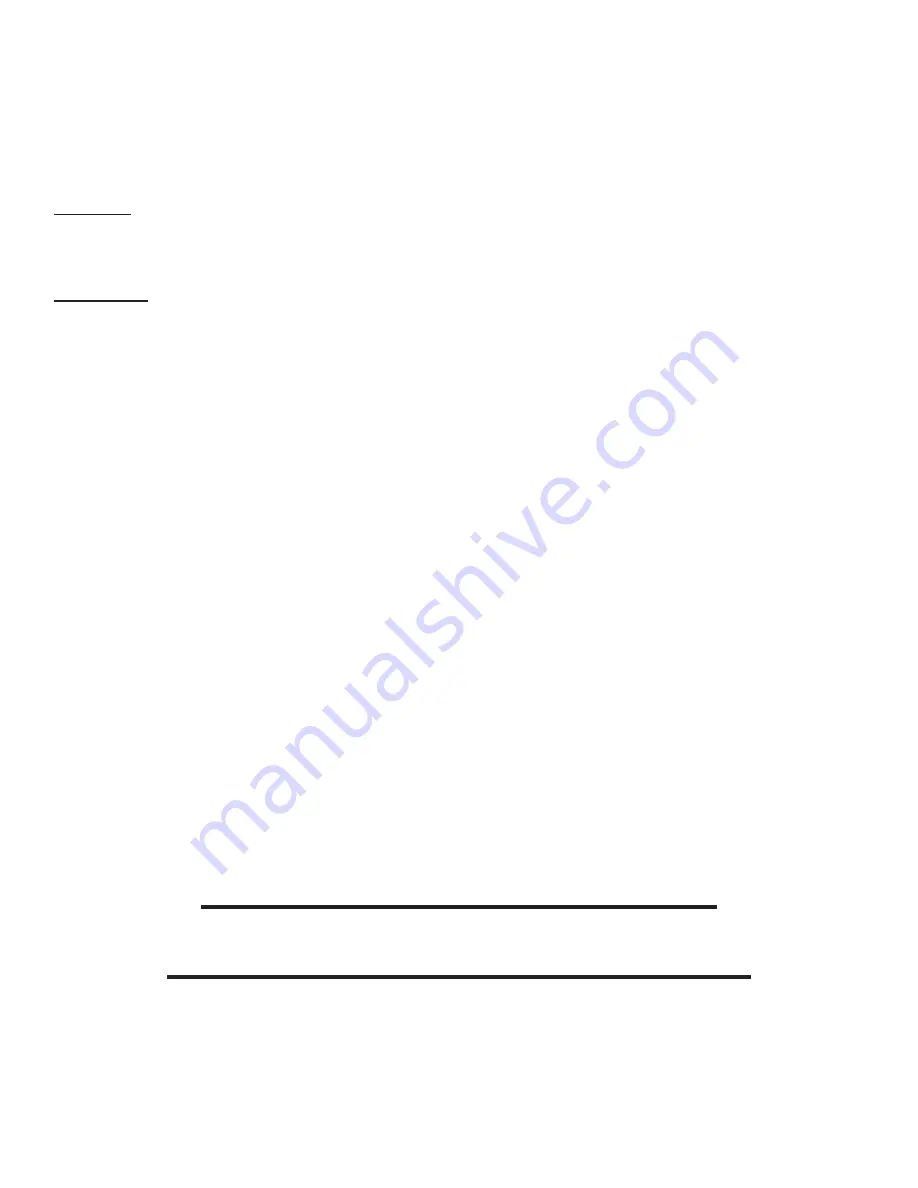
IMPORTANT SAFETY INSTRUCTIONS
When using an electrical machine, basic safety precautions should always be followed, including the
following:
Read all instructions before using (this machine).
DANGER
- To reduce the risk of electric shock:
1.
The machine should never be left unattended when plugged in. Always unplug this machine from
the electric outlet immediately after using and before cleaning.
WARNING
- To reduce the risk of burns, fire, electric shock, or injury to persons:
1.
Do not allow this machine to be used as a toy. Close attention is necessary when this machine is
used by or near children.
2.
Use this machine only for its intended use as described in this manual. Use only attachments
recommended by the manufacturer as contained in this manual.
3.
Never operate this machine if it has a damaged cord or plug, if it is not working properly, if it has
been dropped or damaged, or dropped into water. Return the machine to the nearest authorized dealer
or service center for examination, repair, electrical or mechanical adjustment.
4.
Never operate the machine with any air openings blocked. Keep ventilation openings of the sewing
machine free from the accumulation of lint, dust, and loose cloth.
5.
Never drop or insert any object into any opening.
6.
Do not use outdoors.
7.
Do not operate where aerosol (spray) products are being used or where oxygen is being administered.
8.
To disconnect, turn all controls to the off position, then remove the plug from the outlet.
9.
Do not unplug by pulling on cord. To unplug, grasp the plug, not the cord.
ii)
Keep fingers away from all moving parts. Special care is required around the sewing machine
needle.
iii)
Always use the proper needle plate. The wrong plate can cause the needle to break.
iv)
Do not use bent needles.
v)
Do not pull or push fabric while stitching. It may deflect the needle causing it to break.
vi)
Switch the sewing machine off when making any adjustments in the needle area, such as
threading needle, changing needle, threading bobbin, or changing presser foot, etc.
vii)
Always unplug sewing machine from the electrical outlet when removing covers, lubricating,
or when making any other user servicing adjustments mentioned in the instruction manual.
Connect this machine to a properly grounded outlet only. See Grounding Instructions.
SAVE THESE INSTRUCTIONS
Do not discard box or packaging
3