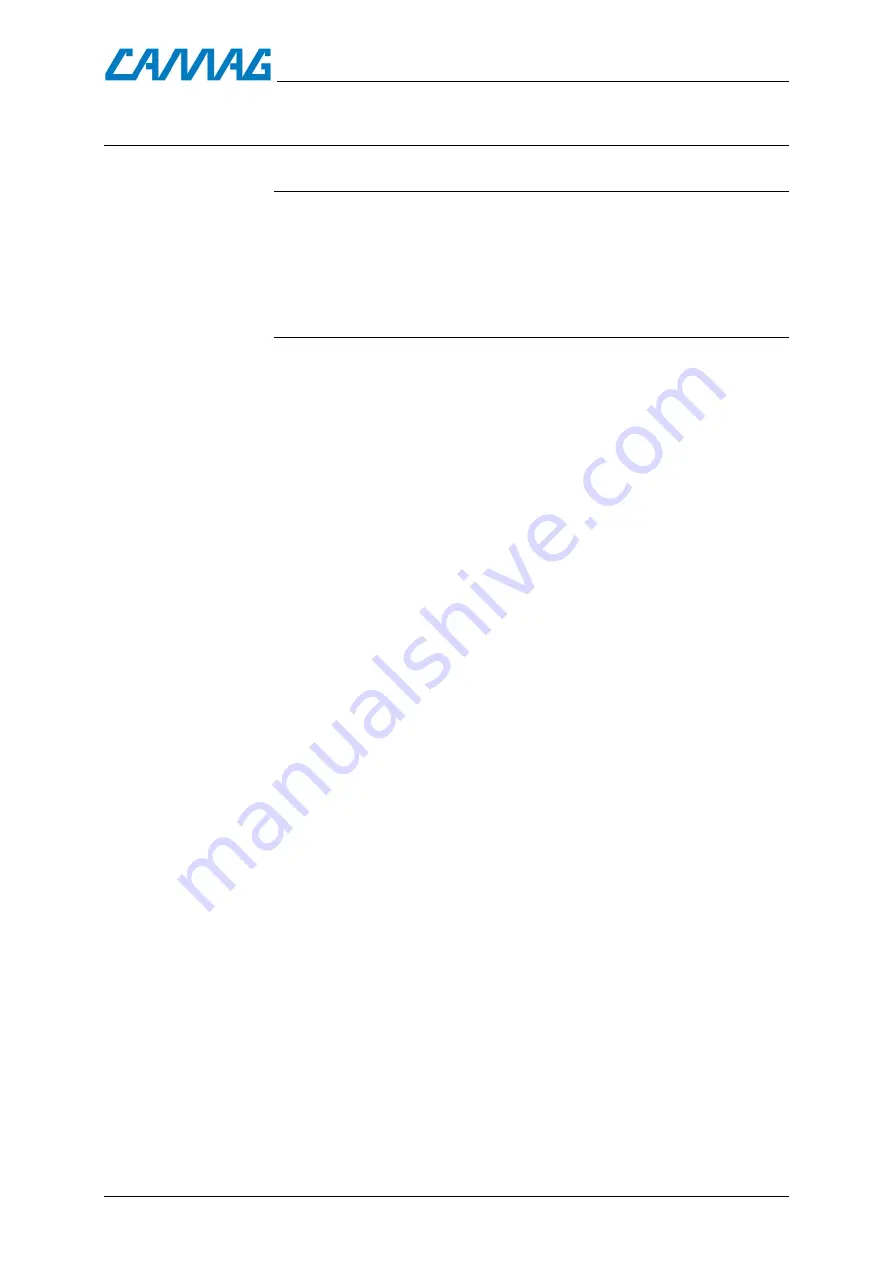
ADC 2
Instruction Manual, November 2016
Page 11
3.
Getting started
3.1.
Automatic instrument monitoring
A sensor system controls and monitors the proper handling and
guarantees a monitored developing process. In case of failure a
signal will sound and an error message displayed. For error mes-
sages see chapter 6.8.
3.2.
Checking system functions
Switch on the instrument. The ADC2 will now show the installed
firmware version and perform the following checks and tasks:
1. Initializing the drying module.
2. Initializing the lift drive.
If startup was successful the display will show:
* * ADC2 * *
SYSTEM READY
In this phase, only physical blocking of a drive can cause an error.
If necessary, check whether there are obstacles in the instrument.
Summary of Contents for ADC 2
Page 1: ...INSTRUCTION MANUAL ADC 2 ...
Page 41: ......