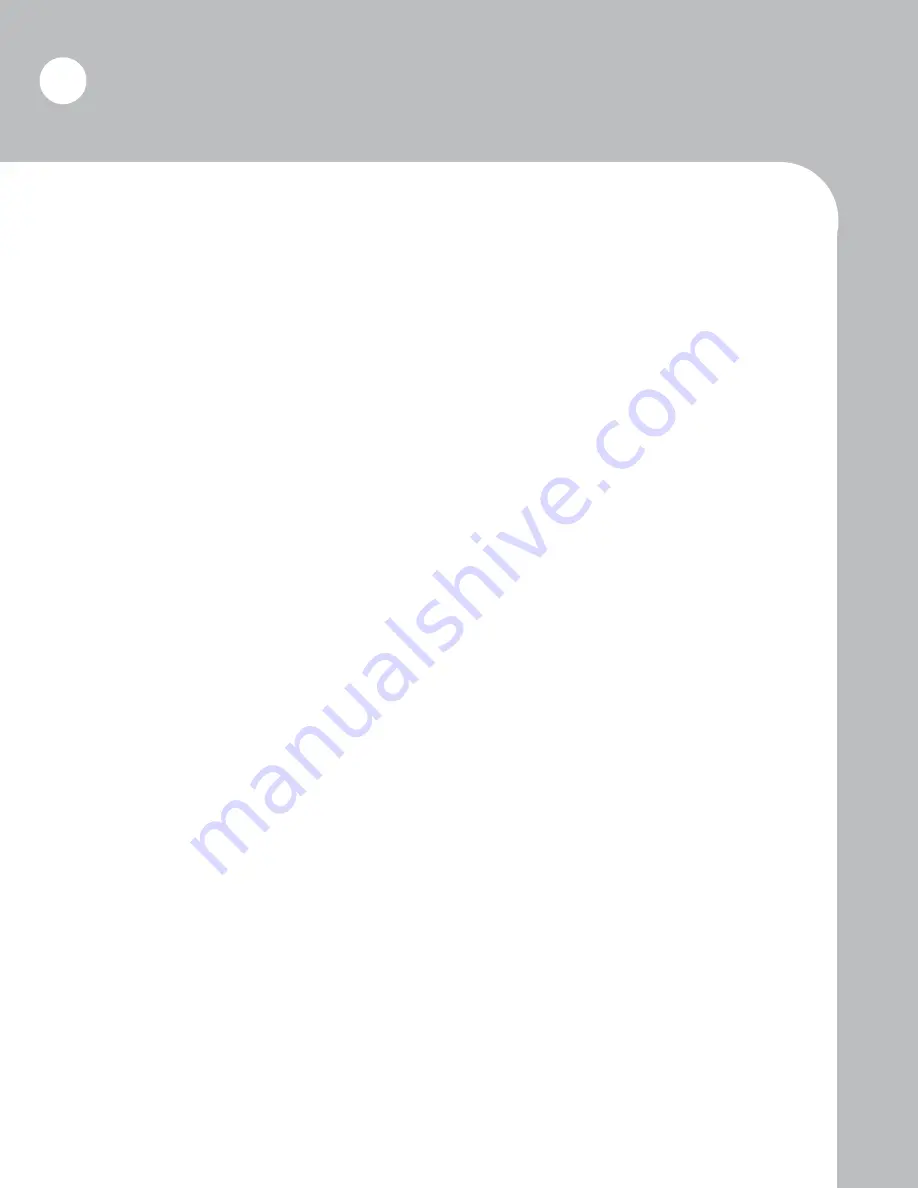
Warranty Statement
LIMITED WARRANTY
BROWN MANUFACTURING CORP. hereby warrants that Brown’s products will be free from defects in material
and workmanship under normal use according to the provisions and limitations herein set forth. All parts, specifically
EXCLUDING expendable ‘wear’ parts, that become unserviceable, due to defective material or workmanship, within three
months / 90 days from date of the original retail purchase, shall, at Brown’s option, be repaired or replaced.
LIMITATIONS
The obligations of Brown for breach of warranty shall be limited to products manufactured by Brown; (1) that are installed,
operated, and maintained according to Brown’s instruction furnished and/or available to the purchaser upon request; (2)
that are installed according to all other applicable Federal, State, and local codes or regulations; and (3) that the purchaser
substantiates were defective in material and workmanship notwithstanding that they were properly installed and correctly
maintained as set forth and were not abused or misused. The obligation of Brown shall be limited to replacing or repairing
the detective product, at the option of Brown. Brown shall not be responsible for any labor or cost of removal or repairing
or reinstallation of its products and shall not be liable for transportation costs to and from its plant in Ozark, Alabama.
Use of parts for modification or repair of the product or any component part thereof not authorized or manufactured by
Brown specifically for such product shall void this warranty. This warranty shall not apply to any damage to or defect in
the Brown’s products that is directly or indirectly caused by; (1) FORCE MAJEURE, act of GOD, or other accident not
related to an inherent product defect; or (2) abuse, misuse, or neglect of the such product, including any damage caused
by improper assembly, installation, adjustment, or faulty instruction of the purchaser.
OTHER THAN AS EXPRESSLY
SET FORTH HEREINABOVE, BROWN MAKES NO OTHER WARRANTY, EXPRESS OR IMPLIED, WITH
RESPECT TO ANY OF BROWN’S PRODUCTS, INCLUDED BUT NOT LIMITED TO ANY MERCHANTABILITY
OR FITNESS FOR A PARTICULAR PURPOSE. IN NO EVENT SHALL BROWN BE RESPONSIBLE FOR ANY
INCIDENTAL OR CONSEQUENTIAL DAMAGES OF ANY NATURE SUFFERED BY PURCHASER OR ANY
OTHER PERSON OR ENTITY CAUSED IN WHOLE OR IN PART BY ANY OF BROWN’S PRODUCTS
. Any
person or entity to whom this warranty extends and who claims breach of warranty against Brown must bring suit thereon
within one year from the date of occurrence of such breach of warranty or be forever barred from any and all legal or other
remedies for such breach of warranty. Brown is not responsible for and hereby disclaims any undertaking, representation,
or warranty made by any dealer, distributor, or other person that is inconsistent with or in any way more expensive than the
provisions of this limited warranty. This warranty grants specific legal rights and shall be read in conformity with applicable
state law. In some jurisdictions, the applicable law mandates warranty provisions that provide greater rights than those
provided for herein. In such case, this limited warranty shall be read to include such mandates provisions; and any provision
herein that is prohibited or unenforceable in any such jurisdiction shall, as to such jurisdiction, be ineffective to the extent
of such prohibition or unenforceable without invalidating the remaining provisions and without affecting the validity or
enforceability of such provisions in any other jurisdiction.
STATEMENT OF POLICY
In accordance with our established policy of constant improvement, we reserve the right to amend these specifications at
any time without notice.
WARRANTY BY MANUFACTURER
Dealer/distributor understands and agrees that the manufacturer extends only the following warranty to its customers. In the
event dealer/distributor extends any additional warranty such as enlarging the scope or period of warranty or undertaking a
warranty of fitness for any particular purpose or obligation not encompassed in manufacturer’s warranty, dealer/distributor
shall be solely responsible therefore and shall have no recourse against manufacturer with respect thereto.
4