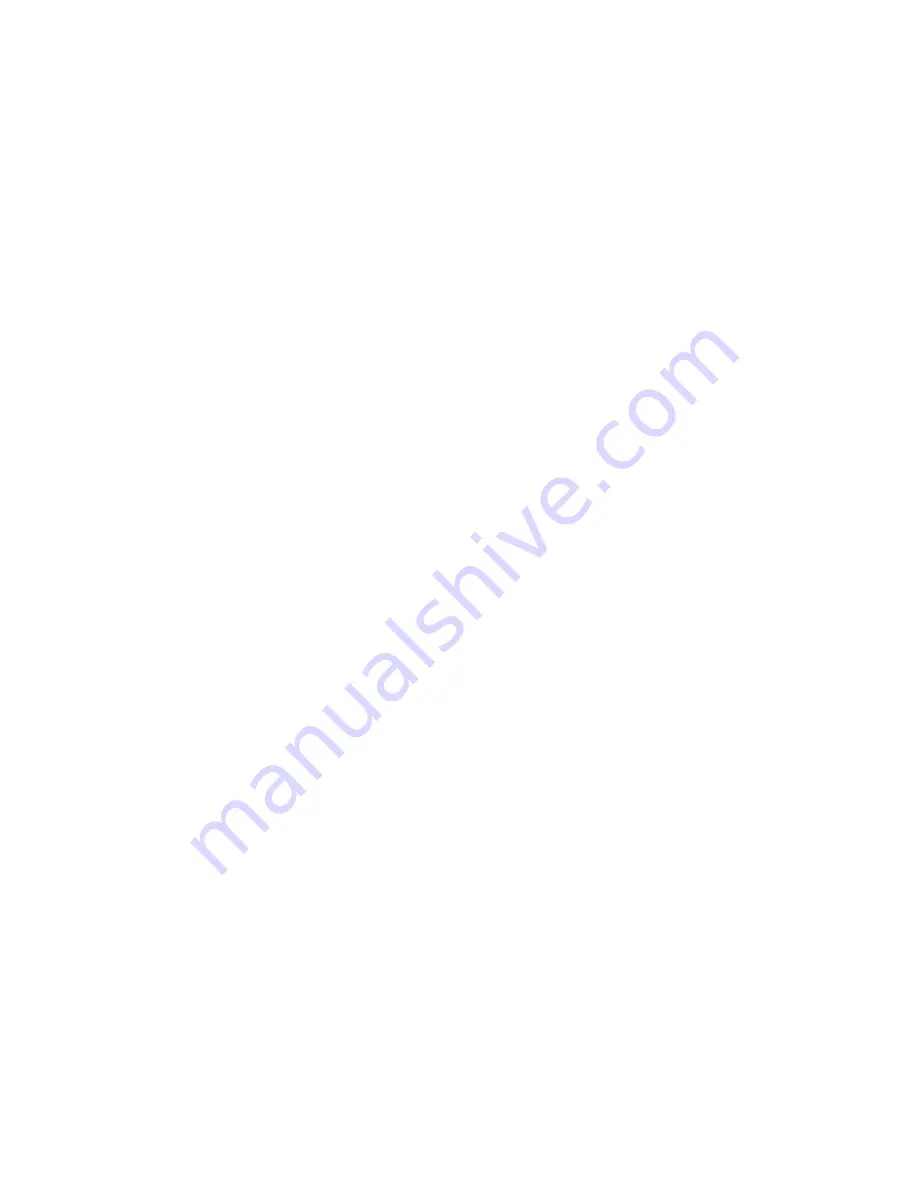
90-second period, after which the LED will be ON continuous, as
long as no faults are detected. After the 90-second period, the
furnace will respond to the thermostat normally.
The blower door must be installed for power to be conducted
through the blower door interlock switch ILK to the furnace
control CPU, transformer TRAN, inducer motor IDM, blower
motor BLWM, hot-surface igniter HSI, and gas valve GV.
1. Heating
(See Fig. 25 for thermostat connections.)
The wall thermostat
″
calls for heat,
″
closing the R-to-W
circuit. The furnace control performs a self-check, verifies the
pressure switch contacts PRS are open, and starts the inducer
motor IDM.
a. Inducer Prepurge Period- As the inducer motor IDM
comes up to speed, the pressure switch contacts PRS close
to begin a 15-second prepurge period.
b. Igniter Warm-Up- At the end of the prepurge period, the
Hot-Surface igniter HSI is energized for a 17-second
igniter warm-up period.
c. Trial-for-Ignition Sequence- When the igniter warm-up
period is completed, the main gas valve relay contacts GVR
close to energize the gas valve GV, the gas valve opens,
and 24 vac power is supplied for a field-installed humidi-
fier at the HUM terminal. The gas valve GV permits gas
flow to the burners where it is ignited by the HSI. Five
seconds after the GVR closes, a 2-second flame proving
period begins. The HSI igniter will remain energized until
the flame is sensed or until the 2-second flame proving
period begins.
