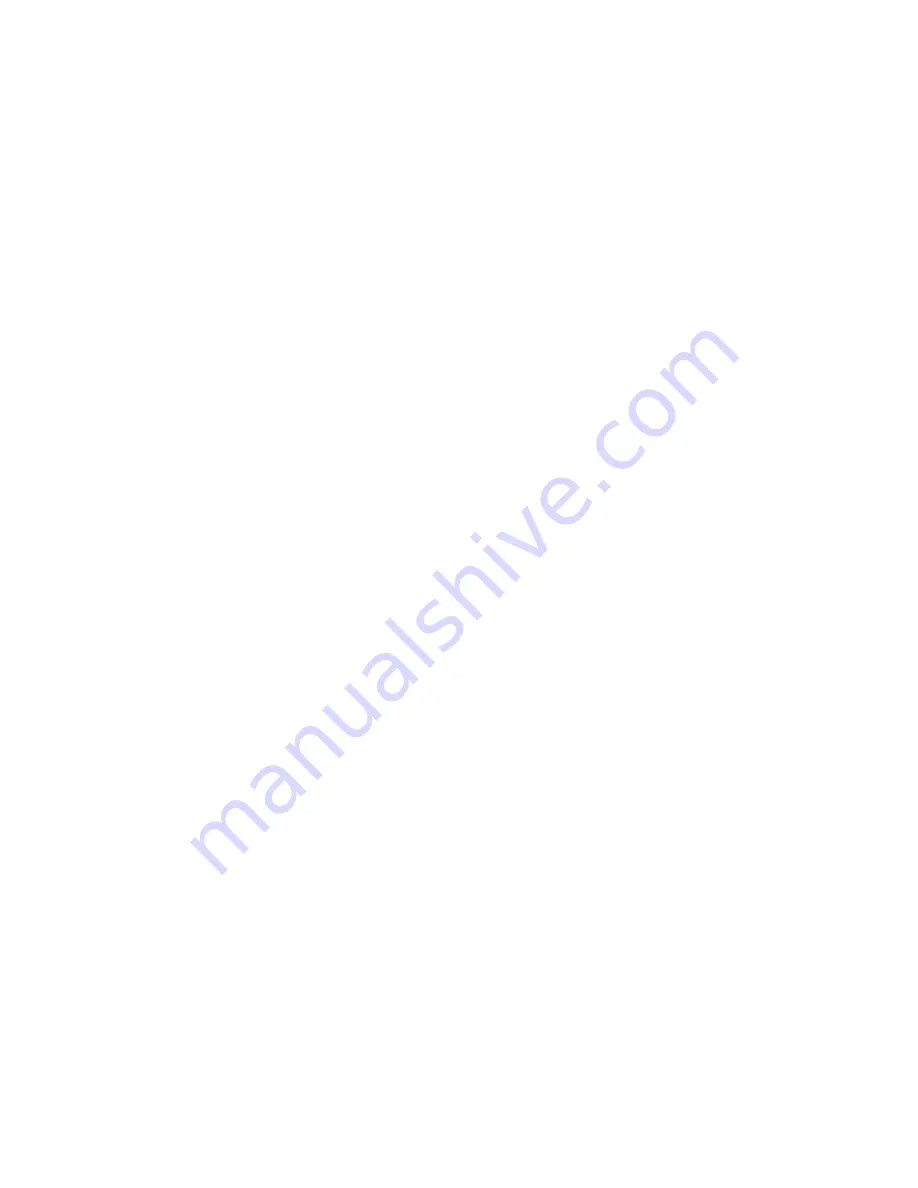
5
<PT-9500PC serviceman tool>
Carry out tests concerning Avery (I. Avery voltage for detecting setting, J. Avery printing test, and
Avery control values) is retained after the setup even though exiting from the software.
Europe version: Skip the tests.
U.S.A. version: Carry out the tests.
<Inspection Procedure>
(1) Cable connection
Connect the PT-9500PC and the inspection PC with serial port.
(2) DC power supply
Input the DC voltage (24V
±
0.1V) from the stabilized power supply through the AC jack of the
PT-9500PC and turn the power supply button ON.
(3) Read serial number
Read the serial number with the bar code reader.
* If a bar code reader is not available, manual entrance is acceptable.
(4) 2. Head rank check
Check the consistency between the head rank and the solder on the main PCB.
(5) 3. Head temperature check
Verify whether the temperature detection of the head thermistor runs normally.
1) If the detected temperature falls in the range of ambient temperature
±
10
°
C, the function of
thermal head is determined as normal function.
(6) 4. Switch sensor check
Press every switch and sensor to verify whether each performance is proper.
(7) 5. USB ID switch check
1) Switch the USB ID switch to verify whether each performance is proper.
2) After checking, set to “USB ID = 2”.
(8) 6. Drive standard voltage setting
Verify that “TEST OK” is displayed on the screen of the inspection PC.
(9) 8. Tape end sensor test
Mount the end tape cassette in the PT-9500PC and verify that “TAPE END TEST OK” is
displayed on the screen of the inspection PC.
(10) A. Full cut test
1) Mount the 24mm non-laminated tape cassette in the PT-9500PC and run the full cut
operation.
Note: Use the 24mm laminated tape cassette for the U.S.A. version.
2) Check whether the performance sample of full cut operation has proper cutting results.
(11) B. Half cut test
1) Mount the 6mm laminated tape cassette in the PT-9500PC and run the half cut operation.
2) Check whether the performance sample of half cut operation has proper cutting results.
Summary of Contents for PT-9500PC - P-Touch 9500pc B/W Thermal Transfer Printer
Page 1: ...SERVICE MANUAL MODEL PT 9500PC ...
Page 2: ...SERVICE MANUAL MODEL PT 9500PC ...
Page 86: ...IV 10 3 The LED does not turn on 4 No printing is performed ...
Page 87: ...IV 11 5 The interface malfunction 6 The tape is not cut ...
Page 88: ...IV 12 7 The tape is not fed correctly ...
Page 89: ...IV 13 ...
Page 90: ...IV 14 8 Half cut failure ...
Page 91: ...IV 15 9 Forced tape eject failure ...
Page 92: ...IV 16 10 The failure of pressure contact release of the roller holder ...
Page 103: ......
Page 104: ......
Page 105: ......