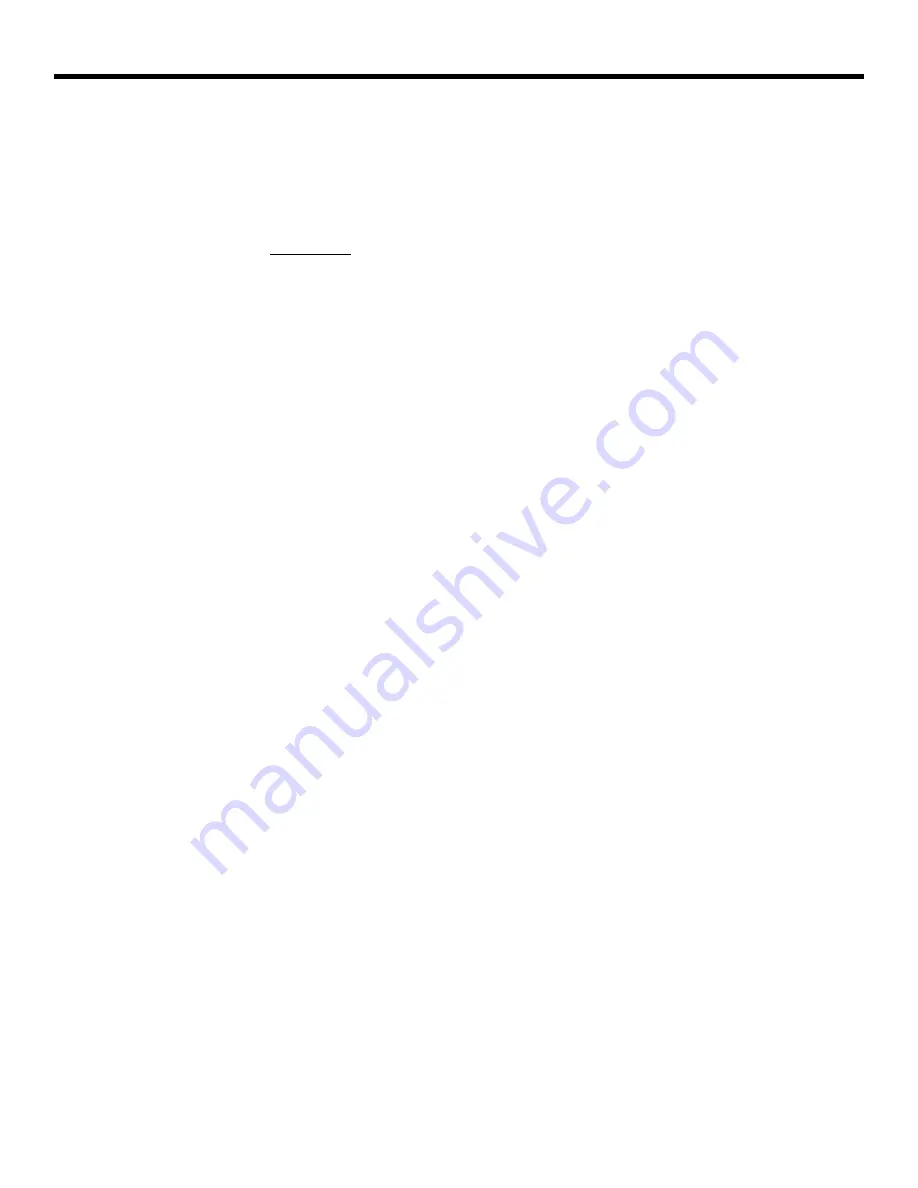
Initial setup and operation of your new pressure washer
When you receive your pressure washer, be sure you check for concealed freight damage. Any
damage should be noted with the delivering carrier. If you have any questions related to freight,
call the 800 number listed in the front of the manual.
Check all oil levels in the pump or engine, if applicable. Failure to check all levels will result in
equipment damage. Most pumps are shipped with oil from factory and the crankcase are sealed,
you may have to remove a shipping plug and install a dipstick in the pump.
Most engines are
shipped
without oil
,
be sure to check these oil levels.
Your water supply must provide water to the equipment that exceeds the Gallon Per Minute
(GPM) rate of your machine. You can check your GPM by using a five gallon bucket and a
timer. If your machine is five GPM or less and the bucket fills in less than a minute you have
adequate supply. Some systems are effected by things like washing machines, livestock water-
ing systems, and flushing toilets. Be sure the supply is still adequate when these operations are
taking place. The water temperature cannot exceed 145 degrees Fahrenheit. Water pressure
should not exceed 60 PSI.
Failure to secure adequate water supply will result in pump
damage. Do not run pump dry.
Your water should not contain particles larger than 80 microns. Although there are small filters
installed on pressure washers that filter the water, they can only filter poor quality water for a
short period of time before they clog. Clogging would result in damage to the machine.
Therefore you should insure no sand or scale particles are present in the water supply.
Hook a garden hose from the hydrant to the machine, when doing this be sure to check the
inlet water filter or screen. This hose should be at least 5/8’ diameter and a length at least 15
feet. This 15 foot length helps isolate the water supply from pulsations from the pump.
Many
states require a Vacuum Break or backflow preventer be installed at the hydrant
,
before the garden hose, to insure the water source cannot be contaminated. Be sure to check
local and state regulations upon installation.
Turn on the water supply and open the trigger gun, this will purge all the air from the system.
Look for water leaks and stop any leak found. Leaks can cause erratic pump behavior.
Turn equipment off and allow time to cool before refueling. Fill the burner tank labeled ‘fuel’.
Be sure the fuel is clean and free from moisture and particles.
Use only No. 1, No. 2 or
kerosene, no other fuel should be used!
There is a fuel filter in the line. Check this filter
prior to operation. Do not run fuel pump dry, doing so will damage the fuel pump.
Prior to starting the motor, check the oil in the pump. Be sure it is at the proper operating level
and that the correct oil is being used. Check the pump breakdown for the proper type of oil.
Inspection
for freight
damage
Inspection
of oil levels
Water supply
Water quality
Supply hose
Purge air
Burner fuel
Pump
4