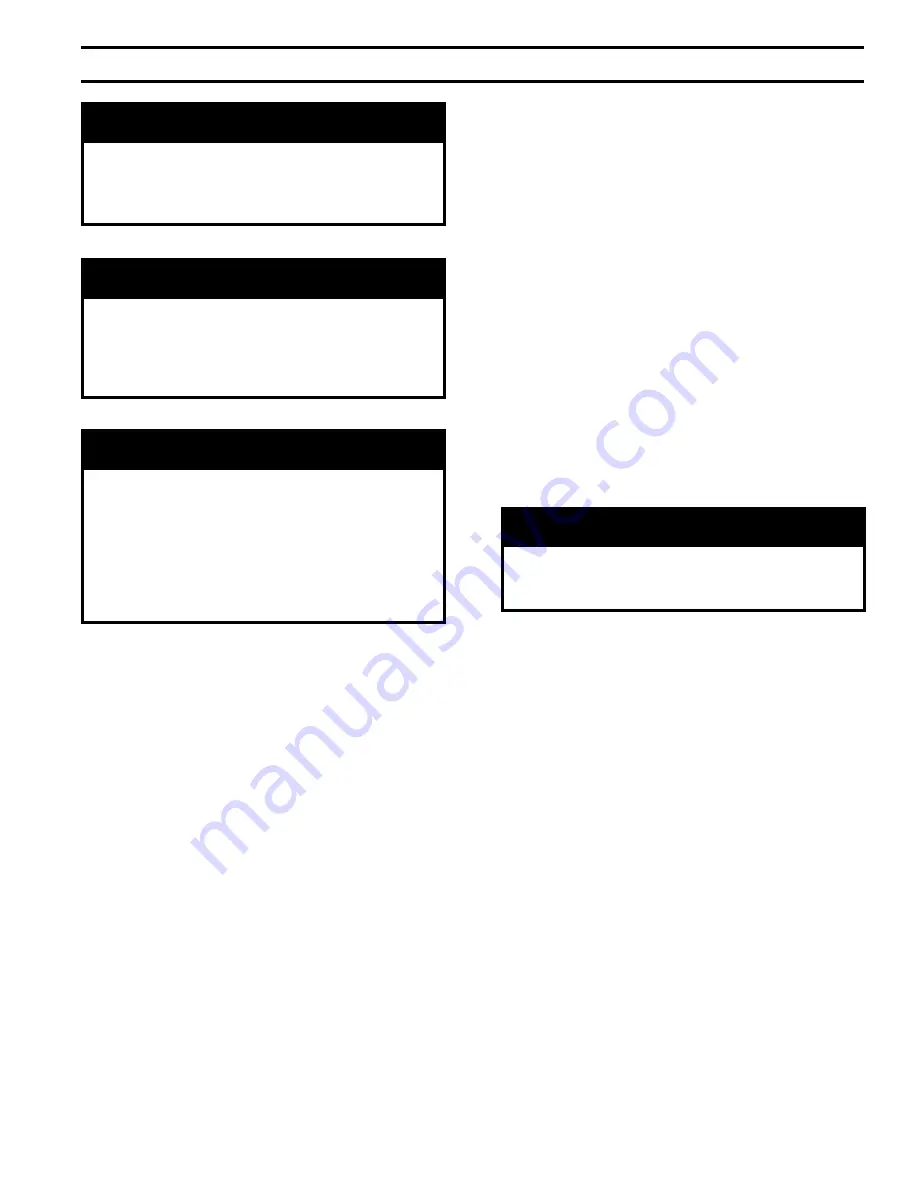
7
I. Pre-Installation
A.
Inspect shipment carefully for any signs of damage. All
equipment is carefully manufactured, inspected and
packed. Our responsibility ceases upon delivery of
boiler to carrier in good condition. Any claim for
damage or shortage in shipment must be filed
immediately against carrier by consignee. No claims for
variances or shortages will be allowed by Boiler
Manufacturer, unless presented within sixty (60) days
after receipt of equipment.
B.
