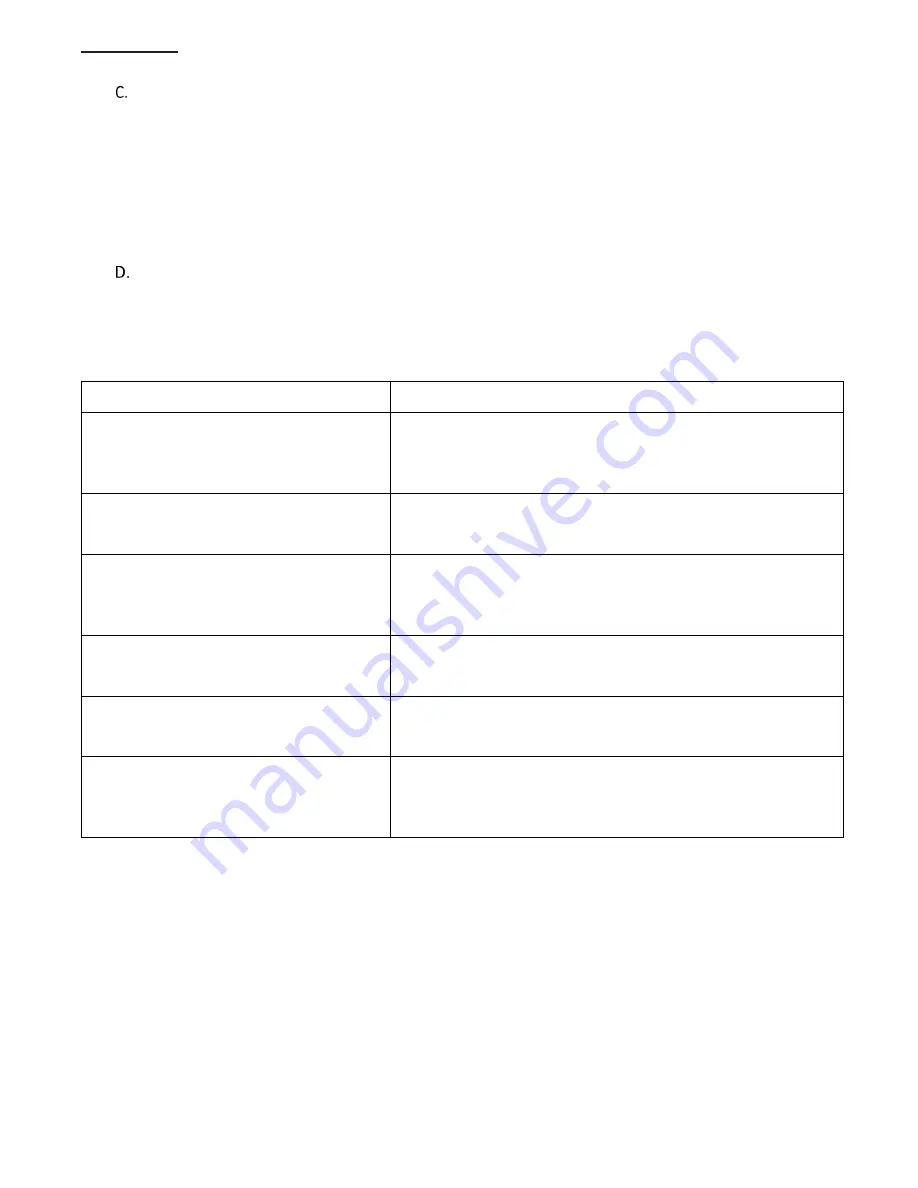
PH
-SERIES
44
INITIAL GAS CHECKS
a)
Make
sure manual valve is turned on.
b)
Make sure
gas valve knob is turned on.
c)
Check for gas supply and proper pressure to valve.
d)
Check wires and make sure that they and their connections are in g
ood
condition.
e)
Check
for
power to valve.
f)
If no power, check control board. (see page 45)
ELECTRICITY AND GAS TO HEATER, BUT STILL INOPERATIVE
If after confirming that adequate gas and electricity are present and unit still does not operate, review
the symptoms below. After the symptom has been identified, refer to the corresponding cause/cure,
Review CHECK CONTROL BOARD section, and finalize troubleshooting procedure.
Symptom
Cause/Cure
1. Dead
A)
Mis-wired
B)
Transformer bad
C)
Fuse/circuit breaker bad
D)
Bad control (check LED for steady on)
2. Thermostat on - No Blower Output
A)
Mis-wired (check PSW terminal voltage)
B)
Bad thermostat - Do voltage @terminal W
C)
Bad control (check LED for steady on)
3. Pressure Switch input okay but no
Trial for Ignition after purge delay
A)
Mis-wired (check PSW terminal voltage)
B)
Flame sense problem (existing flame-check LED-2
Flashes)
C)
Bad control (check voltage between L1 & IND)
4. Valve on, no spark
A)
Shorted electrode
B)
Open HV cable
C)
Bad Control
5. Spark on, no valve
A)
Valve coil open
B)
Open valve wire
C)
Bad control (check voltage between V1 &V2)
6. Flame okay during TFI, no flame
sense (after TFI)
A)
Bad electrode
B)
Bad S1 or HV wire
C)
Poor ground at burner
D)
Poor flame (check flame current)
NOTE: TFI = Trial For Ignition