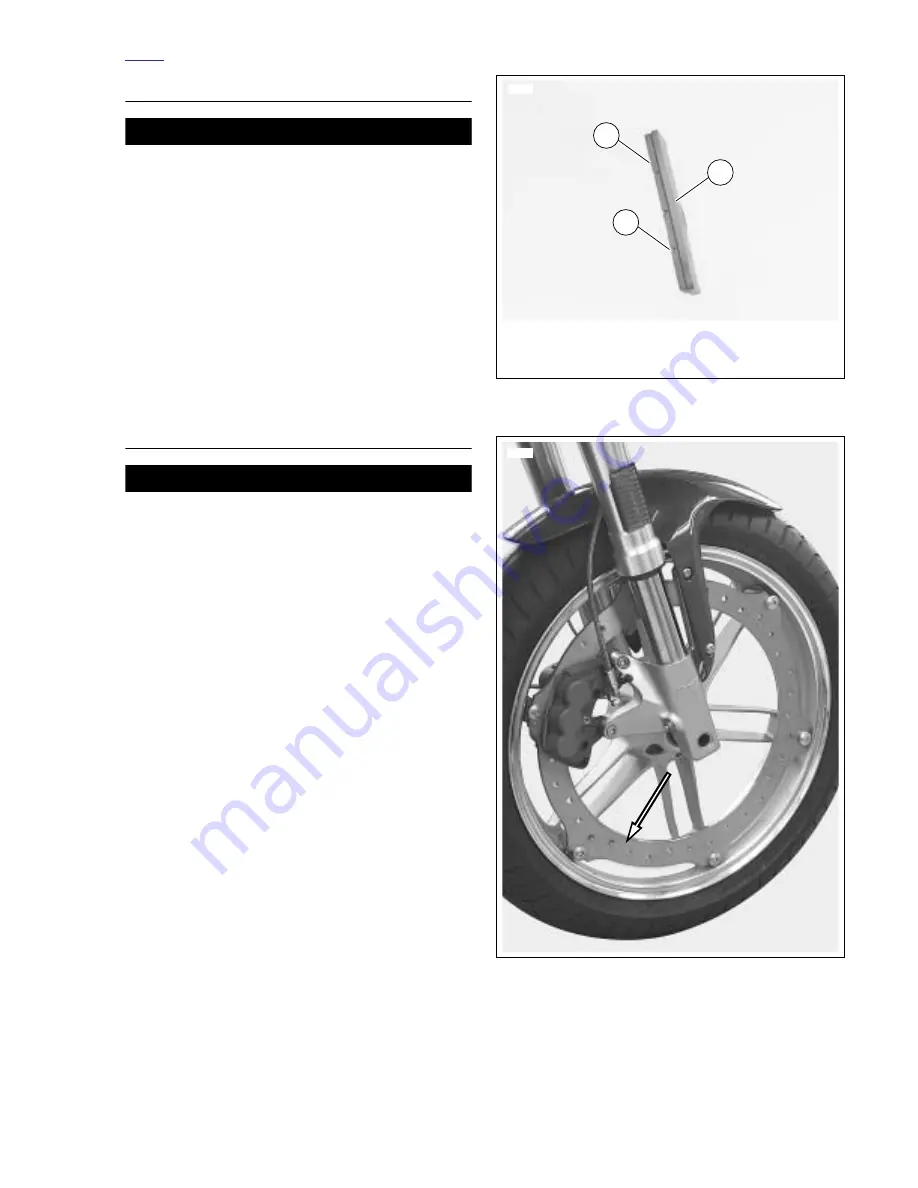
2003 Buell XB9S: Maintenance
1-19
BRAKE PAD THICKNESS
1
WARNING
1
WARNING
Always replace brake pads in complete sets for correct
brake operation. Never replace just one brake pad. Fail-
ure to install brake pads as a set could result in death or
serious injury.
Check brake pads for minimum thickness:
●
At the 1000 mile (1600 km) service interval.
●
At every 2500 miles (4000 km) service interval thereafter.
●
At every scheduled service interval thereafter.
See
Inspect brake pads for damage or excessive
wear. Replace both pads as a set if friction material of either
pad is worn to 0.040 in. (1.0 mm) or less. If this amount of
wear occurs, wear grooves will disappear from friction mate-
rial surface.
BRAKE ROTOR THICKNESS
1
WARNING
1
WARNING
Do not allow brake fluid, bearing grease, lubricants, etc.
to contact brake rotor when servicing motorcycle or
reduced braking ability will occur, which could result in
death or serious injury.
See
Check brake rotors for minimum thickness:
●
At the 1000 mile (1600 km) service interval.
●
At every 2500 miles (4000 km) service interval thereafter.
●
At every scheduled service interval thereafter.
1.
Measure rotor thickness. Replace rotor if minimum thick-
ness is less than 0.18 in. (4.5 mm). Replace drive bush-
ings, fasteners, washers and springs whenever rotor is
replaced.
2.
Check rotor surface. Replace if warped or badly scored.
See
for proce-
dure.
Figure 1-13. Brake Pad Thickness
Figure 1-14. Front Brake Rotor
7082
1.
Friction material
2.
Wear groove
3.
Backing material
1
2
3
8347
8347