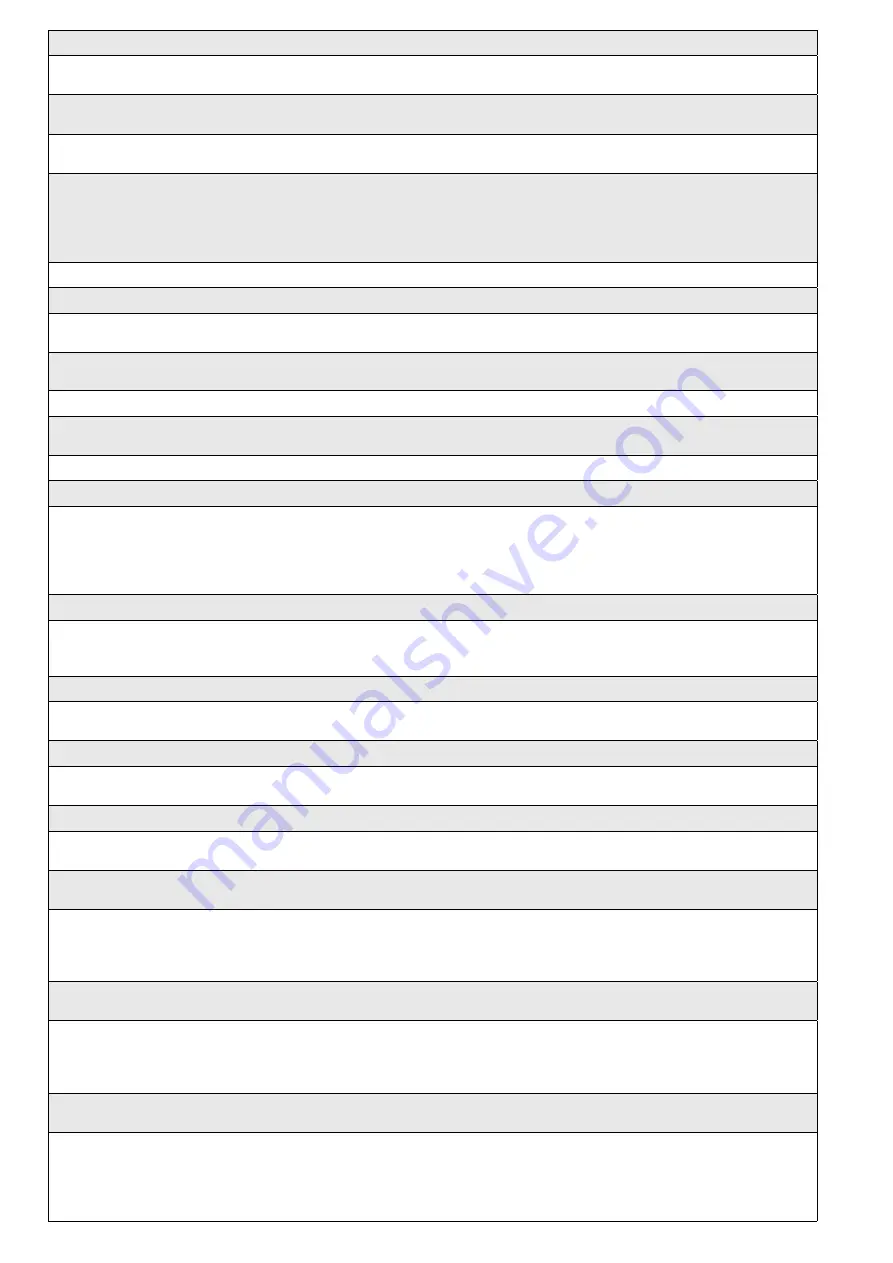
p.
2
0
20
- M
an
u
al
c
od
e:
F
A
0
0
1
2
4
-E
N
FA
0
0
1
2
4
-E
N
v.
3
- 04/
2
0
17 - © C
am
e S
.p.
A
. - T
h
e m
an
u
al
's c
onte
nts m
ay b
e e
d
ite
d at a
ny ti
m
e w
ith
ou
t n
oti
ce
.
