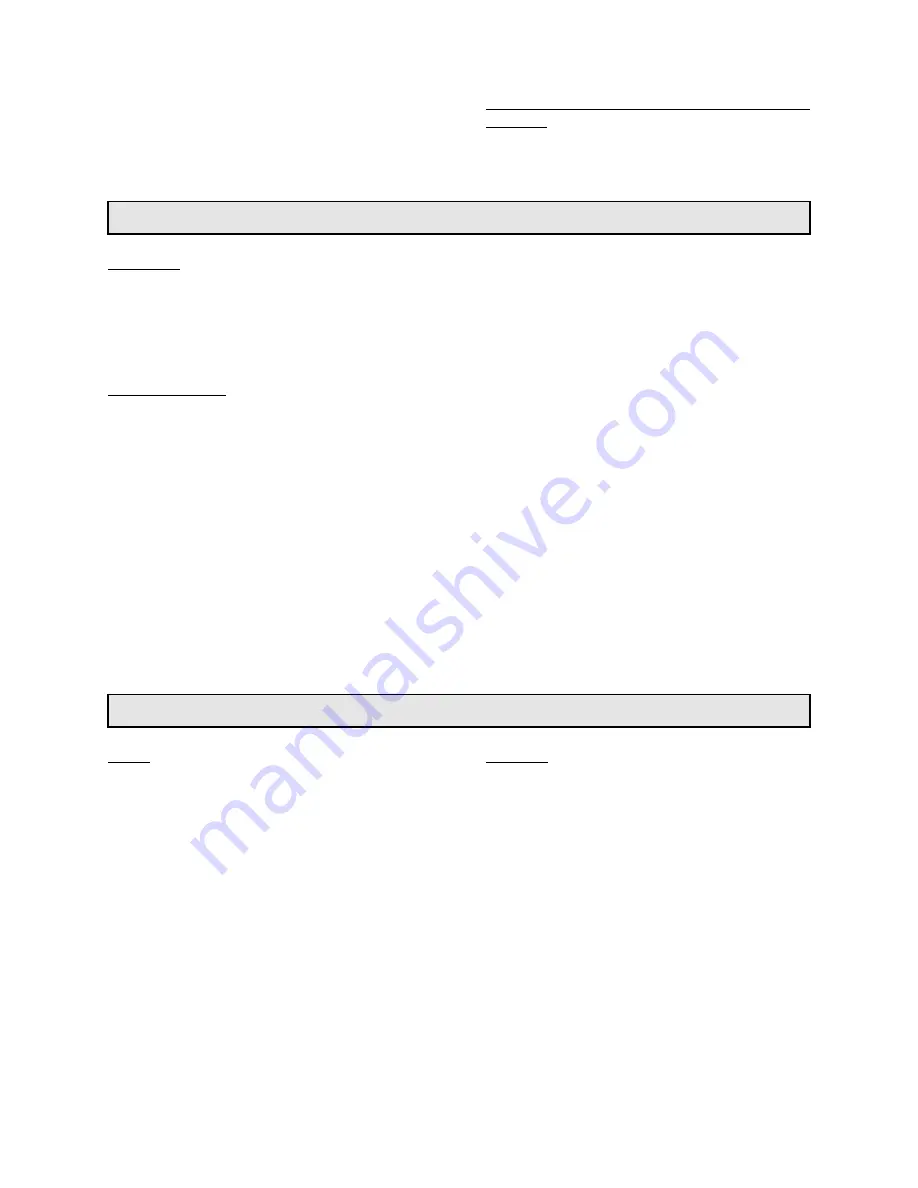
Dissolved oxygen will cause severe boiler tube
corrosion.
DRAINING AND REFILLING THE BOILER &
SYSTEM
If the system is drained and then refilled,
chemical treatment is essential to treat the raw
water. Use only clean, softened water.
3.4 EXTERNAL "FIRE-SIDE" CLEANING
PURPOSE
Carbon (soot) is an insulator and is corrosive.
The heating surface of a boiler must be kept free
from soot accumulation to keep the boiler
operating at its highest efficiency and to avoid
damage from corrosion.
SOOT REMOVAL
If the yearly inspection of the boiler tube surfaces
reveals a build-up of either soot or rust (usually
due to condensation), the tubes should be
thoroughly brushed. (Tube cleaning brushes are
available from Bryan Steam) To inspect and, if
necessary, clean the tube surfaces and flue
collector, first remove the tube access panels.
Examine the exterior of the tubes for evidence of
soot or rust. Using a flashlight, carefully look
between the tubes. There should be an
unobstructed opening between all tubes, and the
top surfaces of the tube must be free from soot
accumulation. Also inspect the interior of the flue
collector. Brush or vacuum the soot from all
surfaces. Be sure to cover atmospheric burners
with
a protective cover during cleaning to prevent soot
from falling into them.
If the buildup of soot is appreciable, the flue gas
venting system must be thoroughly inspected
internally as well, and cleaned as necessary.
IMPORTANT
If either soot or condensation is apparent, a boiler
service technician should be consulted. The
presence of soot indicates poor combustion and
possibly hazardous boiler operation. Failure to do
so may result in fire, explosion potential, or
asphyxiation. A combustion test and burner
adjustments should be undertaken at once.
Rust on the tubes indicates that boiler operating
temperatures are too low. The set point of the
boiler operating control must be no less than
130 F for natural gas or propane firing and
170 F for oil fired boilers. Boilers equipped with
outdoor reset must also follow these limits.
3.5 SUGGESTED MAINTENANCE SCHEDULE
DAILY
1. Make visual inspection of gauges, monitors,
and indicators and record readings in boiler log.
2. Make visual check of instrument and
equipment settings against factory recommended
specifications.
3. Check operation of float type low water cutoffs
to ensure control is functioning. The lower piping
connections of float type level controls should
have a suitable blowdown valve piped into a
proper drain. This valve should be opened
periodically to allow any sludge accumulated in
the control to be flushed out. On closed loop
water heating systems this should not be often
required. Consult manufacturer's instructions.
WEEKLY
1. On units equipped with firing rate control, verify
it is functioning correctly by adjusting control and
observing if input changes accordingly.
2. Make visual inspection of igniter and pilot
flame. For an atmospheric unit, confirm pilot
flame is as shown in this manual (Section 1.9)
and that the main burners light off correctly
(smoothly) and that the flame is clean and
normal. For units with a power burner, check pilot
flame signal strength as specified in burner
manual.
3. Check pilot and main fuel valves for correct
operation. Open limit switch - make audible and
visual check - check valve position indicators and
check fuel meters, if supplied.
Summary of Contents for AB Series
Page 22: ......