Installation must conform to the requirements of the
authority having jurisdiction. In the absence of such
requirements, installation must conform to the
National
Fuel Gas Code
, NFPA 54/ANSI Z223.1 and/or CAN/
CGA B149 Installation Codes.. Where required by the
authority having jurisdiction, the installation must
conform to the
Standard for Controls and Safety
Devices for Automatically Fired Boilers
, ANSI/ASME
No. CSD-1.
C.
Appliance is design certified for installation on
combustible flooring. Boiler must not be installed on
carpeting.
D.
Provide clearance between boiler jacket and
combustible material in accordance with local fire
ordinance. See Figure 3 for minimum listed clearance
to combustible material. Recommended service
clearance is 24 inches from left side, right side, and
front. Additional clearance may be required on left side
if optional tankless heater is installed. Service
clearances may be reduced to minimum clearances to
combustible materials.
E.
Install boiler on level floor as close to chimney as
possible. For basement installation provide a solid base,
such as concrete, steel or masonry if floor is not level or
if water may be encountered on floor around boiler.
F.
Protect gas ignition system components from water
(dripping, spraying, rain, etc.) during boiler operation
and service (circulator replacement, control
replacement, etc.).
G.
Provide combustion and ventilation air in accordance
with applicable provisions of local building codes, or
the
National Fuel Gas Code
, NFPA 54/ANSI Z223.1,
Section 5.3, Air for Combustion and Ventilation; or
CAN/CGA B149 Installation Codes, Sections 7.2, 7.3
or 7.4.
G
N
I
N
R
A
W
r
i
a
n
o
i
t
a
li
t
n
e
v
d
n
a
n
o
i
t
s
u
b
m
o
c
e
t
a
u
q
e
d
A
r
e
p
o
r
p
e
r
u
s
s
a
o
t
d
e
d
i
v
o
r
p
e
b
t
s
u
m
.
n
o
i
t
s
u
b
m
o
c
The following guideline is based on the
National Fuel
Gas Code
, NFPA 54/ANSI Z223.1.
1. Determine volume of space (boiler room). Rooms
communicating directly with space (through
openings not furnished with doors) are considered
part of space.
Volume [ft³] = Length [ft] x Width [ft] x Height [ft]
2. Determine Total Input of all appliances in space.
Round result to nearest 1,000 Btu per hour (Btuh).
3. Determine type of space. Divide Volume by Total
Input.
a. If result is greater than or equal to 50 ft³ per
1,000 Btuh, space is considered an
unconfined
space
.
b. If result is less than 50 ft³ per 1,000 Btuh, space
is considered a
confined space
.
4. Determine building type. A building of
unusually
tight construction
has the following characteristics:
a. Walls and ceiling exposed to outside atmosphere
have a continuous water vapor retarder with a
rating of 1 perm or less with openings gasketed
and sealed, and
b. Weather-stripping has been added on openable
windows and doors, and
G
N
I
N
R
A
W
s
n
o
i
t
c
u
r
t
s
n
i
e
s
e
h
t
w
o
ll
o
f
t
o
n
o
d
u
o
y
f
I
t
l
u
s
e
r
y
a
m
n
o
i
s
o
l
p
x
e
r
o
e
r
i
f
a
,
y
l
t
c
a
x
e
l
a
n
o
s
r
e
p
r
o
e
g
a
m
a
d
y
t
r
e
p
o
r
p
g
n
i
s
u
a
c
.
y
r
u
j
n
i
R
E
G
N
A
D
r
e
h
t
o
r
o
e
n
il
o
s
a
g
e
r
e
h
w
r
e
li
o
b
ll
a
t
s
n
i
t
o
n
o
D
f
o
s
e
c
r
u
o
s
r
o
,
s
d
i
u
q
il
r
o
s
r
o
p
a
v
e
l
b
a
m
m
a
l
f
,
s
r
e
n
a
e
l
c
,
s
e
h
c
a
e
l
b
.
e
.i
(
s
n
o
b
r
a
c
o
r
d
y
h
c
i
r
b
a
f
,
s
r
e
v
o
m
e
r
t
n
i
a
p
,
s
y
a
r
p
s
,
s
l
a
c
i
m
e
h
c
.
d
e
r
o
t
s
r
o
d
e
s
u
e
r
a
)
.
