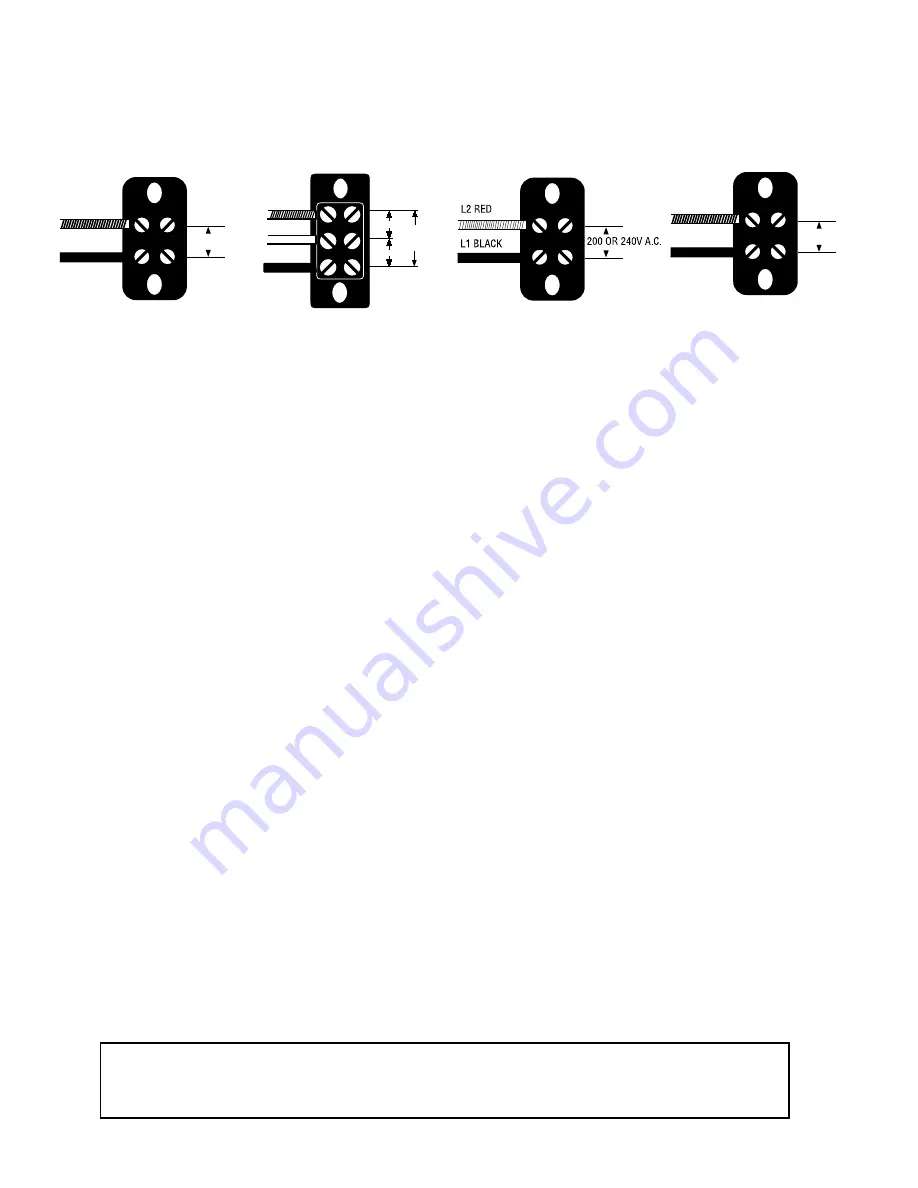
Page 4
PLUMBING REQUIREMENTS
Models S & SA:
These models are completely portable and require no attached plumbing.
Models ST, STA, STF & STFA
These brewers must be connected to a cold water system with operating pressure between 20 and 90 psi (138
and 620 kPa) from a
1
⁄
2
" or larger supply line. A shut-off valve should be installed in the line before the brewer. Install
a regulator in the line when pressure is greater than 90 psi (620 kPa) to reduce it to 50 psi (345 kPa). The water
inlet fitting is
1
⁄
4
" flare.
NOTE -
Bunn-O-Matic recommends
1
⁄
4
" copper tubing for installations of less than 25 feet and
3
⁄
8
" for more than
25 feet from the
1
⁄
2
" water supply line. A tight coil of copper tubing in the water line will facilitate moving the brewer
to clean the countertop. Bunn-O-Matic does not recommend the use of a saddle valve to install the brewer. The
size and shape of the hole made in the supply line by this type of device may restrict water flow.
ELECTRICAL REQUIREMENTS
CAUTION -
The brewer must be disconnected from the power source until specified in
Initial Set-Up.
Model 15
has an attached cordset and requires 2-wire grounded service rated 120 volts ac, 15 amp, single
phase, 60 Hz.
Model 35
requires 3-
wire, grounded service
rated 120/208 or 120/240
volts ac, 20 amp, single
phase, 60 Hz. Proceed as
follows:
Model 20
requires 2-
wire, grounded service
rated 120 volts ac, 20
amp, single phase, 60 Hz.
Proceed as follows:
Electrical Hook-Up
CAUTION –
Improper electrical installation will damage electronic components.
1.
An electrician must provide electrical service as specified.
2.
Using a voltmeter, check the voltage and color coding of each conductor at the electrical source.
3.
Before electrically connecting the brewer, remove the front and rear panel and rotate the thermostat knob fully
counterclockwise to the "OFF" position. Keep this knob in the "OFF" position until performing the "Initial Set-Up"
4.
Feed the power cord through the strain relief and connect it to the terminal block.
5.
Connect the brewer to the power source and verify the voltage at the terminal block before proceeding.
(Models S and ST-15 have cord attached. Replace all panels.
6.
If plumbing is to be hooked-up later be sure the brewer is disconnected from the power source. If plumbing
has been hooked-up, the brewer is ready for "Initial Set-Up".
NOTE: Schematic wiring diagrams are included in this manual.
“A" & "B”
models re-
quire 2-wire, grounded
service rated 200 volts ac
or 240 volts ac, 20 amp,
single phase, 50 Hz. Pro-
ceed as follows:
"SDB”
model requires
2-wire, grounded service
rated 100 volts ac, 20
amp, single phase, 50 Hz.
Proceed as follows:
This equipment must be installed to comply with the Basic Plumbing Code of the Building
Officials and Code Administrators International, Inc. (BOCA) and the Food Service Sanitation
Manual of the Food and Drug Administration (FDA).
29251 011800
P1841
L2 RED
NEUTRAL
L1 BLACK
120V A.C.
120V A.C.
208 or
240V.A.C.
WHITE
NEUTRAL
L1 BLACK
120V.A.C.
WHITE
NEUTRAL
L1 BLACK
100V.A.C.
WHITE
P2185
P2185
P2193
Summary of Contents for S
Page 31: ...Page 31 29251 052500 ...
Page 32: ...Page 32 29251 052500 ...
Page 33: ...Page 33 29251 052500 ...
Page 34: ...Page 34 29251 052500 ...
Page 35: ...Page 35 29251 052500 ...
Page 36: ...Page 36 29251 052500 ...
Page 37: ...Page 37 29251 052500 ...
Page 38: ...Page 38 29251 052500 ...
Page 39: ...Page 39 29251 052500 ...
Page 40: ...Page 40 29251 052500 ...
Page 41: ...Page 41 29251 052500 ...
Page 42: ...Page 42 29251 080400 ...
Page 43: ...Page 43 29251 052500 ...
Page 44: ......