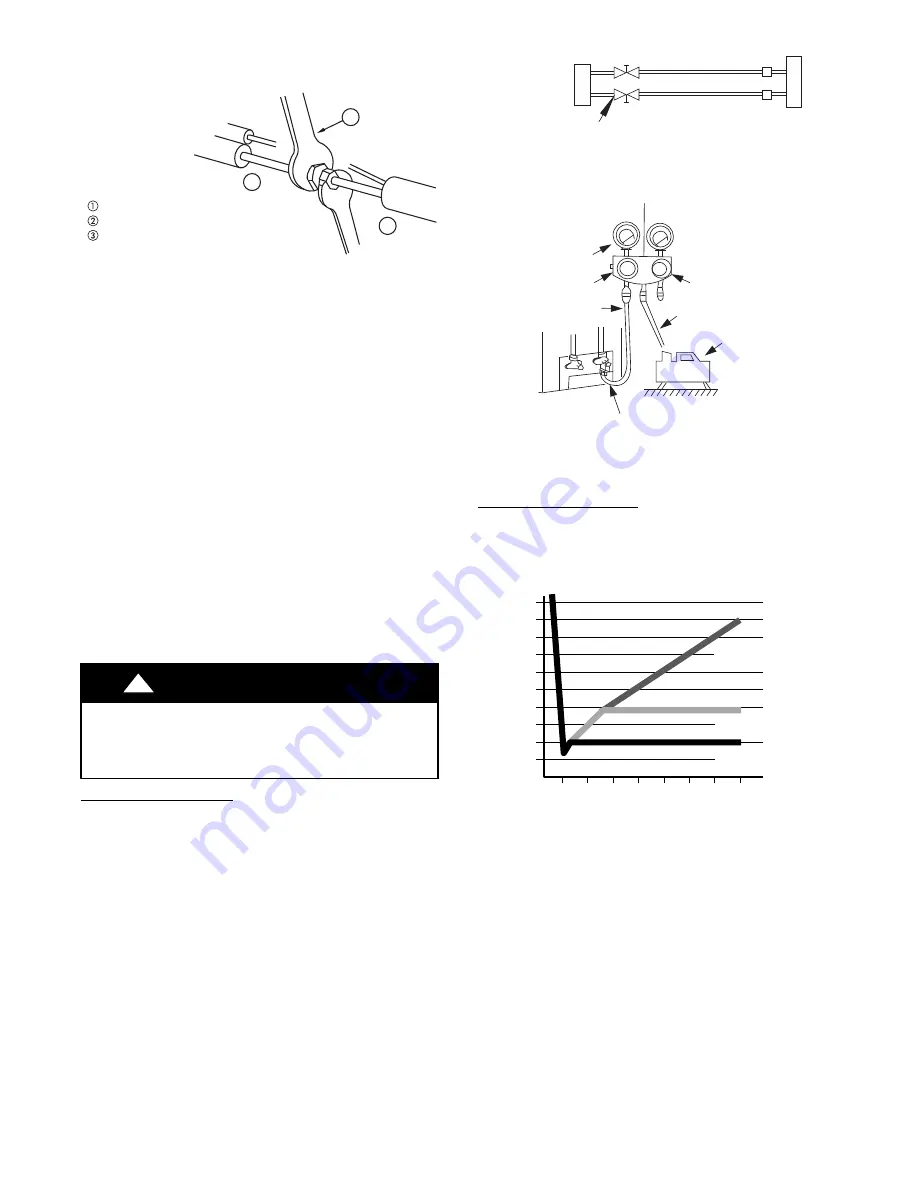
19
6. Lubricate the end of the pipe and thread of the flare
connection with refrigerant oil. Tighten by hand and then
use two wrenches (see Fig. 39) to tighten all connections.
Adjustable wrench or torque wrench
Outdoor end
Indoor end
3
1
2
A07201
Fig. 39 – Tightening Connections
START--UP
PRELIMINARY CHECKS
1. Check condensate drainage system; on the opposite side of
the drain connection, insert a water bottle up into the fan
coil unit and fill the drain pan. Water must flow steadily; if
not, check the pipe slope or inspect for any pipe restrictions.
2. Make sure all wiring connections are correct and they are
tight.
3. Field electrical power source must agree with unit name
plate rating.
4. Check that all barriers, covers, and panels are in place.
Ensure that the filters and return--air grilles on the indoor
unit have been installed and that the discharge louvers are
positioned correctly.
5. All service valves must be closed.
6. On units with crankcase heaters, ensure belly--band heaters
are tight around the compressor.
EVACUATE AND DEHYDRATE THE
SYSTEM
CAUTION
!
UNIT DAMAGE HAZARD
Failure to follow this caution may result in equipment damage
or improper operation.
Never use the system compressor as a vacuum pump.
Using Vacuum Pump
1. Completely tighten flare nuts A, B, C, D, connect manifold
gage charge hose to a charge port of the low side service
valve (see Fig. 40).
2. Connect charge hose to vacuum pump.
3. Fully open the low side of manifold gage (see Fig. 41).
4. Start vacuum pump
5. Evacuate using either deep vacuum or triple evacuation
method.
6. After evacuation is complete, fully close the low side of
manifold gage and stop operation of vacuum pump.
7. The factory charge contained in the outdoor unit is good for up
to 25 ft. (8 m) of line length. For refrigerant lines longer than
25 ft. (8 m), add charge up to the maximum allowable length
as specified in the residential Long Line Application Guide.
8. Disconnect charge hose from charge connection of the low
side service valve.
9. Fully open service valves B and A.
10. Securely tighten caps of service valves.
Outdoor Unit
Indoor Unit
Refrigerant
Service Valve
Low Side
High Side
A
B
C
D
A07360
Fig. 40 – Service Valve
Manifold Gage
500 microns
Low side valve
High side valve
Charge hose
Charge hose
Vacuum pump
Low side valve
A07361
Fig. 41 – Manifold
Deep Vacuum Method
The deep vacuum method requires a vacuum pump capable of
pulling a vacuum of 500 microns and a vacuum gage capable of
accurately measuring this vacuum depth. The deep vacuum method
is the most positive way of assuring a system is free of air and
liquid water (see Fig. 42).
500
MINUTES
0
1
2
3
4
5
6
7
1000
1500
LEAK IN
SYSTEM
VACUUM TIGHT
TOO WET
TIGHT
DRY SYSTEM
2000
MI
CRONS
2500
3000
3500
4000
4500
5000
A95424
Fig. 42 – Deep Vacuum Graph