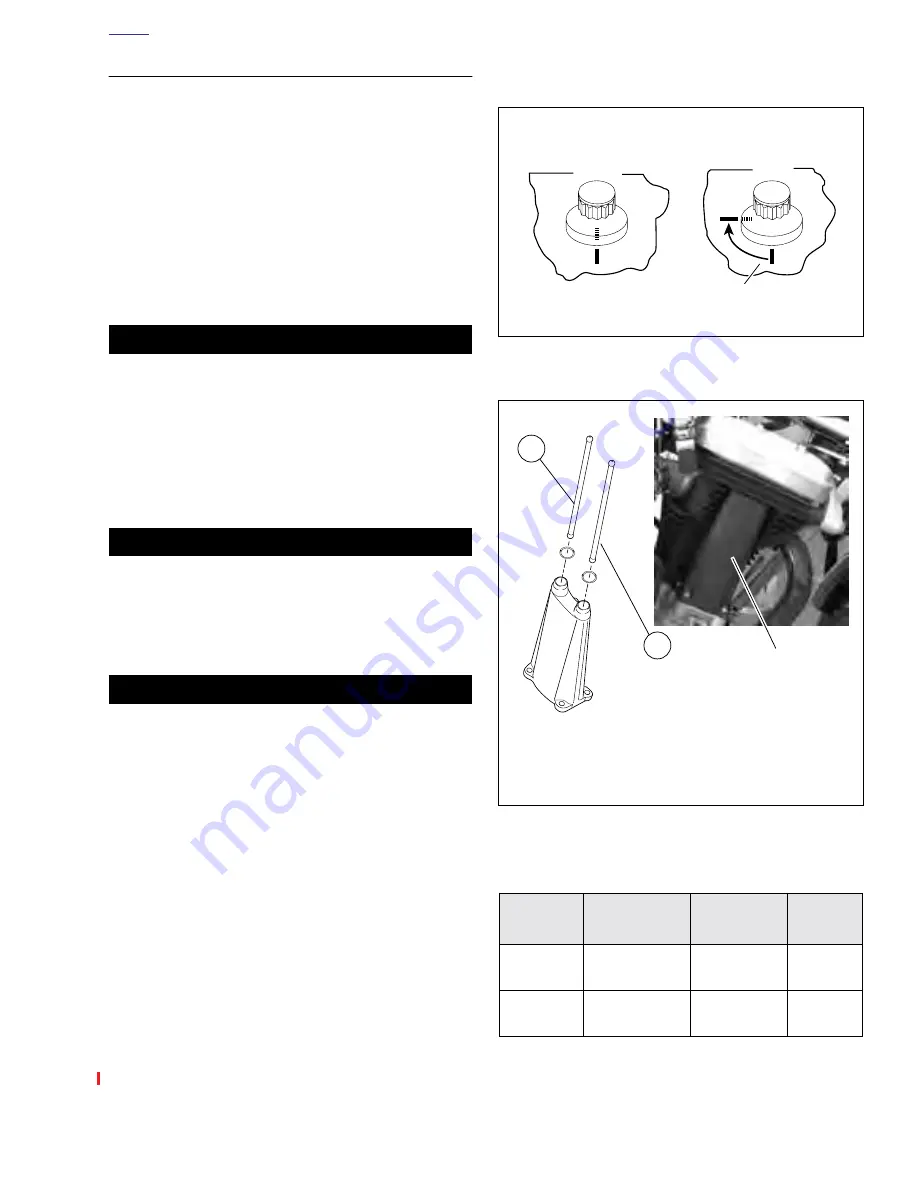
2002 Buell P3: Engine
3-33
HOME
INSTALLATION
If only cylinder head work was needed, reinstall cylinder head
following these instructions. If further repair is required, see
3.6 CYLINDER AND PISTON
.
1.
Coat mating surfaces of cylinder studs and head screws
with parts cleaning solution.
