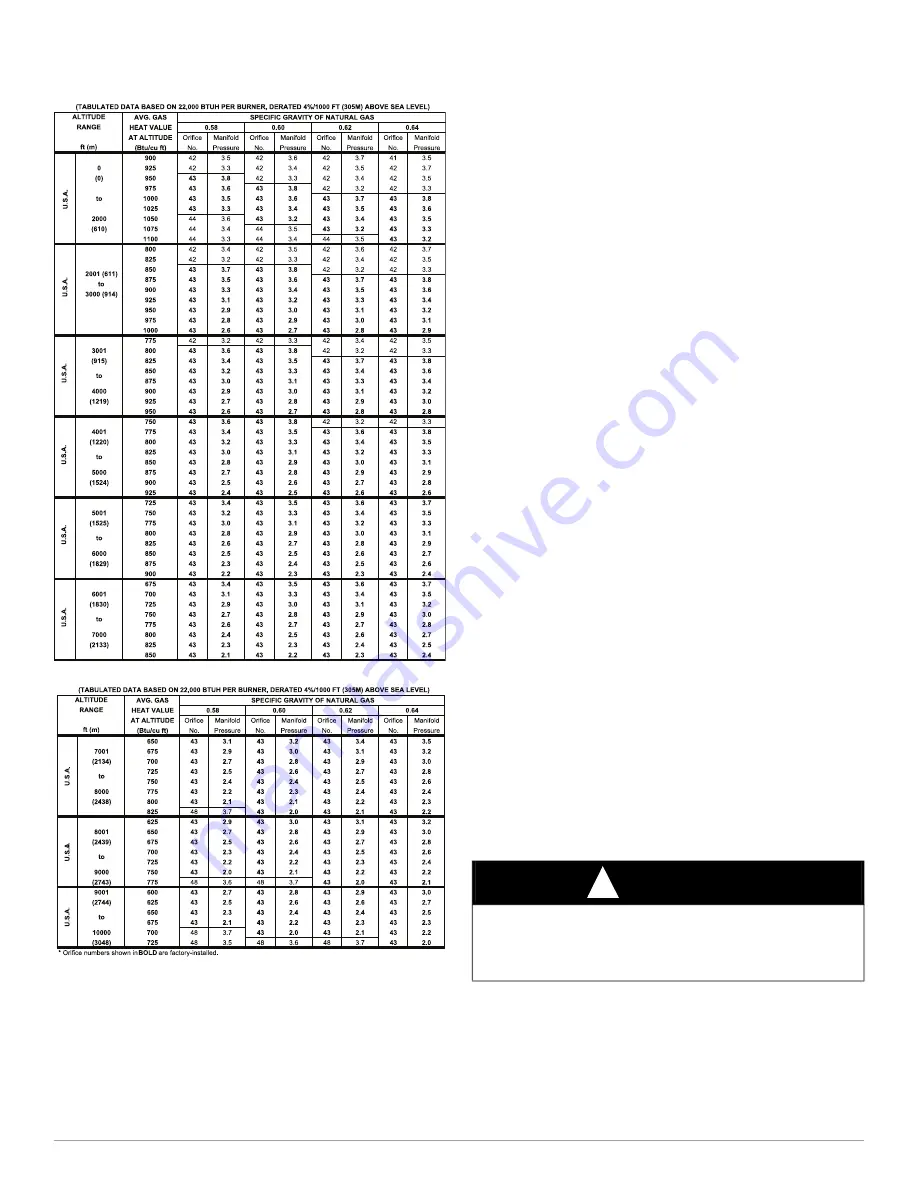
800SA/801SA: Installation, Start–Up, Operating and Service and Maintenance Instructions
Manufacturer reserves the right to change, at any time, specifications and designs without notice and without obligations.
28
Table 11 – Orifice Size* and Manifold Pressure (In. W.C.) for Gas
Input Rate
A10180
A10180a
4. Verify natural gas input rate by clocking meter.
NOTE:
Gas valve regulator adjustment cap must be in place for proper
input to be clocked.
a. Turn off all other gas appliances and pilots served by the meter.
b. Run furnace for 3 minutes in heating operation.
c. Measure time (in sec) for gas meter to complete 1 revolution and
note reading. The 2 or 5 cubic feet dial provides a more accurate
measurement of gas flow.
d. Refer to
for cubic ft. of gas per hr.
e. Multiply gas rate (cu ft./hr) by heating value (Btuh/cu ft.) to
obtain input.
f. If clocked rate does not match required input from Step 1,
increase manifold pressure to increase input or decrease manifold
pressure to decrease input. Repeat steps b through e until correct
input is achieved. Reinstall regulator seal cap on gas valve.
5. Set temperature rise. The furnace must operate within the
temperature rise ranges specified on the furnace rating plate. Do not
exceed temperature rise range specified on unit rating plate.
Determine the temperature rise as follows:
NOTE:
Blower access door must be installed when taking temperature
rise reading. Leaving blower access door off will result in incorrect
temperature measurements.
a. Place thermometers in return and supply ducts as close to furnace
as possible. Be sure thermometers do not see radiant heat from
heat exchangers. Radiant heat affects temperature rise readings.
This practice is particularly important with straight-run ducts.
b. When thermometer readings stabilize, subtract return-air
temperature from supply-air temperature to determine air
temperature rise.
NOTE:
If the temperature rise is outside this range, first check:
(1.) Gas input for heating operation.
(2.) Derate for altitude if applicable.
(3.) Return and supply ducts for excessive restrictions causing static
pressures greater than 0.50-In. W.C.
c. Adjust air temperature rise by adjusting blower speed. Increase
blower speed to reduce temperature rise. Decrease blower speed
to increase temperature rise
d. Turn thermostat down below room temperature and remove
blower access door.
e. To change motor speed selection for heating, remove blower
motor lead from control HEAT terminal (See
). Select
desired blower motor speed lead from one of the other terminals
and relocate it to the HEAT terminal (See
for lead color
identification). Reconnect original lead to SPARE terminal.
f. If the same motor speed tap is needed for heating and cooling, a
Jumper Wire accessory kit is available, see Product Data sheet
for the current Jumper Wire accessory part number. The single
wire end of the jumper will be connected to the desired blower
motor speed lead. The two wire end of the jumper will be
connected to the control board, connecting one wire to the HEAT
(heating blower tap) terminal and the other will be connected to
the COOL (cooling blower tap). Use the provided wire ties to
secure the loose blower motor speed lead and any other loose
wires, being careful not to put tension on any wire connectors.
g. Repeat steps a through e.
h. When correct input rate and temperature rise is achieved, turn
gas valve ON/OFF switch to OFF.
i. Remove manometer or similar device from gas valve.
j. Reinstall manifold pressure tap plug in gas valve.
(1.)
WARNING
!
FIRE HAZARD
Failure to follow this warning could result in personal injury, death,
and/or property damage.
Reinstall manifold pressure tap plug in gas valve to prevent gas leak.