d. Flame-Proving- When the burner flame is proved at the
flame-proving sensor electrode FSE, the furnace control
CPU begins the blower-ON delay period and continues to
hold the gas valve GV open. If the burner flame is not
proved within two seconds, the control CPU will close the
gas valve GV, and the control CPU will repeat the ignition
sequence for up to three more Trials-For-Ignition before
going to Ignition-Lockout. Lockout will be reset auto-
matically after three hours or by momentarily interrupting
115 vac power to the furnace, or by interrupting 24 vac
power at SEC1 or SEC2 to the furnace control CPU (not at
W, G, R, etc.).
If flame is proved when flame should not be present, the
furnace control CPU will lock out of Gas-Heating mode
and operate the inducer motor IDM until flame is no longer
proved.
e. Blower-On Delay- If the burner flame is proven, the
blower motor is energized on HEAT speed 25 seconds after
the gas valve GV is energized.
Simultaneously, the electronic air cleaner terminal EAC-1
is energized and remains energized as long as the blower
motor BLWM is energized.
f. Blower-Off Delay- When the thermostat is satisfied, the
R-to-W circuit is opened, de-energizing the gas valve GV,
stopping gas flow to the burners, and de-energizing the
humidifier terminal HUM. The inducer motor IDM will
remain energized for a 5-second post-purge period. The
blower motor BLWM and air cleaner terminal EAC-1 will
remain energized for 90, 120, 150, or 180 seconds (depend-
ing on the blower-OFF delay selection). The furnace
control CPU is factory-set for a 120-second blower-OFF
delay.
2. Cooling Mode
The thermostat “calls for cooling.”
a. Single-Speed Cooling
(See Fig. 25, 26, 28, and 30 for thermostat connections)
The thermostat closes the R-to-G-and-Y circuits. The R-to-
Y circuit starts the outdoor unit, and the R-to-G-and-Y/Y2
circuits start the furnace blower motor BLWM on COOL
speed.
The electronic air cleaner terminal EAC-1 is energized with
115 vac when the blower motor BLWM is operating.
When the thermostat is satisfied, the R-to-G-and-Y circuits
are opened. The outdoor unit will stop, and the furnace
blower motor BLWM will continue operating on the
COOL speed for an additional 90 seconds. Jumper Y/Y2 to
DHUM to reduce the cooling off-delay to 5 seconds. (See
Fig. 24.)
b. Two-Speed Cooling
(See Fig. 27, 29, 31, and 32 for thermostat connections.)
The thermostat closes the R-to-G-and-Y1 circuits for
low-cooling or closes the R-to-G-and-Y1-and-Y2 circuits
for high-cooling. The R-to-Y1 circuit starts the outdoor
unit on low-cooling speed, and the R-to-G-and-Y1 circuit
starts the furnace blower motor BLWM on low-cool speed
(same speed as FAN). The R-to-Y1-and-Y2 circuits start
the outdoor unit on high-cooling speed, and the R-to-G-
and-Y/Y2 circuits start the furnace blower motor BLWM
on COOL speed.
The electronic air cleaner terminal EAC-1 is energized
with 115 vac whenever the blower motor BLWM is
operating.
When the thermostat is satisfied, the R-to-G-and-Y1 or
R-to-G-and-Y1 and Y2 circuits are opened. The outdoor
unit stops, and the furnace blower BLWM and electronic
air cleaner terminal EAC-1 will remain energized for an
additional 90 seconds. Jumper Y1 to DHUM to reduce the
cooling off-delay to 5 seconds. (See Fig. 24.)
3. Thermidistat Mode
(See Fig. 26-29 for Thermidistat connections.)
The dehumidification output, DHUM on the Thermidistat
should be connected to the furnace control thermostat terminal
DHUM. When there is a dehumidify demand, the DHUM
input is activated, which means 24 vac signal is removed from
the DHUM input terminal. In other words, the DHUM input
logic is reversed. The DHUM input is turned ON when no
dehumidify demand exists. Once 24 vac is detected by the
furnace control on the DHUM input, the furnace control
operates in Thermidistat mode. If the DHUM input is low for
more than 48 hours, the furnace control reverts back to
non-Thermidistat mode.
The cooling operation described in item 2. above also applies
to operation with a Thermidistat. The exceptions are listed
below:
a. When the R-to-G-and-Y1 circuit is closed and there is a
demand for dehumidification, the furnace blower motor
BLWM will continue running at low-cool speed (same
speed as FAN).
b. When the R-to-G-and-Y/Y2 circuit is closed and there is a
demand for dehumidification, the furnace blower motor
BLWM will drop the blower speed from COOL to HEAT
for a maximum of 10 minutes before reverting back to
COOL speed. If there is still a demand for dehumidification
48
→