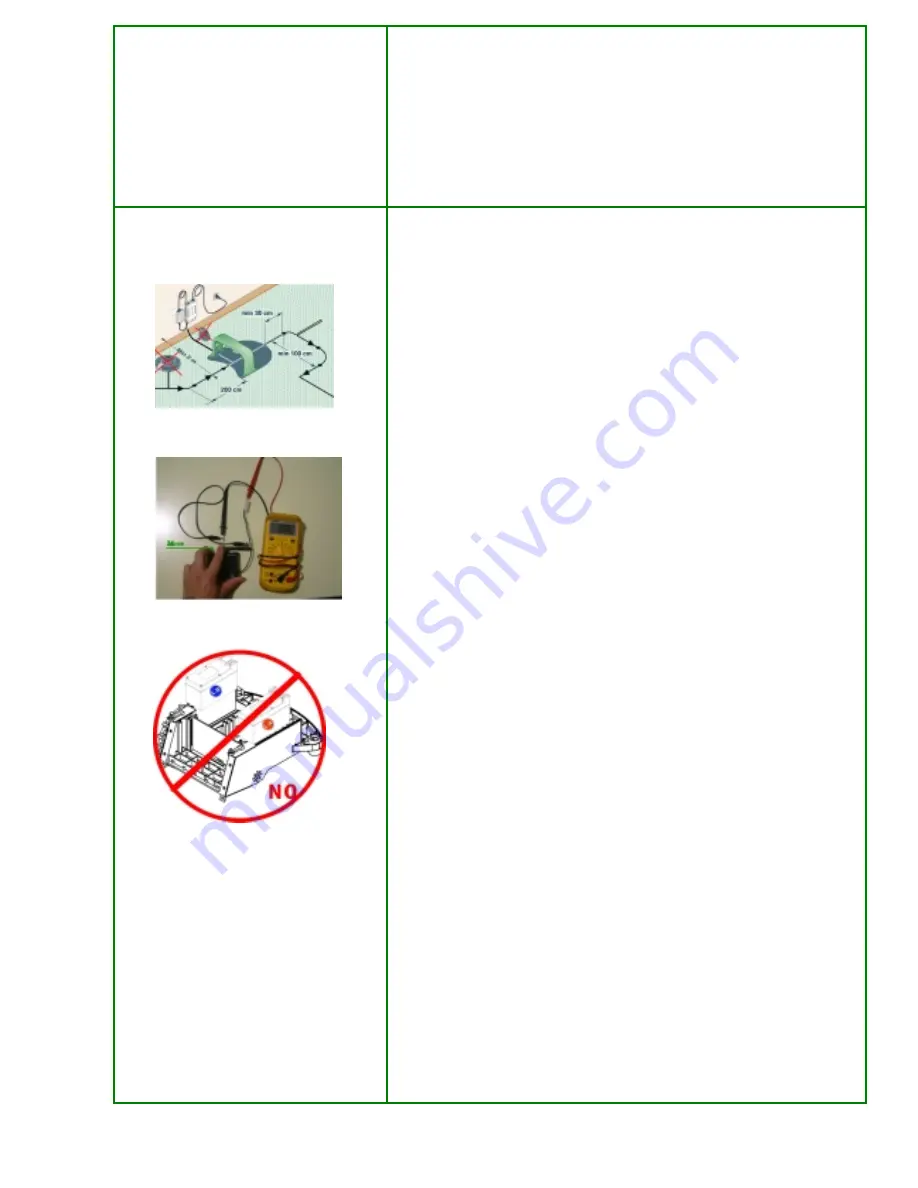
- 22 -
connect the transmitter to the base up to the recharging springs.
-
When the robot is not in the docking station, check the plates tension
with a tester. For the Lithium should be 29,3V.
-
When the robot is switched on CHARGING in its docking station,
check with a tester the tension of the plates and of the charging nuts.
The tension should be the same. If it is different, maybe the plates or
the nuts are dirty. If the tension is the same, check also the batteries
tension. It should be the same. If it is different, maybe the problem is
inside the micro switches/charging wiring group.
“Low battery “ and to short working Time
& Charging lithium problem
Should the robots not work for a sufficient time, please check the following
things:
First of all, before checking the robot, make the following modifications and
repeat the working cycle.
•
Disable the self-programming in the user's menu
•
Clean the blade from grass remains
•
Clean and check the plates and recharging plates.
•
Have the robot recharged all the night long and check the first
working cycle.
•
Check the cutting motor speed that must reach at least 16 RPM when
the batteries are totally charged, there are no cutting efforts and the
robot is not, for sure, under modulation mode.
These tests make the robot reach a normal working condition. If the problem
is not solved, please do as follows:
-
If the robot has 2, 3 or 4 lithium batteries make the following test.
Try to turn on the robot by connecting one only battery at a time.
This permits to check if both the batteries are well working. If one of
them is not working, check the internal fuse; otherwise get in touch
with our service office in ZCS.
-
Control visually or with a tester the contact from the recharging nuts
up to the wiring inside the robot in order to load the batteries.
If the problem is not solved it is necessary to remove the body and
transparent protection out from the robot. Take out the covering from the
recharging base as well. Turn on the robot when it is in the recharging base
and put it under pause mode. After 3 hours make the following tests by using
a digital tester device:
•
Measure the current tension at the outgoing point of the battery
charger (white connector - outgoing point 1,2). It must be 29,3-29,5
•
Measure the current tensions of the recharging plates. It must be
29,3-29,5 otherwise the problem is with cabling under the recharging
base or with the grey cable from the battery charger to the
transmitter.
•
Measure the current tension of the batteries. It must be 29,0-29,5.
Otherwise the problem is with the internal cable of the micro switch
•
If the previous tests are correct, check what the display of Ambrogio
shows. It must show at least Battery 2900. Otherwise the problem is
with the voltmeter of the mother board.
If all these tests do not identify the problem, unfortunately it is necessary to
make a step check with the following items that affect the recharge and
working time.
•
Battery Charger
•
Recharging Base (Under base c Plates)
•
Charging Cabling (Bump group)
•
Robot cabling
•
Mother Board
•
Battery
•
Cutting Motor
•
Blade