F6 Hold-to-run
0 = Deactivated (
default
) / 1 = Activated
Press and hold a button to open and close the barrier. Opening button on contact 2-3; closing button on contact 2-4. All other command
devices, including radio-controlled devices, are excluded.
F9 Obstruction
detection
with motor idle
0 = Deactivated (
default
) / 1 = Activated
With the barrier open or closed or after a total stop, if the safety devices (photocells or safety edges) detect an obstacle the operator remains
stationary.
F10 Open-barrier signal
output
0 = on with boom raised and moving (
default
) /
1 = fl ashes intermittently every half second during opening
fl ashes intermittently every second during closing
on with boom raised
off with boom lowered
It signals the barrier status. The signalling device is connected to contact 10-5.
F11 Encoder
0 = Activated (
default
) / 1 = Deactivated*
It manages slow-downs, obstruction detection and sensitivity.
* Connect the micro-switches to F-FC-FA.
F14 Sensor type selection
0 = control with transponder sensor or magnetic card reader /
1 = control with keypad selector (
default
).
Setting the type of sensor to control the barrier.
F15 Luminous cord signal
output
0 = Boom moving (
default
) / 1 = Boom moving and closed
It signals the status of the barrier with intermittent lights. Luminous cord connected to contact 10-E6.
F18 Additional light
0 = Flashing light (
default
) / 1 = Beacon / 2 = Courtesy light
Output on 10-E1.
The fl ashing light functions during opening and closing.
The beacon stays on from the moment the barrier begins to open until it is fully closed (including automatic closing time). Where the automatic
closing function is not activated, it only stays on during barrier movement.
The courtesy light either stays on for a fi xed period of 180 seconds or can be adjusted; see function F 25.
F19 Automatic closing time
0 = Deactivated (
default
) / 1 = 1 second / ... / 180 = 180 seconds
The waiting time before the barrier closes automatically starts when the limit-switch point is reached during opening. The time can be set to
between 1 second and 180 seconds. The barrier is not closed automatically where the safety devices are triggered by an obstacle, after a total
stop or where there is no power.
F21 Pre-fl ashing time
0 = Deactivated (
default
) / 1 = 1 second / … / 5 = 5 seconds
Adjusting the pre-fl ashing time of the fl ashing light connected to 10-E1 before each manoeuvre. The fl ashing time can be set to between 1
second and 10 seconds.
F22 Working time
5 = 5 seconds / … / 120 = 120 seconds (
default)
Gearmotor cycle time during opening or closing.
The working time can be set to between 5 seconds and 120 seconds.
F25 Courtesy light time
60 = 60 seconds / … / 180 = 180 seconds (
default
)
Additional light; it stays on when the barrier opens and closes.
The time can be set to between 5 seconds and 120 seconds.
F28 Opening manoeuvre
speed
70 = Minimum speed / … / 100 = Maximum speed.
Setting the boom opening speed, calculated as a percentage.
⚠
Warning: the speed parameter fi elds vary according to the type of boom:
- for booms with a joint, between 2 m and 4 m, set the speed percentage from 70 to 100;
- for booms between 6 m and 8 m, set the speed percentage from 80 to 100.
F29 Closing manoeuvre
speed
70 = Minimum speed / … / 100 = Maximum speed.
Setting the boom closing speed, calculated as a percentage.
⚠
Warning: the speed parameter fi elds vary according to the type of boom:
- for booms with a joint, between 2 m and 4 m, set the speed percentage from 70 to 100;
- for booms between 6 m and 8 m, set the speed percentage from 80 to 100.
F30 Opening slow-down
speed
15 = Minimum speed / … / 40 = Maximum speed
Setting the boom opening slow-down speed, calculated as a percentage.
⚠
Warning: the speed parameter fi elds vary according to the type of boom:
- for 2 m booms with a joint, set the slow-down speed percentage from 20 to 40;
- for 4 m booms, set the slow-down speed percentage from 20 to 30.
- for booms between 6 m and 8 m, set the slow-down speed percentage from 15 to 40.