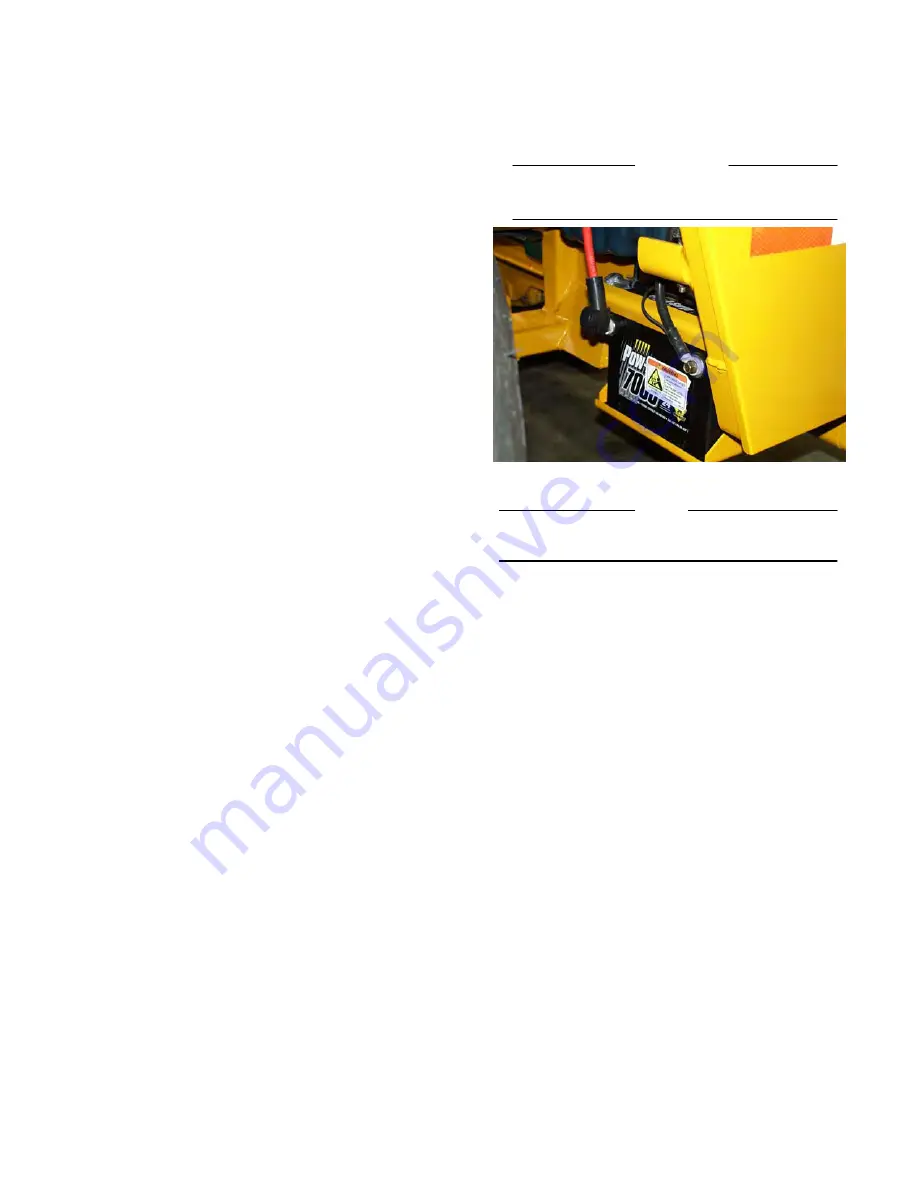
OPERATING INSTRUCTIONS
DAILY INSPECTION
Before Start-Up each day it important to do a careful
‘walk-around’ inspection.
Check the following items ;
•
Missing or damage parts. Loose hardware.
•
All Panels and Guards properly secured.
•
Forks, Lift Chains and Mast, no excessive
wear or damage.
•
Damage to, and leaks from, hydraulic tubes,
hoses, motors, pumps, and connections.
•
Excessive wear or damage to the tires.
•
Damage to the wheel rims and missing or
loose lug nuts.
•
All fluid levels. Top up as necessary.
•
That the operating controls are not damaged,
are correctly adjusted and working properly.
•
The operator’s seat and seat belt are properly
adjusted and secured.
•
Check around and under the machine for water
or oil leaks.
IMPORTANT
Do not operate the machine if any of the above
items fail to pass inspection.
Fig.10
BATTERY LOCATION
NOTE
See the Kubota Operating Manual for battery service
instructions.
19
Summary of Contents for 4500
Page 1: ...KESMAC Transportable Forklifts Operators Manual ...
Page 3: ......
Page 9: ......
Page 10: ......
Page 11: ......
Page 12: ...11 3 10 4 8 1 5 7 6 2 9 REAR WHEEL BATTERY ENGINE COMPARTMENT 9 ...
Page 38: ...35 Fig 22 ...
Page 40: ...Fig 25 37 ...