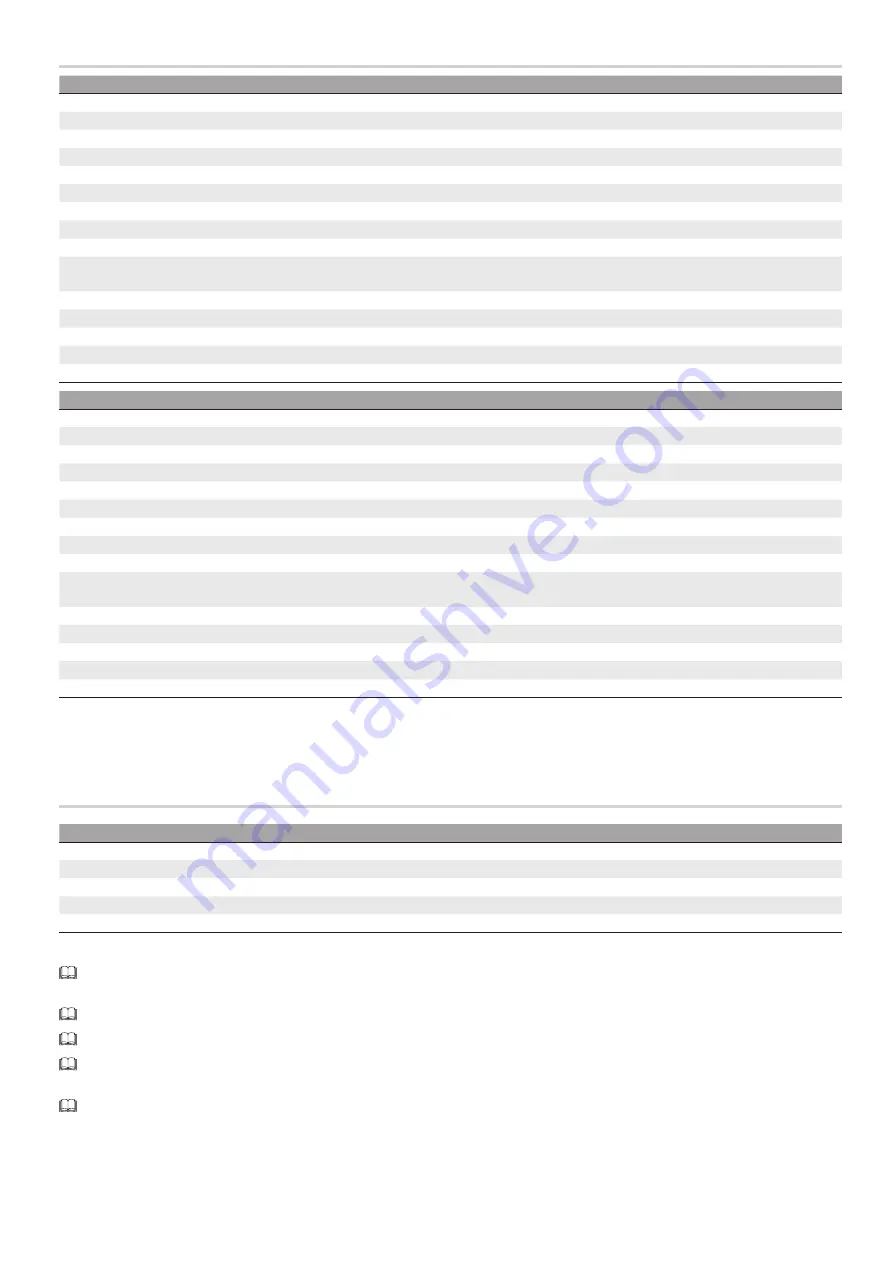
Page
9
- Manual
FA02036-EN
- 12/2023 - © C
AME S.p.A. - The contents of this manual may be changed at any time and without notice. - T
ranslation of the o
riginal instructions
Technical data
MODELS
BXV04AGS
BXV06AGS
BXV08AGS
BXV10AGS
BXV04RGS
BXV06RGS
BXV08RGS
BXV10RGS
Power supply (V - 50/60 Hz)
230 AC
230 AC
230 AC
230 AC
110 AC
110 AC
110 AC
110 AC
Motor power supply (V)
24 DC
24 DC
24 DC
24 DC
24 DC
24 DC
24 DC
24 DC
Standby consumption (W)
5,5
5.5
5.5
5.5
5.5
5.5
5.5
5.5
Power (W)
170
270
400
400
170
270
400
400
Maximum current draw (A)
7
11
16
16
7
11
16
16
Colour
RAL 7024
RAL 7024
RAL 7024
RAL 7024
RAL 7024
RAL 7024
RAL 7024
RAL 7024
Thrust (N)
350
600
800
1000
350
600
800
1000
Maximum operating speed (m/min)
12
12
11
11
12
12
11
11
Operating time (s)
180
180
180
180
180
180
180
180
Duty cycle
HEAVY-DUTY
SERVICE
HEAVY-DUTY
SERVICE
HEAVY-DUTY
SERVICE
HEAVY-DUTY
SERVICE
HEAVY-DUTY
SERVICE
HEAVY-DUTY
SERVICE
HEAVY-DUTY
SERVICE
HEAVY-DUTY
SERVICE
Pinion module
4
4
4
4
4
4
4
4
Limit-switch type
MECHANICAL
MECHANICAL
MECHANICAL
MECHANICAL
MECHANICAL
MECHANICAL
MECHANICAL
MECHANICAL
Protection rating (IP)
54
54
54
54
44
44
44
44
Insulation class
I
I
I
I
I
I
I
I
Average life (cycles)**
150000
150000
150000
150000
150000
150000
150000
150000
MODELS
BXV06AGL
BXV10AGL
BXV04ALS
BXV06ALS
BXV08ALS
BXV10ALS
Power supply (V - 50/60 Hz)
230 AC
230 AC
230 AC
230 AC
230 AC
230 AC
Motor power supply (V)
24 DC
24 DC
24 DC
24 DC
24 DC
24 DC
Standby consumption (W)
5.5
5.5
5,5
5.5
5.5
5.5
Power (W)
270
400
170
270
400
400
Maximum current draw (A)
11
16
7
11
16
16
Colour
RAL 7024
RAL 7024
RAL 7040
RAL 7040
RAL 7040
RAL 7040
Thrust (N)
600
1000
350
600
800
1000
Maximum operating speed (m/min)
12
11
12
12
11
11
Operating time (s)
180
180
180
180
180
180
Duty cycle
HEAVY-DUTY
SERVICE
HEAVY-DUTY
SERVICE
HEAVY-DUTY
SERVICE
HEAVY-DUTY
SERVICE
HEAVY-DUTY
SERVICE
HEAVY-DUTY
SERVICE
Pinion module
4
4
4
4
4
4
Limit-switch type
MAGNETIC
MAGNETIC
MECHANICAL
MECHANICAL
MECHANICAL
MECHANICAL
Protection rating (IP)
54
