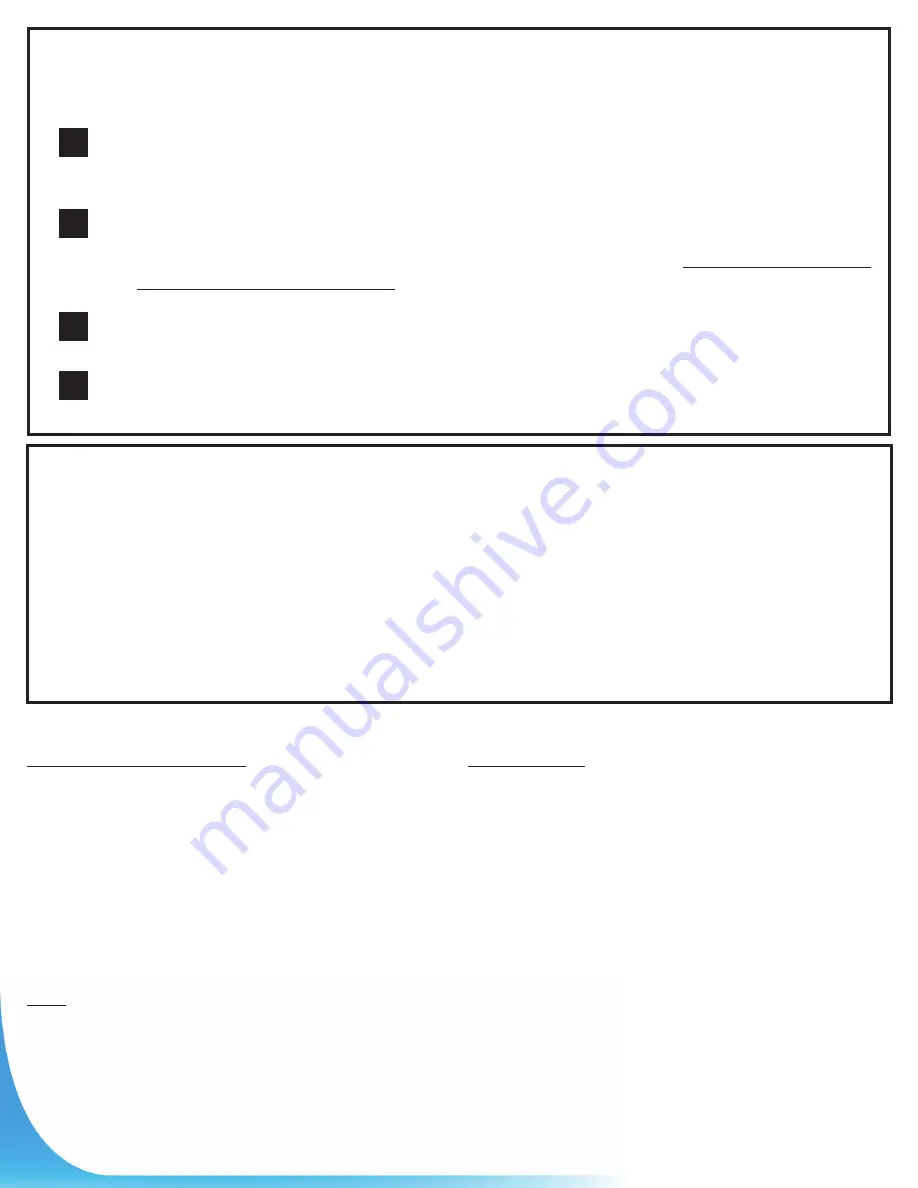
2
Safety Instructions:
This fine pump that you have just purchased is designed from the latest in material and workmanship.
Before installation and operation, we recommend the following procedures:
CHECK WITH YOUR LOCAL ELECTRICAL AND PLUMBING CODES TO ENSURE YOU COMPLY
WITH THE REGULATIONS. THESE CODES HAVE BEEN DESIGNED WITH YOUR SAFETY IN
MIND. BE SURE YOU COMPLY WITH THEM.
WE RECOMMEND THAT A SEPARATE CIRCUIT BE LEAD FROM THE HOME ELECTRICAL
DISTRIBUTION PANEL PROPERLY PROTECTED WITH A FUSE OR A CIRCUIT BREAKER. WE
ALSO RECOMMEND THAT A GROUND FAULT CIRCUIT BE USED. CONSULT A LICENSED
ELECTRICIAN FOR ALL WIRING.
THE GROUND TERMINAL ON THE THREE PRONG PLUGS SHOULD NEVER BE REMOVED.
THEY ARE SUPPLIED AND DESIGNED FOR YOUR PROTECTION.
NEVER MAKE ADJUSTMENTS TO ANY ELECTRICAL APPLIANCE OR PRODUCT WITH THE
POWER CONNECTED. DO NOT ONLY UNSCREW THE FUSE OR TRIP THE BREAKER, REMOVE
THE POWER PLUG FROM THE RECEPTACLE.
A
B
C
D
Material required for drilled well application
(indoor use only)
Shallow well pump installation
• Desired length of polyethylene 1” pipe, 100 PSI, CSA or
UL approved, to link up from pumping level to pump.
• 1 1” foot valve (750756 or 750752P).
• 1 well seal, as per well casing diameter
(750929 6” x 1”).
• 1 1” well seal elbow (750860).
• 2 1” male adaptors (750865 or 750871).
• 8 1” stainless steel clamps (750885).
• Teflon tape.
Tank installation
• Desired length of 1” braided hose (750919) to link up
from pump to tank. Keep tank as close as possible to
the pump.
• 1 tank T (650651).
• 1 drain valve (650659)
• 2 1” female adaptor.
• 1 1” male adaptor (750865 or 750871).
• 3 1” stainless steel clamps (750885).
• Teflon tape.
Tools
Screwdrivers, hacksaw to cut pipe, knife to assist in pipe cutting, round file to smooth pipe ends, pipe wrench,
adjustable wrench to tighten fittings, propane torch and welding material.
Monthly Mandatory check-up:
1. Inspect the pump for any obvious condition that necessitates cleaning, correction, adjustment or repair.
2. Clear the surrounding of any paper, leaves or other debris.
3. Ensure that the pump is secure for proper operation.
4. Ensure that there is adequate clearance from any combustible materials or structure. Stored materials
must be kept away from the pump. Shelves or cabinet structures must not be in close proximity over
the pump.
5. Ensure that the motor is securely plugged into a proper GFCI electrical outlet.
6. Test the GFCI outlet by pressing its test switch. This should prove that the outlet is energized and will trip
off to protect against a ground fault. Be sure to reset the GFCI by pressing its reset switch.
7. Observe that the plumbing can carry the water safely into the residence.