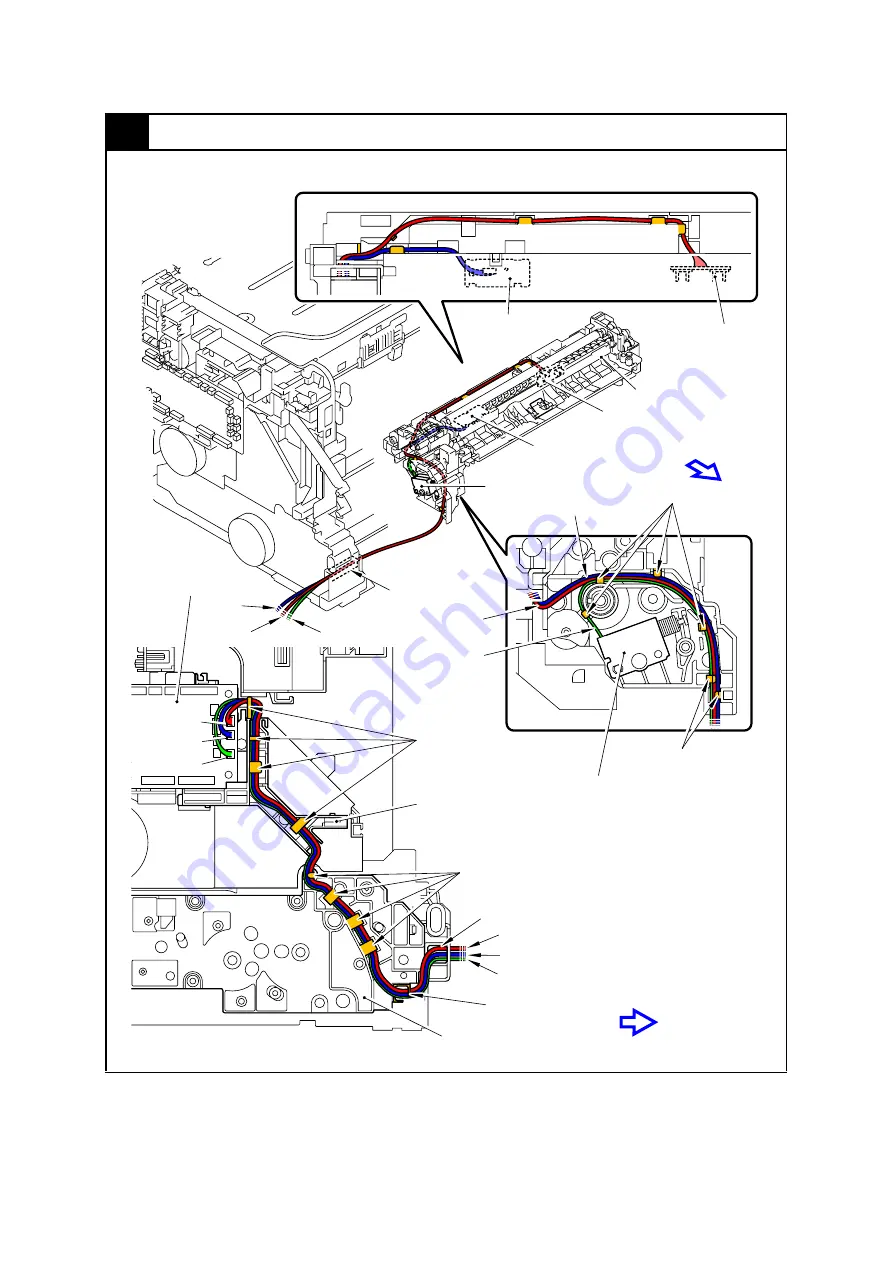
3-19
Confidential
12
PF ASSY
Front
Front
PF ASSY
Hook
Hook
Hook
Hook
Hook
T1 registration
front/rear sensor
PCB ASSY
T1 registration front/rear
sensor PCB ASSY
T1 paper edge sensor PCB ASSY
MP sector solenoid
Hole
“a”
“b”
“c”
“a”
Engine PCB ASSY
“b”
“c”
MP sector solenoid
“c”
“b”
“a”
PF line holder
CN13
CN10
CN8
PF cleaner drive ASSY
Hole
T1 paper edge sensor
PCB ASSY
Summary of Contents for HL-4140CN
Page 19: ...Confidential CHAPTER 1 SPECIFICATIONS ...
Page 29: ...Confidential CHAPTER 2 ERROR INDICATION AND TROUBLESHOOTING ...
Page 145: ...Confidential CHAPTER 3 DISASSEMBLY AND ASSEMBLY ...
Page 169: ...3 21 Confidential 8 DISASSEMBLY FLOW Disassembly Re Assembly second ...
Page 296: ...Confidential CHAPTER 4 ADJUSTMENTS AND UPDATING OF SETTINGS REQUIRED AFTER PARTS REPLACEMENT ...
Page 311: ...Confidential CHAPTER 5 SERVICE FUNCTIONS ...
Page 336: ...5 23 Confidential Inter color position alignment adjustment chart Fig 5 8 ...
Page 343: ...5 30 Confidential Fig 5 11 ...
Page 345: ...5 32 Confidential Fig 5 12 First side Second side ...
Page 347: ...5 34 Confidential Color test pattern Fig 5 13 MCYK Y C K M YCMK_ _A ...
Page 354: ...5 41 Confidential Maintenance information Fig 5 14 ...
Page 382: ...Confidential CHAPTER 6 CIRCUIT DIAGRAMS WIRING DIAGRAM ...
Page 384: ...6 1 Confidential 1 CIRCUIT DIAGRAMS High voltage Power Supply PCB Circuit Diagram 1 3 ...
Page 385: ...6 2 Confidential High voltage Power Supply PCB Circuit Diagram 2 3 ...
Page 386: ...6 3 Confidential High voltage Power Supply PCB Circuit Diagram 3 3 ...
Page 387: ...6 4 Confidential Low voltage Power Supply PCB Circuit Diagram 100V ...
Page 388: ...6 5 Confidential Low voltage Power Supply PCB Circuit Diagram 200V ...
Page 389: ...6 6 Confidential 2 WIRING DIAGRAM Wiring Diagram ...
Page 390: ...Confidential CHAPTER 7 PERIODICAL MAINTENANCE ...
Page 424: ...Confidential APPENDIX 1 SERIAL NUMBERING SYSTEM ...
Page 428: ...Confidential APPENDIX 3 INSTALLING THE MAINTENANCE DRIVER ...
Page 432: ...App 3 4 Confidential 10 Alert warning message appears click Continue Anyway to proceed ...