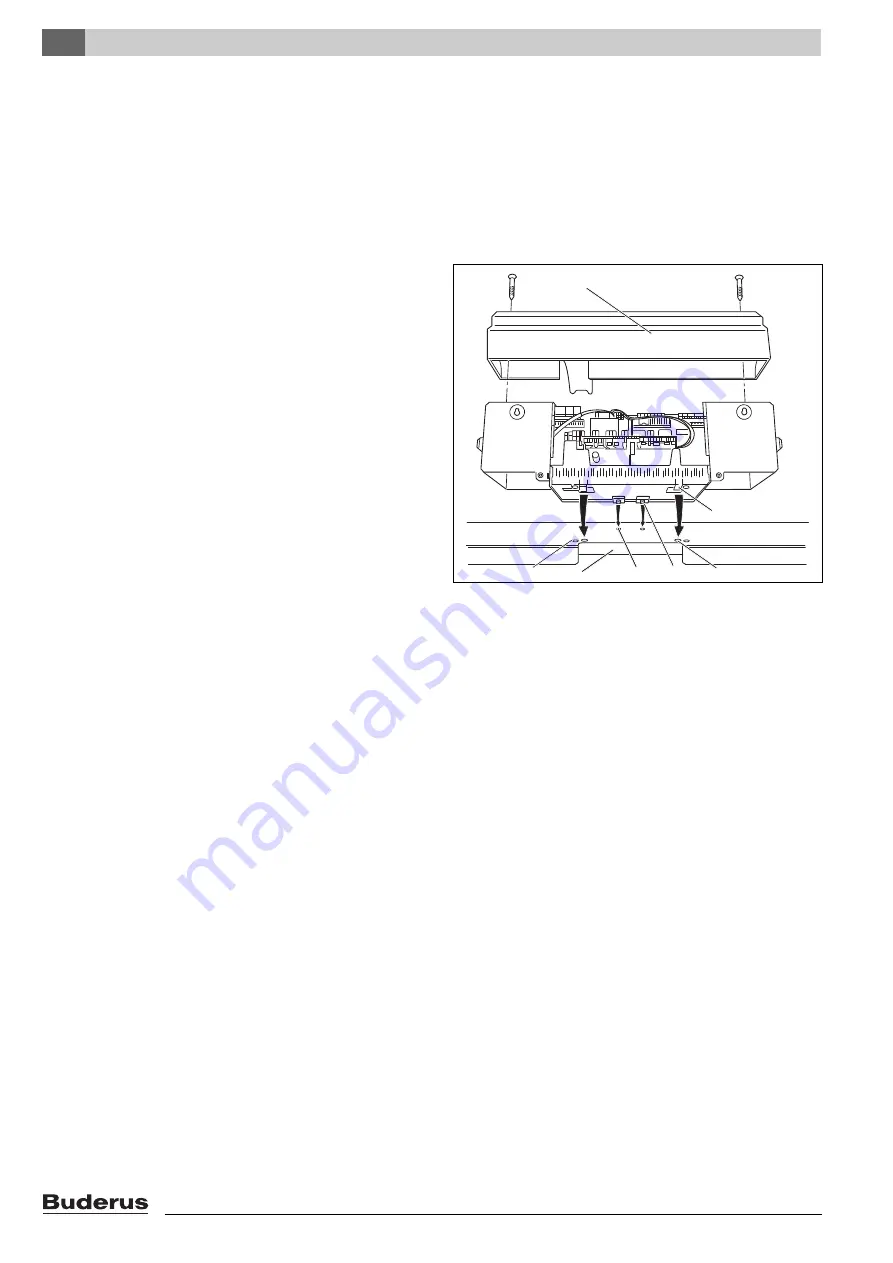
Installing the control device
10
Logano GE515 - We reserve the right to make any changes due to technical modifications.
46
10 Installing the control device
This chapter explains how to install a series 4000 control
device, plus a temperature sensor set.
10.1 Installing the control device
Figure 60 shows the control unit and the front cover "A"
as viewed from the rear.
z
Loosen both screws (Fig. 60,
[1]
) securing the
terminal cover. Remove the terminal cover by pulling
it upwards.
z
Mount the control unit. Insert the control unit at the
front of the boiler with the locating tabs (Fig. 60,
[4]
)
into the oval apertures of the front boiler hood
(Fig. 60,
[5]
). Pull the control unit forward and then
pivot it back. Ensure that the resilient hooks (Fig. 60,
[2]
) engage at the rear into the rectangular apertures
of the front boiler hood (Fig. 60,
[3]
).
z
Secure the control unit base on the r.h. and l.h. side
of the cable way (Fig. 60,
[6]
) in the front boiler hood
with two self-tapping screws (Fig. 60,
[7]
).
Fig. 60 Installing the control device
1
2
4
5
6
3
7