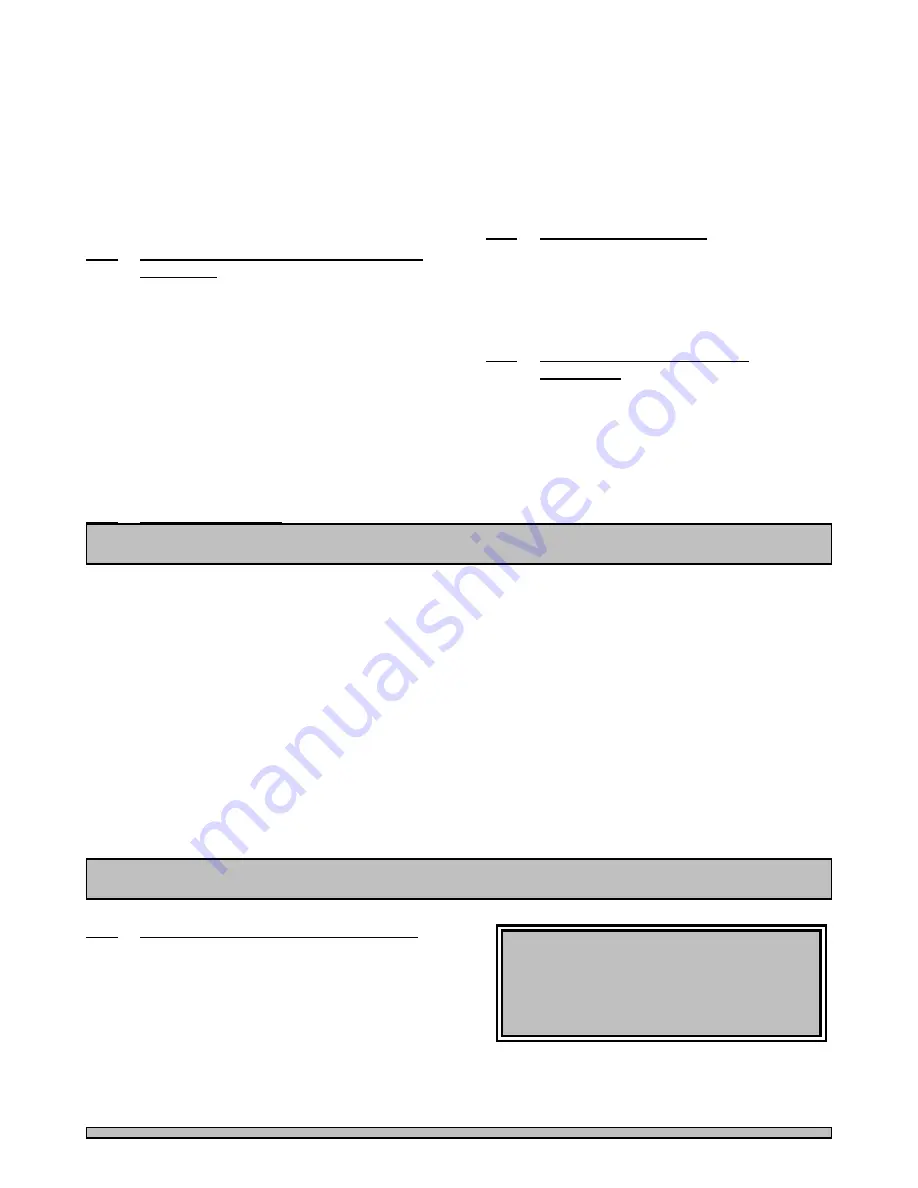
When the water level is restored, the boiler
should cycle back on. Depress the manual reset
button of devices which require manual reset in
order to restore the boiler to operation.
Carefully read the enclosed literature on the
low water cut-off controls, particularly
installing, operating and servicing.
2.1-6
COMBINATION LOW WATER CUT-OFF
& FEEDER
The low water cut-off/feeder supplied with
some boilers serves as a low water cut-off (see
above) and also causes make-up water to be
added to the boiler, should the water level drop
below its control point. This type of control
must be operationally tested to assure that the
make-up water is introduced as needed.
Carefully read the enclosed literature on the
low water cut-off controls, particularly
installing, operating and servicing.
2.1-7 OTHER
CONTROLS
Additional controls, as required for the
particular installation, may also be provided.
Refer to the literature on these devices included
in the boiler manual. All such devices must be
operationally tested to assure reliable operation
of the boiler and system.
2.1-8
BOILER FEED SYSTEM
The boiler feed pump must be operationally
tested to assure that it can provide boiler
feedwater at the pressure and in the amount
needed for safe and reliable boiler operation.
2.1-9
CHEMICAL FEED SYSTEM &
SOFTENER
Check the performance of the boiler water
softener and chemical treatment system.
Chemically test the feedwater to be certain it
complies with the recommendations of the
chemical treatment consultant.
2.2 OPERATING
CONTROLLER
As previously discussed, electric boilers are
broken down into branch circuits. Each circuit
is controlled by a step control (if two steps or
less, then controlled by their own pressure
control). Step control operates by having a
signal sent from the operating control that
typically sends a modulation signal depending
on the pressure setting at the pressure operating
control. The pressure operating controller will
send a signal to the step control to cycle on
more steps until the desired pressure is reached.
Once the pressure control is satisfied, steps will
begin to cycle off, therefore, turning off
elements and reducing the heat output. Each
step control is supplied with a dead band area.
When the desired pressure is reached the step
control will stay constant until a larger degree
of drop is recognized. This will keep the step
controller from oscillating between steps
during operation. The operating control
pressure needs to be set and maintained by the
operator for the desired output
.
2.3 OPERATING
INSTRUCTIONS
2.3-1
FAMILIARIZATION WITH MANUAL(S)
The user of the boiler must familiarize himself
with this manual to be sure he is prepared to
operate and maintain the boiler properly.
The operating instructions should be kept in a
safe place and available to all who may be
working or operating the boiler.
READ THE MANUAL BEFORE
ATTEMPTING A START-UP.
C
AUTION
:
CHECK ALL ELECTRICAL
TERMINALS AND CONNECTIONS FOR
TIGHTNESS BEFORE START
-
UP
.