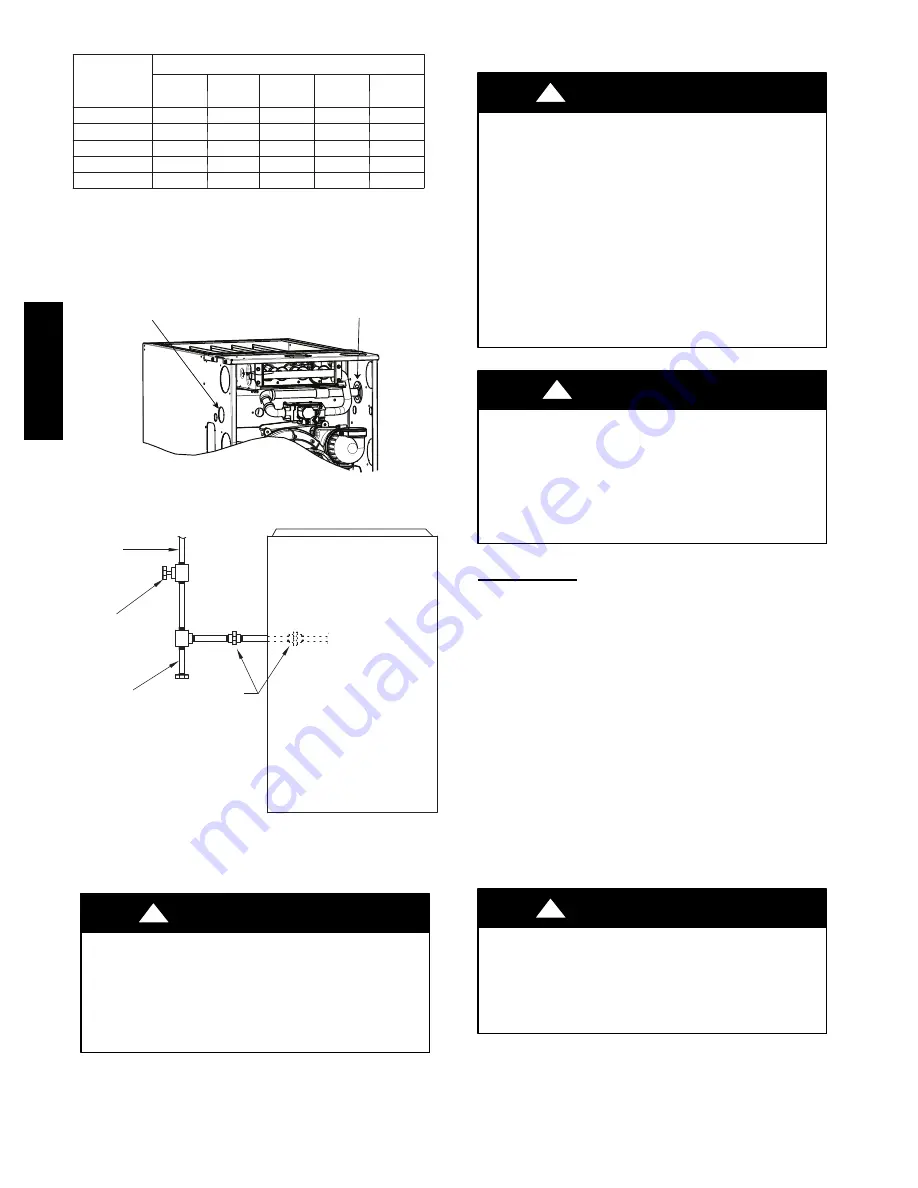
32
Table 10 – Maximum Capacity of Pipe
NOMINAL
IRON PIPE
SIZE
IN. (MM)
LENGTH OF PIPE --- FT (M)
10
(3.0)
20
(6.0)
30
(9.1)
40
(12.1)
50
(15.2)
1/2 (13)
175
120
97
82
73
3/4 (19)
360
250
200
170
151
1 ( 25)
680
465
375
320
285
1-1/4 (32)
1400
950
770
660
580
1-1/2 (39)
2100
1460
1180
990
900
* Cubic ft of gas per hr for gas pressures of 0.5 psig (14---in. w.c.) or less
and a pressure drop of 0.5---in. w.c. (based on a 0.60 specific gravity gas).
Ref: Table 10 above and 6.2 of NFPA54/ANSI Z223.1---2009.
Gas Pipe Grommet Required
For Direct Vent Applications
Left Side Gas Entry. Gas Pipe
Grommet Required For Direct
Vent Applications.
A11338
Fig. 30 -- Gas Entry
GAS
SUPPLY
MANUAL
SHUT OFF
VALVE
(REQUIRED)
SEDIMENT
TRAP
UNION
NOTE: Union may be inside the
vestibule where permitted by
local codes.
FRONT
A11035
Fig. 31 -- Typical Gas Pipe Arrangement
ELECTRICAL CONNECTIONS
ELECTRICAL SHOCK HAZARD
Failure to follow this warning could result in personal
injury or death.
Blower door switch opens 115--v power to control. No
component operation can occur. Do not bypass or close
switch with blower door removed.
!
WARNING
See Fig. 35 for field wiring diagram showing typical field 115--v
wiring. Check all factory and field electrical connections for
tightness.
Field--supplied wiring shall conform with the limitations of 63
_
F
(33
_
C) rise.
ELECTRICAL SHOCK AND FIRE HAZARD
Failure to follow this warning could result in personal
injury, death, or property damage.
The cabinet MUST have an uninterrupted or unbroken
ground according to NEC ANSI/NFPA 70--2011 or local
codes to minimize personal injury if an electrical fault
should occur. In Canada, refer to Canadian Electrical Code
CSA C22.1. This may consist of electrical wire, conduit
approved for electrical ground or a listed, grounded power
cord (where permitted by local code) when installed in
accordance with existing electrical codes. Refer to the
power cord manufacturer’s ratings for proper wire gauge.
Do not use gas piping as an electrical ground.
!
WARNING
FURNACE MAY NOT OPERATE HAZARD
Failure to follow this caution may result in intermittent
furnace operation.
Furnace control must be grounded for proper operation or
else control will lock out. Control must remain grounded
through green/yellow wire routed to gas valve and manifold
bracket screw.
CAUTION
!
115--V Wiring
Furnace must have a 115-v power supply properly connected and
grounded.
NOTE
: Proper polarity must be maintained for 115-v wiring. If
polarity is incorrect, control LED status indicator light will flash
rapidly and furnace will
NOT
operate.
Verify that the voltage, frequency, and phase correspond to that
specified on unit rating plate. Also, check to be sure that service
provided by utility is sufficient to handle load imposed by this
equipment. Refer to rating plate or Table 11 for equipment
electrical specifications.
U.S.A. Installations
: Make all electrical connections in accordance
with the current edition of the National Electrical Code (NEC)
ANSI/NFPA 70 and any local codes or ordinances that might
apply.
Canada Installations
: Make all electrical connections in
accordance with the current edition of the Canadian Electrical
Code CSA C22.1 and any local codes or ordinances that might
apply.
FIRE HAZARD
Failure to follow this warning could result in personal
injury, death, or property damage.
Do not connect aluminum wire between disconnect
switch and furnace. Use only copper wire. See Fig. 33.
!
WARNING
Use a separate, fused branch electrical circuit with a properly sized
fuse or circuit breaker for this furnace. See Table 11 for wire size
and fuse specifications. A readily accessible means of electrical
disconnect must be located within sight of the furnace.
PG92SAS