54
54
54
54
54
Insulation class
I
I
I
I
I
I
Average life (cycles)**
150000
150000
150000
150000
150000
150000
(*) Before installing the product, keep it at room temperature where it has previously been stored or transported at a very high or very low temperature.
(**) The average product life specified should be understood purely as an indicative estimate. It applies to normal usage conditions and where the product has been
installed and maintained in compliance with the instructions provided in the CAME technical manual. The average product life is also affected, including significantly,
by other variables such as, but not limited to, climatic and environmental conditions. The average product life should not be confused with the product warranty.
Cable types and minimum thicknesses
Cable length (m)
up to 20
from 20 to 30
Power supply 230 V AC
3G x 1.5 mm2
3G x 2.5 mm2
24 V AC/DC flashing beacon
2 x 1 mm2
2 x 1 mm2
TX Photocells
2 x 0.5 mm2
2 x 0.5 mm2
RX photocells
4 x 0.5 mm2
4 x 0.5 mm2
Command and control devices
* no. x 0.5 mm2
* no. x 0.5 mm2
* no. = see product assembly instructions - Warning: the cable cross-section is indicative and varies according to the motor power and cable length.
When operating at 230 V and outdoors, use H05RN-F cables compliant with 60245 IEC 57 (IEC); when indoors, use H05VV-F cables compliant with 60227 IEC 53
(IEC). For power supplies up to 48 V, use FROR 20-22 II cables compliant with standard EN 50267-2-1 (CEI).
To connect the antenna, use RG58 cable (up to 5 m).
For paired connection and CRP, use UTP CAT5 cable (up to 1,000 m).
If the cable lengths differ from those specified in the table, define the cable cross-sections according to the actual power draw of the connected devices and in
line with regulation CEI EN 60204-1.
For multiple, sequential loads along the same line, recalculate the values in the table according to the actual power draw and distances. For information on
connecting products not covered in this manual, please see the documentation accompanying the products themselves.