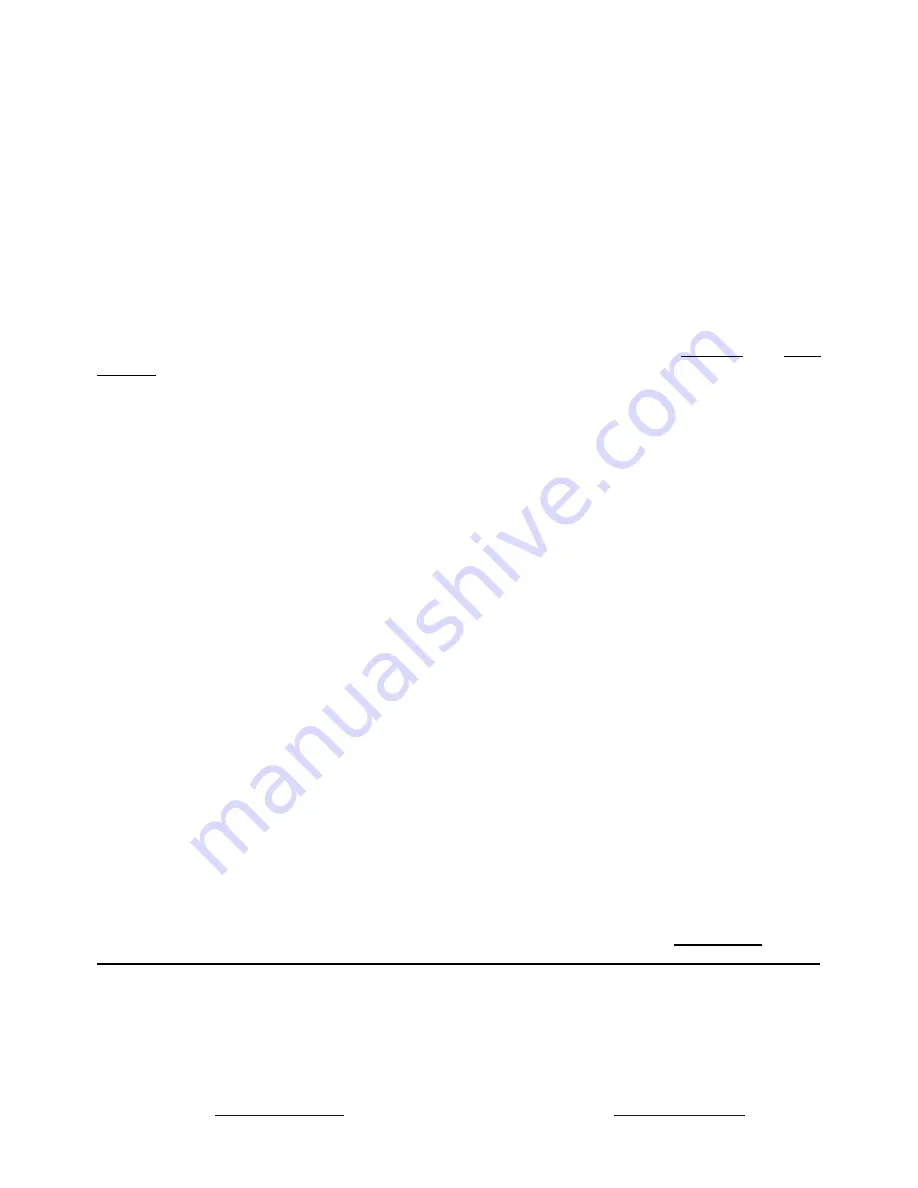
See our catalog at
www.burrking.com
Contact us at
info@burrking.com
DOC760OP-99 REV 04/02
2
Functional operating instructions for the model 760 belt grinder
The model 760 was fully tested and verified to comply with requirements prior to shipping from the factory.
You should perform the following steps:
1. With the machine securely bolted to its table, pedestal, and/or floor point connect the AC power to its
source.
2.
Adjust the work support and work support arm (P/N 706, 705) to the desired position. Take care that the
gap between the face of the abrasive belt and the work rest is at most 1/8 inch.
WARNING
:
Be aware
that thin section work pieces can pass through this gap if the gap is not properly adjusted. Ejected
work parts can cause serious personal injury!
3. Insure that the abrasive belt is tensioned properly. To do this, raise the tensioning handle (P/N 737A). You
will hear mechanical clicks as the tensioning ratchet (P/N 736, 737F) moves. Generally, the belt will be
adequately tensioned when you hear three to eight clicks. To reduce or release the belt tension slightly raise
the tensioning handle (P/N 737A) then press the button (P/N 737B) in the center of the tensioning handle.
Move the tensioning handle down slightly to reduce belt tension or all the way down to release belt tension.
4. Engage the motor by placing the ON/OFF switch to ON. The belt should rotate smoothly in a CCW
direction about the machine wheel belt path. If either of these conditions is not met immediately turn the
machine OFF.
a. If the abrasive belt does not remain centered on the contact wheel (P/N 702) while the belt is
moving use the tracking adjustment (P/N 711) on the upper left side of the machine to track the belt. Turning
this control CW to cause the belt to track to the left, conversely turn the control CCW to cause the belt to
move to the right.
b. If the belt runs in reverse ( up from the floor) you must correct this unsafe condition by changing
the main drive motor rotation direction.
WARNING: FIRST DISCONNECT THE MACHINE FROM
ITS AC POWER SOURCE. A COMPETENT ELECTRICIAN SHOULD PERFORM ALL
ELECTRICAL WORK ON THE MODEL 760.
1) Reversed the motor direction of a three phase motor by reversing any
two legs of the input power lines.
2) Reverse the motor direction of a single phase motor by reversing leads 5 and 8 found
within the metal wiring box located on the motor, or as otherwise instructed on the actual
motor label.
c. If the abrasive belt tensions, and tracks properly, but has excessive vibration turn the machine OFF
and call the Burr King factory for assistance.
Maintenance for the model 760
WARNING: FIRST DISCONNECT THE MACHINE FROM ITS AC POWER SOURCE.
* Every thirty days apply light machine oil to the rear wheel support (P/N 735) to rear wheel handle (P/N
737G) interface. Two drops of oil is sufficient.
* Every thirty days check the v-belt (P/N 729) tension. If you can hear the belt “slap” the v-belt guard (P/N
728) when the drive motor starts, the v-belt requires re-tensioning. Do this by loosening the four bolts (P/N
2) that secure the motor to the machine base (P/N 731) and slide the motor toward the rear of the machine.
Tighten the four bolts.
* Daily vacuum or otherwise remove dust and debris build-up from the machine and the machine belt track.
There are no other maintenance actions required. All bearings are sealed for life and require no additional
lubrication.
---------------------------------------------------------------------------------------------------------
WARNING,
AVOID INJURY: operator safety and the continued effectiveness of your model 760 requires that you:
Do not defeat the safety guards and other safety provisions of the model 760.
Do not operate the model 760 with the safety guard open or the contact wheel guard/platen assembly
(or internal grinding attachment) removed.
Do not reach inside the safety guards while the machine is running. To do so is hazardous.
Do not use fluids in your grinding process unless your model 760 is designed for liquid operation
(NEMA 4, 4X). To do so may create an electrical safety hazard.