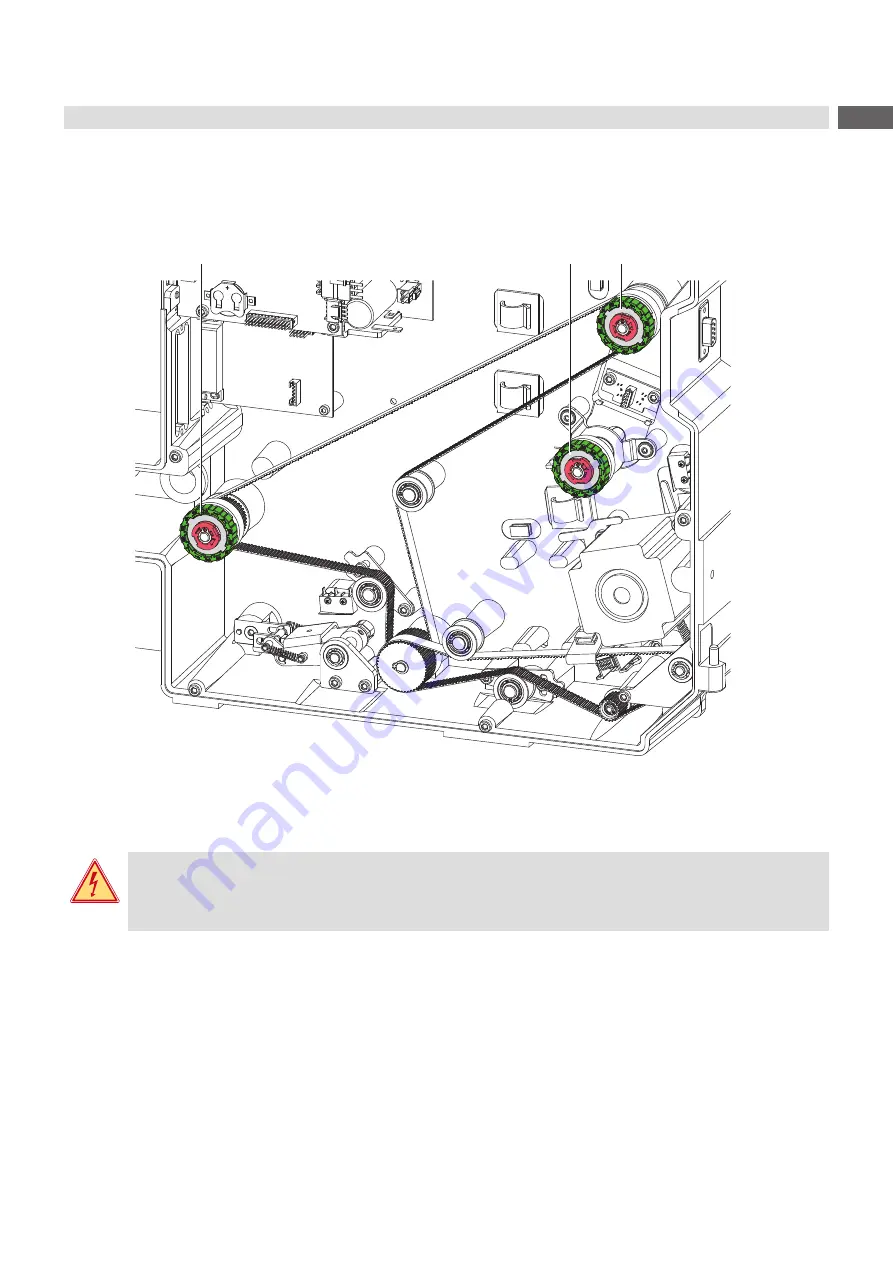
11
4.3
Replacing the Slipping Clutches
The rewinder for the transfer ribbon and the internal rewinder are coupled with slipping clutches to the main drive.
The supply hub of the transfer ribbon is braked with a slipping clutch during printing.
Replace a slipping clutch when the set value of the torque cannot be set
Removal and installation of the slipping clutch is also required for replacement of a winder.
1
2
3
1 Internal rewinder: coupling
2 Ribbon supply hub: brake
3 Ribbon take up hub: coupling
Figure 5
Slipping clutches
Danger!
Risk of death via electric shock!
Before opening the housing cover, disconnect the device from the mains supply and wait at least one
minute until the power supply unit has discharged.