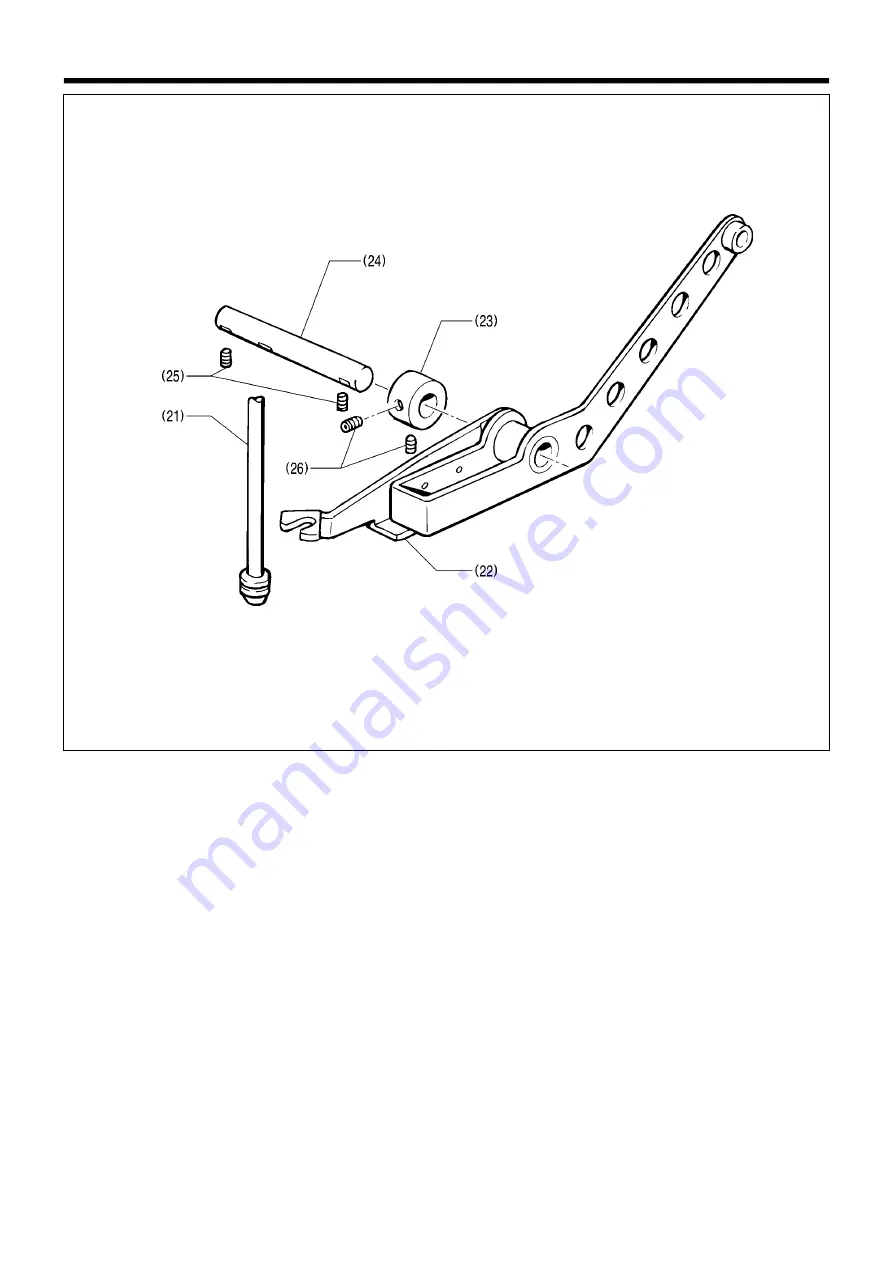
3. ASSEMBLY
RH-981A
39
9. Turn the pulley until it comes to its stop position, and attach the spreader link shaft (21) to the forked portion of the
spreader driving lever (22) while pulling the former downward.
10.Pass the looper link support shaft (24) through the spreader driving lever (22) and the set screw collar (23), and
secure them using the two set screws (25). (The split in the shaft should be facing the right.)
11. Tighten the two set screws (26) of the set screw collar (23) to eliminate the end play.
3758Q