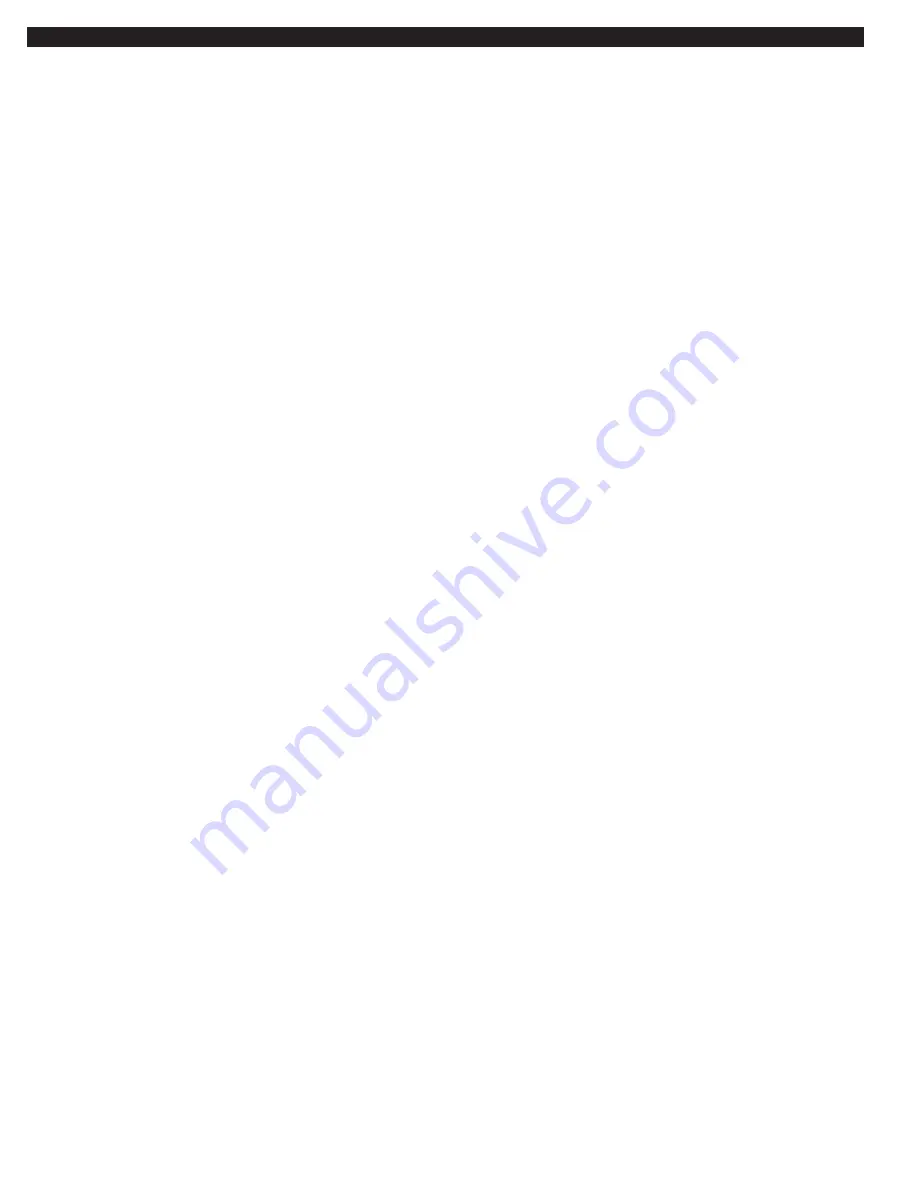
6
Daily Operation
• Make sure power supply is on and working.
• If light does not come on, check that the reset button is pushed in. This is found
behind the face cover of the unit. You will need a Phillips screwdriver.
• If indicator light works properly but temperature does not get hot at the tap, test
for a plumbing crossover; shut off cold supply to heater and open hot water tap.
No water should be flowing. Any continued flow indicates a crossover which will
affect the temperature and will need to be corrected.
• Heating element may need to be replaced. (Please refer to your hot water heater
handbook for replacement instructions.)
Pump Will Not Start
• Is the motor hot? Thermal breaker may have triggered;
it will reset when cool.
• Check wall outlet for voltage (fuse or breaker).
• Check pressure switch operation and correct voltage at
switch or motor wires.
• Check rectifier or motor for open or grounded circuit.
• Check for locked drive assembly.
Pump Will Not Prime
• Out of product?
• Check strainer for debris.
• Check Inlet tubing / plumbing for severe vacuum leak.
• Inlet / outlet tube severely restricted (kinked)
• Check for debris in pump inlet / outlet valves.
• Proper voltage with the pump operating (+/- 10%)
• Check pump housing for cracks.
Pump Will Not Shut off
(Pressure switch equip.)
• Output line closed and no leaks
• Check for air trapped in outlet line or pump head.
• Check for correct voltage to pump (+/- 10%)
• Check Inlet / outlet valves for debris or swelling.
• Loose drive assembly or head screws.
• Pressure switch operation / adjustment incorrect. Refer
to pump (Shurflo) service bulletin #1031 for differential
and pressure adjustment procedure. (110v Model)
Noisy / Rough Operation
• Mounting feet are compressed too tightly.
• Loose pump head or drive screws.
• Does the mounting surface multiply noise? (flexible)
• Is pump plumbed with rigid pipe causing noise to transmit?
Note: This pump is to be used for the circulation of water only.
No solvents—especially flammable liquids—are to be
used in this system.
Leaks from Pump Head or Switch
• Check for loose screws at switch or pump head.
• Is switch diaphragm ruptured or pinched?
• Check for punctured diaphragm if fluid is present at
bottom drain holes.
Light Not on
• If light does not come on, but water gets hot, check for faulty bulb.
• Check reset button mentioned in earlier section.
Brown Water
Brown or rusty water indicates a “spent” anode rod. Replace anode rod.
Odor in Water
Smelly water could be due to an unusual reaction between local water and the
heater’s anode rod. Check anode rod.
(See section on changing anode rod in hot water heater handbook.)
Water is Too Hot
Remove face plate on front of heater and rotate the temperature selector counter-
clockwise to lower temp. If temperature never lowers, then replace the thermostat.
(See hot water heater handbook for details on this operation.)
Leaking
Periodically check all water fittings to and from heater unit. Also remove the face
cover and check the gasket to the heating element inside.
Hot Water Heater Unit
Water Pump
IV. Troubleshooting Guide
Note: Always keep this operator’s manual and the hot water heater handbook
together for operation reference and troubleshooting points.