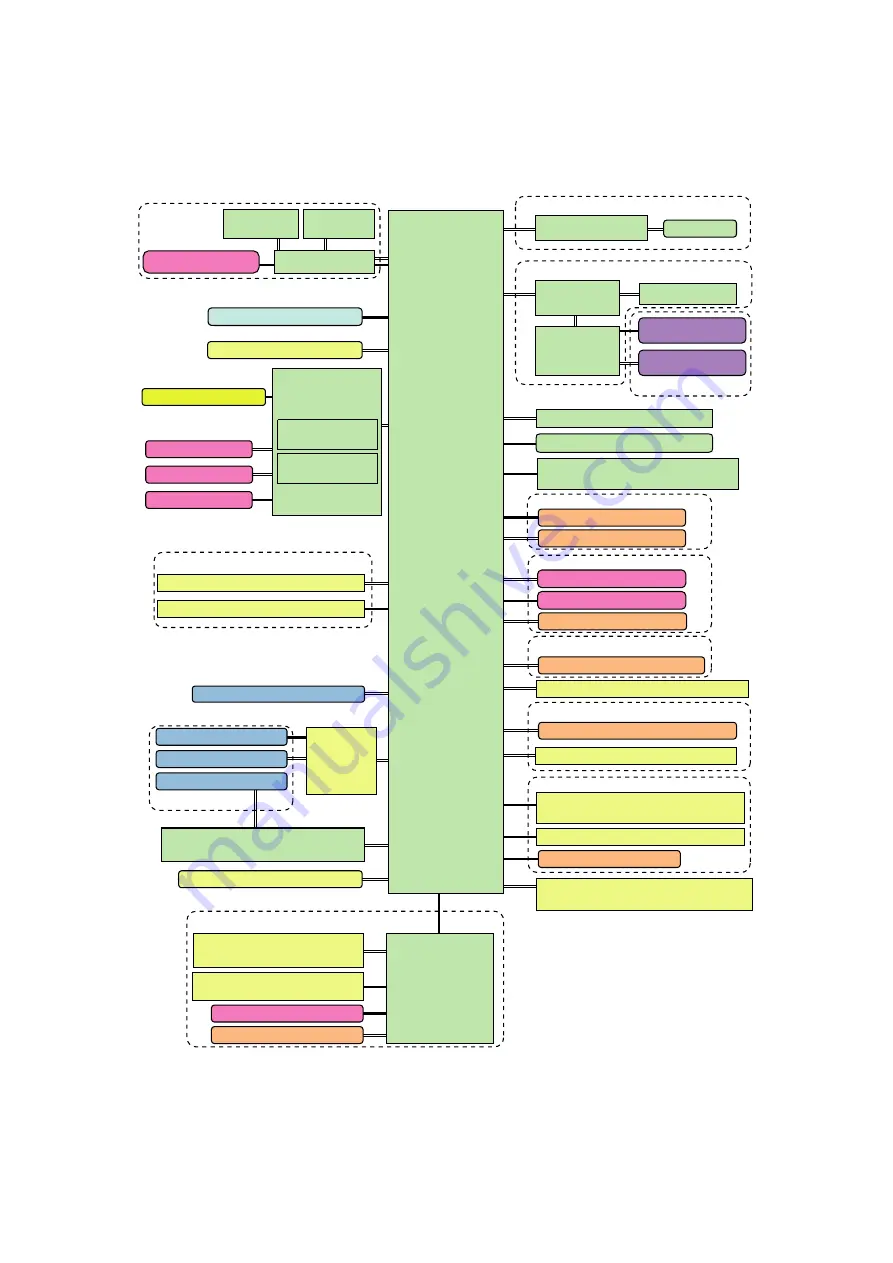
2-8
Confidential
2.4 Block Diagram
Fig. 2-3
Paper eject origin sensor
Laser unit
Control panel
Control panel
Registration mark sensor unit
LCD unit
Main drive unit
Process drive unit
Paper feed unit
Paper eject ASSY
T2 paper tray unit
T2 paper tray unit
USB host relay PCB ASSY
Front cover sensor
Process motor
Main motor
Back cover sensor ASSY
MP registration front sensor
Toner/new sensor PCB ASSY
(Light reception)
Develop release sensor PCB ASSY
T1 paper feed sensor PCB ASSY
Registration front/rear sensor
PCB ASSY
MP solenoid
Registration solenoid
Internal temperature sensor
Center thermistor
Fuser fan
T1 solenoid
Develop clutch
Power fan
Blower
T2 paper feed/
plate origin sensor PCB
T2 solenoid
T2 plate motor
T2 registration sensor PCB
T2 relay PCB
ASSY
2Line LCD
Panel PCB ASSY
Wireless LAN PCB
MP paper empty/
registration front sensor PCB ASSY
Registration mark sensor L PCB
Waste toner sensor
Eject
sensor
PCB ASSY
Registration mark sensor R PCB
LD PCB ASSY
Polygon motor
Side thermistor
Heater
Low-voltage power supply
PCB unit
High-voltage
power supply
PCB ASSY
Toner sensor
(Light emission)
EL emission
circuit
External temperature/
humidity sensor
Fuser unit
Fuser unit
Main PCB ASSY
Develop release clutch
Develop release drive unit
Switch back solenoid
Panel control
PCB ASSY
1.8-inch Color LCD
Touch panel
Key PCB ASSY
Model with touch panel
Model without touch panel
Panel relay
PCB ASSY
LD SUB
PCB ASSY
BD sensor
PCB ASSY