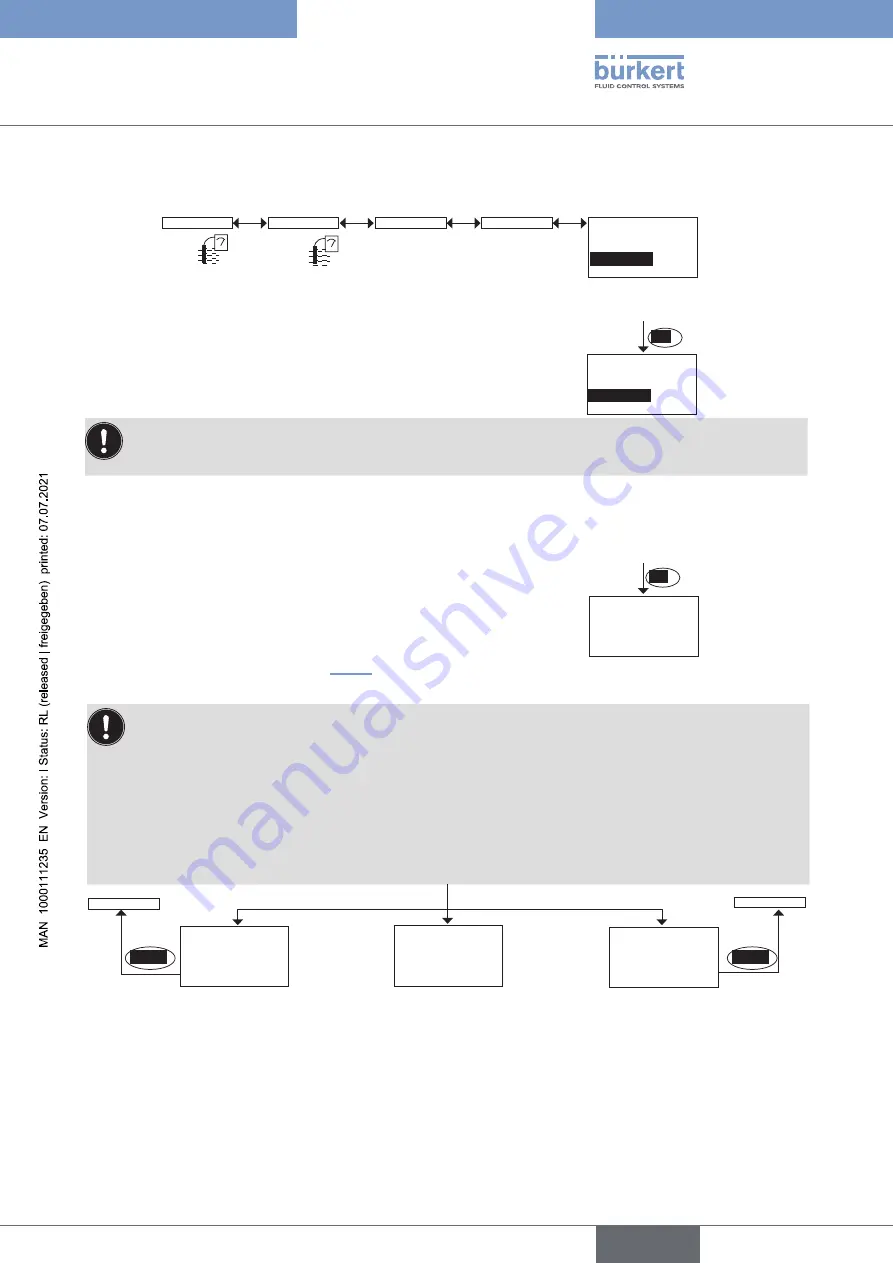
55
Adjustmentandstart-up
Define the temperature compensation graph specific to your process (“teach special” function in
the”probe” menu)
→
Enter the value for the start of the temperature range for which
the compensation graph must be determined.
→
Enter the value of the end of the temperature range for which
the compensation graph must be determined.
→
Before confirming to begin the procedure, check that the fluid
temperature is below 25 °C and T–.
OK
The message “Error: current temp. is too high”
is displayed if, at the beginning of the Teach-
In procedure, the fluid temperature is higher
than 25 °C or than T–.
If the Hold mode is deactivated (chpt. 9.12.1), the device determines the compensation graph with 10 points and
displays alternately the measured solution conductivity and the measured solution temperature.
• During measurement, the fluid temperature must pass 25 °C.
• Immerse the sensor in the solution and progressively reheat:
- from T– to T+ if T– < 25 °C < T+
- from 25 °C to T+ if 25 °C < T– < T+
- from T– to 25 °C if T– < T+ < 25 °C
• The rise in temperature must be slow because of the inertia of the temperature sensor.
• Avoid the formation of bubbles on the conductivity sensor.
The fluid temperature range (T–; T+) must be entered in such a way that the difference between T– and
T+ is greater than 8 °C. The message "Error: Temp span at least 8 °C" is displayed if the difference
between the range start and end values is less than 8 °C.
The message "Error: Temp
span at least 8 °C" is displayed
if the difference between the
range start and end values is
less than 8 °C.
BACK
Calib
Sensor
Teach special
Probe
At the end of processing,
you are requested to save
the calculated graph or not.
Cal. Result
Save: Yes/No
“Error: current
temp. is too
high”
Probe
Start temp
+40.00 °C
Stop temp
+55.00 °C
OK
Processing...
1.234 mS
"Error: temp
span at least
8 °C"
BACK
Probe
English
Type 8222 ELEMENT