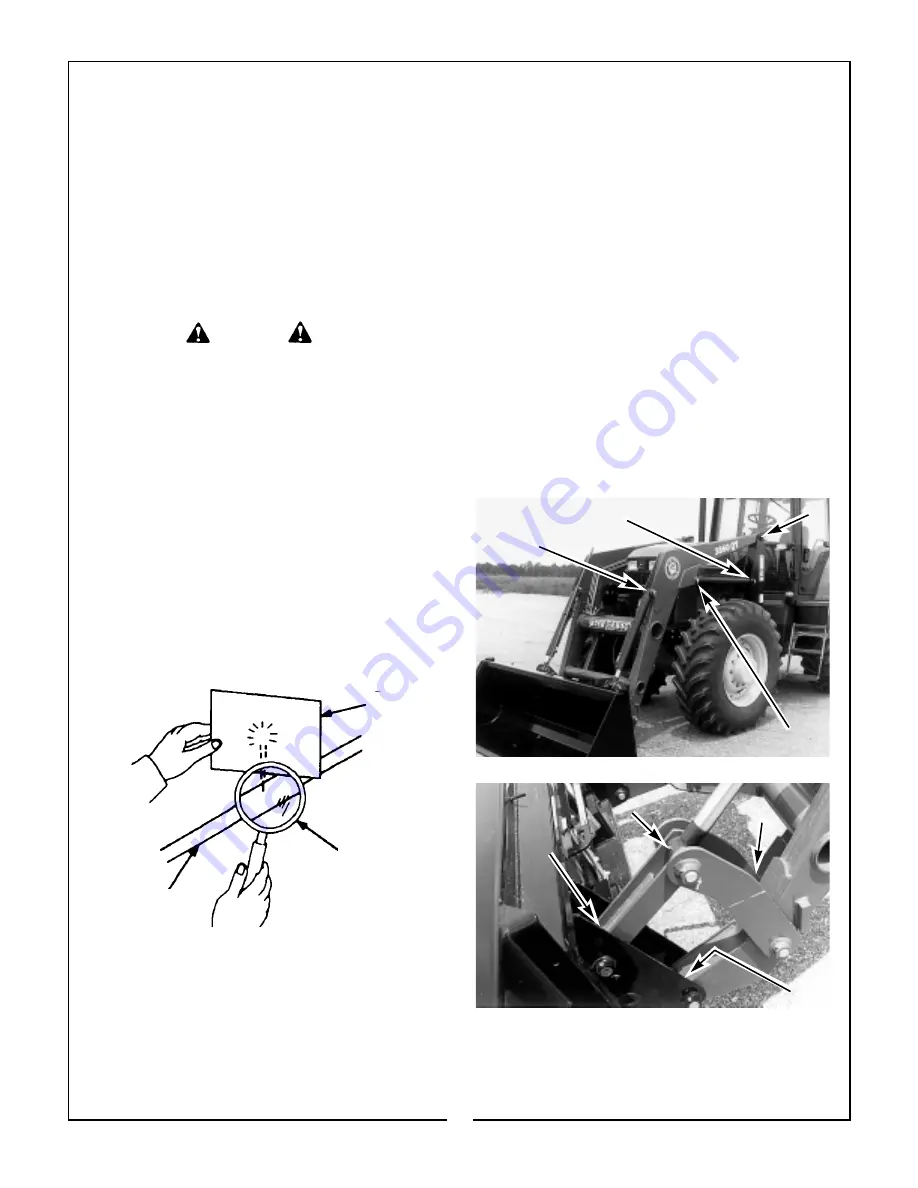
4. MAINTENANCE
DAILY CHECKS
Check all hardware daily before operation.
Tighten hardware to torque values as specified in
the Torque Chart, page 43 unless otherwise speci-
fied.
With the engine off and the bucket on the ground,
inspect all hoses for cuts or wear. Check for signs of
leaks and make sure all fittings are tight.
CAUTION
ESCAPING HYDRAULIC FLUID UNDER
PRESSURE CAN HAVE SUFFICIENT
FORCE TO PENETRATE SKIN, CAUSING
SERIOUS PERSONAL INJURY. BEFORE
DISCONNECTING LINES, BE SURE TO
RELIEVE ALL PRESSURE.
BEFORE APPLYING PRESSURE TO SYS-
TEM, BE SURE ALL CONNECTIONS ARE
TIGHT AND THAT LINES, TUBES, AND
HOSES ARE NOT DAMAGED.
FLUID ESCAPING FROM A VERY SMALL
HOLE CAN BE ALMOST INVISIBLE. USE A
PIECE OF CARDBOARD OR WOOD,
RATHER THAN HANDS, TO SEARCH FOR
SUSPECTED LEAKS.
IF INJURED BY ESCAPING FLUID, SEE A
DOCTOR AT ONCE. SERIOUS INFECTION
OR REACTION CAN DEVELOP IF PROPER
MEDICAL TREATMENT IS NOT ADMINIS-
TERED IMMEDIATELY. REFER TO FIGURE 1.
Figure 1
2
3
1
(1) Hydraulic line.
(2) Cardboard.
(3) Magnifying glass.
Service your loader at the intervals and locations as
specified. When you service your loader, use only
high quality lubricants. The engine hour meter on the
tractor shows the amount of hours the engine has
worked. Use the hour meter to service your loader at
the correct time periods.
IMPORTANT: Lower the loader boom to the
ground and relieve pressure in loader hydraulic
lines prior to doing any service or maintenance
operations on the tractor or loader.
Check the tractor hydraulic fluid level as speci-
fied in the tractor Operator Manual.
NOTE: When checking hydraulic system fluid
level, the loader boom must be on the ground
with the bucket or attachment resting flat on a
level surface.
LOADER LUBRICATION
Position bucket and/or attachment level with ground,
lower loader boom to ground, and relieve all
hydraulic pressure before lubricating. Refer to
Figures 2 & 3.
There are 16 grease fittings on the Model 3860
Loader, one at each pivot point. Lubricate pivots as
specified.
Figure 2
(1) Lubricate these 8 pivot points every 10 hours of
operation.
(2) Lubricate these 8 pivot points every 5 hours of
operation.
Figure 3
1
1
1
1
2
2
2
2
15