2.
Scrape old oil and any carbon deposits from threads by
using a back-and-forth motion, threading each head
screw onto its mating cylinder stud.
3.
Remove head screws from studs. Wipe or blow dry
thread surfaces.
4.
Apply oil to stud threads and to the underside of the
head screw shoulder.
CAUTION
Only oil film must remain on the head screw surfaces.
Too much oil will pool in the head screw sleeve. Pooled
oil may prevent proper torque application and full thread
engagement.
5.
Blow or wipe off excess oil from head screws.
6.
Thoroughly clean and dry the gasket surfaces of cylinder
and cylinder head.
7.
Install a
new
O-ring on each dowel.
CAUTION
O-rings help to properly position the head gasket. O-
rings must be installed before the head gasket.
8.
Install a
new
head gasket to cylinder.
9.
Carefully lower cylinder head over studs and position on
dowels. Use great care so as not to disturb head gasket.
CAUTION
The procedure for tightening the head screws is critical
to proper distribution of pressure over gasket area. It
prevents gasket leaks, stud failure, and head and cylin-
der distortion.
10. See
Figure 3-45.
For each cylinder head, start with
screw numbered one, as shown. In increasing numerical
sequence (i.e. – 1, 2, 3 and 4):
a.
Tighten bolts to 8-10 ft-lbs (11-14 Nm).
b.
Tighten bolts to 13-15 ft-lbs (18-20 Nm).
c.
Loosen all screws.
11. After screws are loosened from initial torque, tighten
head screws in three stages. Tighten fasteners in
increasing numerical sequence (i.e. – 1, 2, 3 and 4).
a.
Tighten each screw to 8-10 ft-lbs (11-14 Nm).
b.
Tighten each screw to 13-15 ft-lbs (18-20 Nm).
c. See
Figure 3-63.
Mark cylinder head and head
screw shoulder with a line as shown (View A).
d.
Turn all bolts an additional 85 -95 .
12. See
3.15 HYDRAULIC LIFTERS
. Install hydraulic lifters
and push rod cover.
13. See
Figure 3-64.
See
Table 3-7.
Identify push rod color
coding, length and respective push rod positions in
engine. Place intake and exhaust push rods onto seat at
top of tappet.
°
°
Figure 3-63. Tightening Head Screws
Figure 3-64. Push Rod Locations
Table 3-7. Push Rod Selection
Position
Color Code
Length
Part Num-
ber
Exhaust
1 Band-Black
10.800 in.
(274.320 mm)
17895-00Y
Intake
1 Band-Orange
10.746 in.
(272.948 mm)
17984-00Y
View
A
View
B
a0089x3x
Tighten head screws 1/4-turn in
the third stage of installation
1.
Intake Push Rod
2.
Exhaust Push Rod
a0098x3x
7695
2
1
Push Rod Cover
Location
Summary of Contents for 2002 P3
Page 2: ......
Page 17: ...A 15 Appendix A Tools HOME ...
Page 32: ...C 3 Appendix C Metric Conversions HOME ...
Page 41: ...1 8 2002 Buell P3 Maintenance HOME NOTES ...
Page 75: ......
Page 111: ...2 36 2002 Buell P3 Chassis HOME NOTES ...
Page 143: ...2 68 2002 Buell P3 Chassis HOME NOTES ...
Page 144: ...2002 Buell P3 Chassis 2 69 HOME ...
Page 146: ......
Page 147: ......
Page 223: ...3 76 2002 Buell P3 Engine HOME NOTES ...
Page 225: ......
Page 256: ...2002 Buell P3 Fuel System 4 31 HOME ...
Page 258: ......
Page 259: ......
Page 279: ...5 20 2002 Buell P3 Electric Starter HOME NOTES ...
Page 281: ......
Page 327: ......
Page 398: ...2002 Buell P3 Electrical 7 71 HOME ...
Page 400: ...Product 1 2 ...