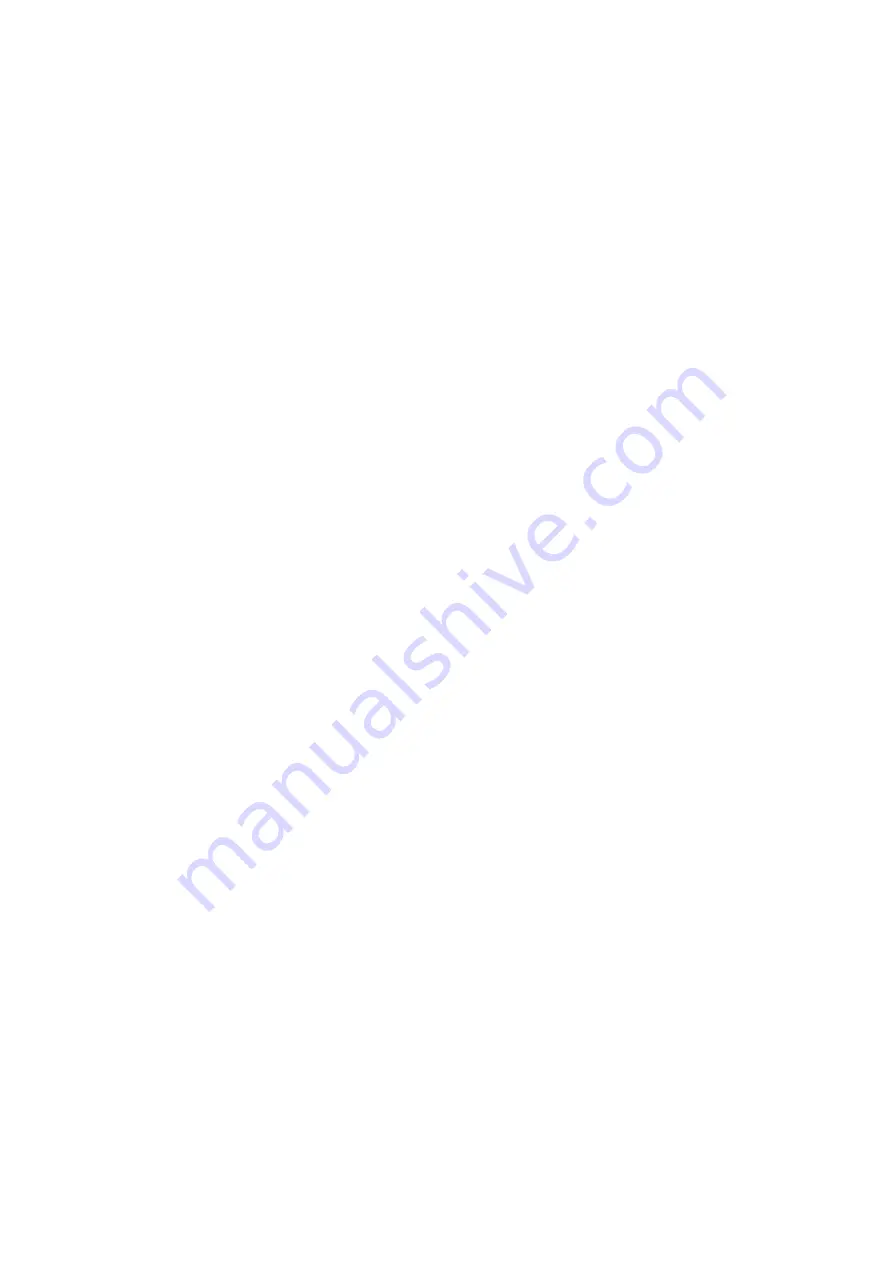
15
Simple Rules for Dismantling and Re-Assembling Imovilli Pumps
Point 1
Before completely dismantling the pump, check that the causes for irregular running or non-function are not
amongst those indicated in the maintenance and instructions booklet supplied with each pump.
Point 2
To substitute diaphragms or internal moving parts, dismantle in the following order:
A)
Suction manifold(s) (according to the type of pump)
B)
Heads
C)
Diaphragms
D)
Cylinders
E)
Pump shaft and then all the moving parts
The exploded drawing in the instructions booklet and spare parts catalogue should be of assistance.
Point 3
Carefully wash all the components with diesel oil, blow clean with compressed air, and then inspect all the parts:
Diaphragms
By inspecting the diaphragm damage one can determine the type of problem.
If the diaphragm has a cut (on the oil side) of the same diameter as the piston, the pump has been running at a
speed of less than 250-300 rpm.
Whenever there is a diaphragm failure on the oil side, with a circular rupture corresponding to the size of the
piston, one should always check that the piston/cylinder are not scored or worn. Otherwise, if this is the case, the
new diaphragms would have a very short life since the oil will not remain between the piston and diaphragm and
the latter will work only mechanically (without hydraulic support).
If there is a circular or semi-circular cut on the centre/outside of the diaphragm on the liquid side, the pump has
worked under a vacuum due to: Blocked suction Equipment, -
“soft “ suction tubes which flatten during operation,
- under dimensioned filter equipment, or a dirty filter.
All these result in too much oil gathering between the piston and the diaphragm, which causes the diaphragm to
literally burst.
Diaphragms can be damaged also if the client will not release pressure when stopping/starting the pump.
N.B. The use of particularly corrosive or concentrated products can also alter the diaphragm structure causing
swelling of the part in contact with the liquid and increasing the likelihood of failure.
Cylinders
These should have no lines from the oil supply holes outwards (flange). If they do they should be replaced.
Connecting Rods
There should be no excessive play between connecting rods/bearings and the connecting rods and their coupling
rings. To check this, position shaft in a vice and mount bearings, connecting rods and rings. The play should not
exceed 0,2-0,3mm.
Crank Shaft
The shaft should have no lines or wear on the part where the connecting rods work.
Shaft Seal Bearings
Premature and repeated impute shaft oil seal failure. If the seat and the shaft are not scored or worn and
tolerances are ok (if not pump will leak also when sitting) the only reason beside normal wear of the seal
(increased in dusty conditions) can be damage on the seal itself when placed into position. The keyway has very
sharp edges and much attention should be given to this operation. It is always advisable to protect the seal with a
thin pipe.
Bearings
The bearings should be rust-free and have no excessive play. Check that the rollers and balls in the bearings are
in perfect condition.