c
t
e
,
s
r
e
n
e
t
f
o
s
E
C
I
T
O
N
,
r
e
li
o
b
e
h
t
f
o
t
n
e
t
n
o
c
r
e
t
a
w
w
o
l
e
h
t
o
t
e
u
D
e
h
t
o
t
d
r
a
g
e
r
h
t
i
w
r
e
li
o
b
e
h
t
f
o
g
n
i
z
i
s
-
s
i
m
e
v
i
s
s
e
c
x
e
n
i
t
l
u
s
e
r
ll
i
w
d
a
o
l
m
e
t
s
y
s
g
n
i
t
a
e
h
t
n
e
n
o
p
m
o
c
d
e
t
a
r
e
l
e
c
c
a
d
n
a
g
n
il
c
y
c
r
e
li
o
b
t
n
a
r
r
a
w
T
O
N
S
E
O
D
m
a
h
n
r
u
B
.
e
r
u
li
a
f
r
e
li
o
b
d
e
z
i
s
-
s
i
m
y
b
d
e
s
u
a
c
s
e
r
u
li
a
f
o
t
r
e
li
o
b
e
h
t
e
z
i
s
r
e
v
o
T
O
N
O
D
.
s
n
o
i
t
a
c
il
p
p
a
.
m
e
t
s
y
s
e
h
t
Summary of Contents for Independence
Page 4: ... Figure 1 Dimensional Drawing ...
Page 19: ...19 Figure 25 Recommended Water Piping for Circulator Zoned Heating System ...
Page 20: ...20 Figure 25A Recommended Water Piping for Zone Valve Zoned Heating System ...
Page 29: ...29 Figure 34 Vent Damper Schematic Wiring Diagram Figure 33 Vent Damper Harness to Limit ...
Page 30: ...30 Figure 35 Wiring Diagrams Steam Continuous Ignition Standing Pilot Probe Low Water Cutoff ...
Page 32: ...32 Figure 36 Wiring Diagrams Steam Intermittent Ignition EI Probe Low Water Cutoff ...
Page 34: ...34 Figure 37 Wiring Diagrams Steam Intermittent Ignition HSP Probe Low Water Cutoff ...
Page 36: ...36 Figure 38 Wiring Diagrams Steam Continuous Ignition Standing Pilot Float Low Water Cutoff ...
Page 38: ...38 Figure 39 Wiring Diagrams Steam Intermittent Ignition EI Float Low Water Cutoff ...
Page 40: ...40 Figure 40 Wiring Diagrams Steam Intermittent Ignition HSP Float Low Water Cutoff ...
Page 44: ...44 Figure 42 Wiring Diagrams Water Intermittent Ignition EI Intermittent Circulation ...
Page 46: ...46 Figure 43 Wiring Diagrams Water Intermittent Ignition HSP Intermittent Circulation ...
Page 48: ...48 Figure 44 Wiring Diagrams Water Continuous Ignition Standing Pilot Gravity Circulation ...
Page 50: ...50 Figure 45 Wiring Diagrams Water Intermittent Ignition EI Gravity Circulation ...
Page 52: ...52 Figure 46 Wiring Diagrams Water Intermittent Ignition HSP Gravity Circulation ...
Page 54: ...54 Figure 47 Wiring Diagrams Water Continuous Ignition Standing Pilot Tankless Heater ...
Page 56: ...56 Figure 48 Wiring Diagrams Water Intermittent Ignition EI Tankless Heater ...
Page 58: ...58 Figure 49 Wiring Diagrams Water Intermittent Ignition HSP Tankless Heater ...
Page 61: ...61 Figure 53 Lighting Instructions Continuous Ignition System VR8200 and VR8300 Gas Valves ...
Page 62: ...62 Figure 54 Lighting Instructions Continuous Ignition System 7000 ERHC Gas Valve ...
Page 65: ...65 Figure 57 Operating Instructions Intermittent Ignition System HSP SV9501 and SV9601 ...
Page 76: ...76 ...
Page 77: ...77 Honeywell Hot Surface to Pilot Trouble Shooting Guide ...
Page 91: ...91 THIS PAGE LEFT BLANK INTENTIONALLY ...
Page 92: ...92 ...
Page 96: ...96 ...
Page 99: ...99 THIS PAGE LEFT BLANK INTENTIONALLY ...
Page 100: ...100 ...