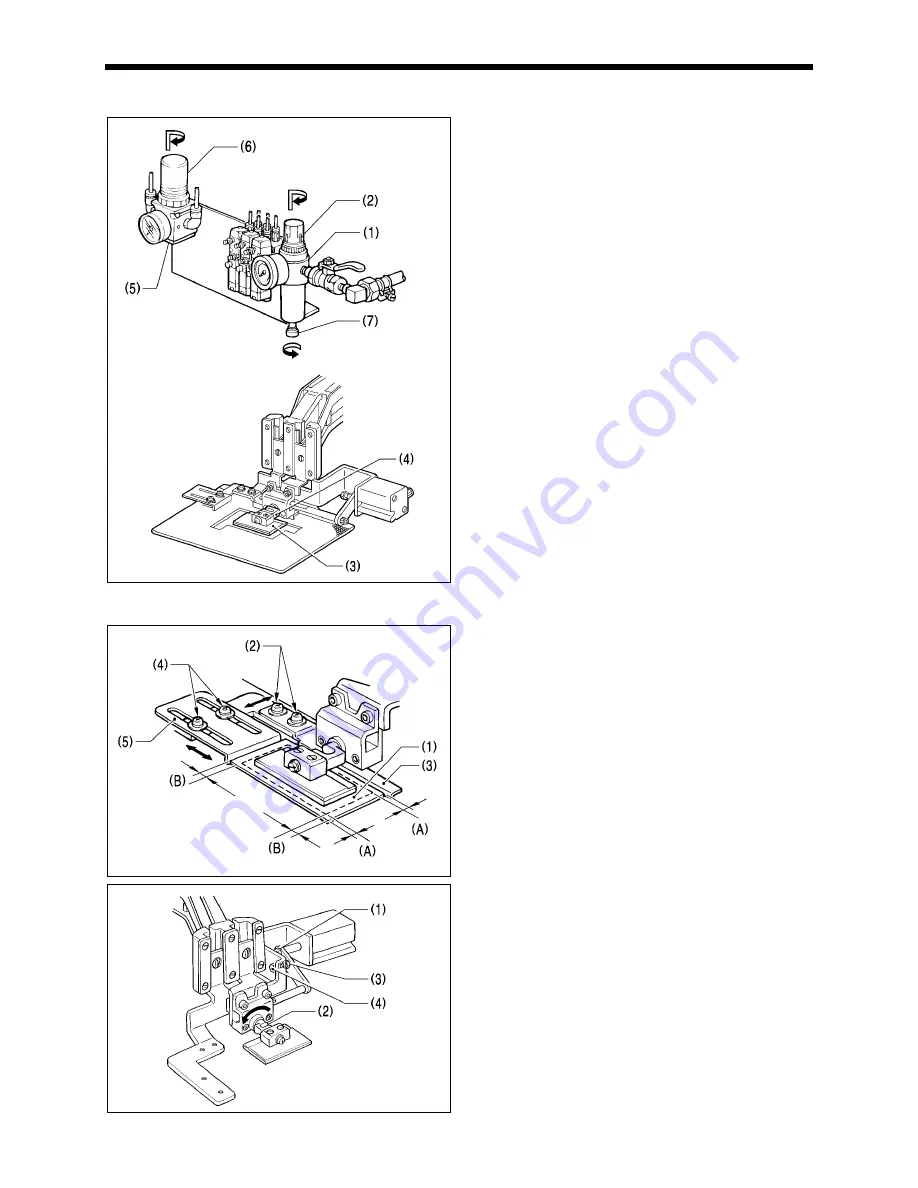
10. STANDARD ADJUSTMENTS
48
KE-434C,435C
10-16. Adjustment of air pressure (for pneumatic)
1. Air pressure should be 0.5 Mpa.
The air pressure can be adjusted by pulling up and turning the
control knob (2) on the integrator (1).
After adjustment is complete, push the control knob (2)
downward to lock it.
2. Adjust the air pressure for the reversal cylinder to stay within
such a range that the presser crank (4) rotates reversely when
pressing the sewing material with the pressure plate (3).
(Approx. 0.3 Mpa)
For adjustment, pull up and, turn the control knob (6) on the
air regulator (5).
After adjustment is complete, push the control knob (6)
downward to lock it.
3. If water stands in the bottle of the integrator (1), turn the drain
cock (7) in the direction indicated by an arrow to drain the
water.
10-17. Adjustment of inner clamping device
Adjustment of the positioning plates
Loosen the screws (2), and adjust the position of the positioning
plate R (3) so that the label (1) can be evenly laid out between
the front and back seams (A).
Next, loosen the screws (4), and adjust the position of the
positioning plate L (5) so that the presser plate can be evenly laid
out between the left and right seams (B).
Adjustment of the presser crank horizontal position
Loosen the nut (3) and push in or pull out the adjusting bolt (4) so
that the presser crank (2) can be horizontal when the reversal
cylinder piston rod (1) is moved to the left extreme.
2624Q
2623Q
2621Q
Increase pressure
Increase pressure
2622Q