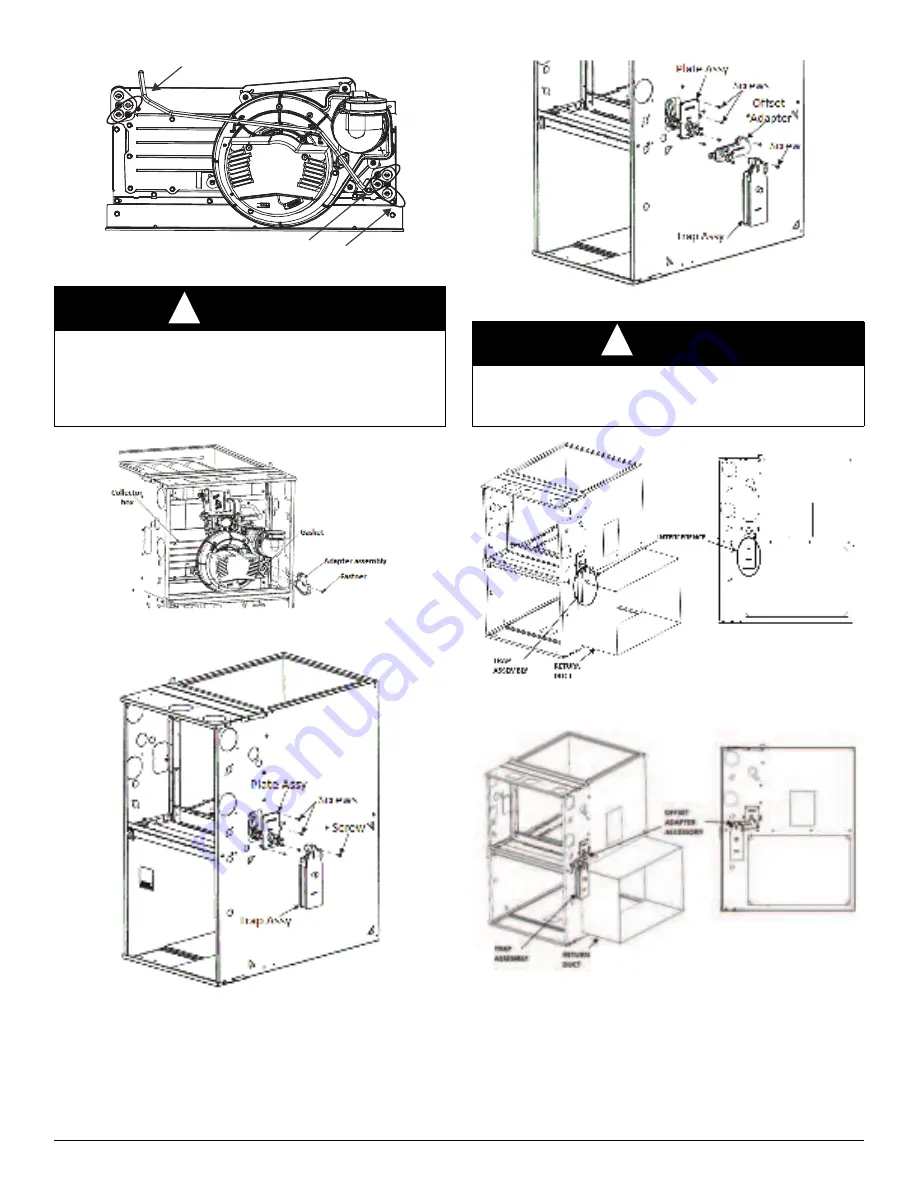
935CA: Installation, Start-up, Operating and Service and Maintenance Instructions
Manufacturer reserves the right to change, at any time, specifications and designs without notice and without obligations.
13
A200075
Fig. 13 – Drain Plugs
A200076
Fig. 14 – Upflow Example of Trap Adapter Installation
A200064
Fig. 15 – Upflow Condensate Drain
A200065
Fig. 16 – Upflow - Offset of Condensate Drain
A200119
Fig. 17 – Upflow Right Side Return Configuration - Trap
Interference
A200120
Fig. 18 – Upflow Right Side Return Configuration - Required
Upflow Offset Installation
WARNING
!
CARBON MONOXIDE POISONING HAZARD
Failure to follow this warning could result in property damage, personal
injury or death.
Missing or damaged gaskets on trap components may result in flue gas
leakage and water leakage.
Remove these for Horizontal Left
Remove these for Horizontal Right
Remove these for Upflow
NOTICE
!
Upflow installations utilizing the right side air return opening
should follow the Upflow Specific Steps - Offset Installation
to ensure the full opening is available for return ductwork.