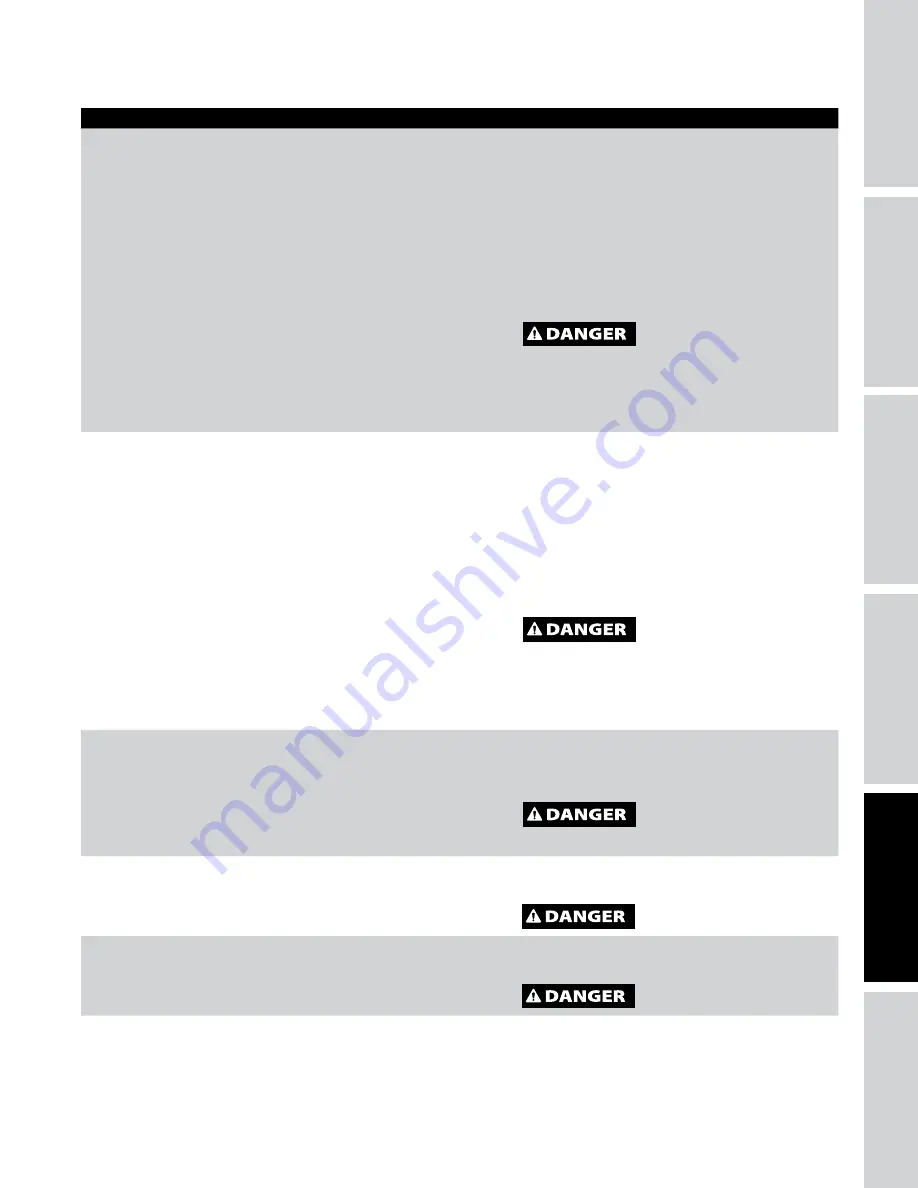
TROUBLESHOOTING GUIDE
MAINTENANCE /
REP
AIR
TROUBLESHOOTING
OPERA
TION
ASSEMBL
Y /
INST
ALLA
TION
SAFETY /
SPECIFICA
TIONS
GETTING ST
AR
TED
15
SYMPTOM
POSSIBLE CAUSE(S)
CORRECTIVE ACTION
Motor hums and runs slowly or
not at all.
1. Low voltage.
1. Check incoming voltage. It should be approximately
230 volts. Motor will not run properly on 208 volts.
Low voltage could be due to wires (from electrical
source to compressor) being too small in diameter
and / or too long. Have a qualified electrician check
these conditions and make repairs as needed.
2. Too many devices on same circuit.
2. Limit the circuit to the use of compressor only.
3. Loose electrical connections.
3. Check all electrical connections.
4. Malfunctioning pressure switch -
contacts will not close.
4. Replace pressure switch.
5. Malfunctioning check valve.
5. Replace check valve.
Do not disassemble check valve
with air pressure in tank.
6. Defective unloader valve on pressure
switch.
6. Replace unloader valve.
7. Defective motor capacitor(s).
7. Replace capacitor(s).
8. Defective motor.
8. Replace motor.
Reset mechanism cuts out
repeatedly or circuit breaker
trips repeatedly.
1. Lack of proper
ventilation / room temperature too
high.
1. Move compressor to well-ventilated area.
2. Too many devices on same circuit.
2. Limit the circuit to the use of only the air
compressor.
3. Restricted air intake.
3. Clean or replace filter element.
4. Loose electrical connection.
4. Check all electrical connections.
5. Pressure switch shut-off pressure set
too high.
5. Replace pressure switch.
6. Malfunctioning check valve.
6. Replace check valve.
Do not disassemble check valve
with air pressure in tank.
7. Defective unloader valve on pressure
switch.
7. Replace unloader valve.
8. Defective motor capacitor(s).
8. Replace capacitor(s).
9. Malfunctioning motor.
9. Replace motor.
Tank does not hold pressure
when compressor is off and
the shut off valve is closed.
1. Air leaks (fittings, tubing on
compressor, or plumbing outside
system).
1. Check all connections with soap and water solution.
Tighten; or remove and apply sealant to threads,
then reassemble.
2. Worn check valve.
2. Replace check valve.
Do not disassemble check valve
with air pressure in tank.
3. Check tank for cracks or pin holes.
3. Replace tank. Never repair a damaged tank.
Pressure switch continuously
blows air out the unloader
valve
Malfunctioning check valve
Replace the check valve if the unloader valve on the
pressure switch bleeds off constantly when unit shuts
off.
Do not disassemble check valve
with air pressure in tank.
Pressure switch does not
release air when the unit shuts
off
Malfunctioning unloader valve on
pressure switch
Replace the pressure switch if it does not release the
pressure for a short period of time when the unit shuts
off.
Do not disassemble pressure
switch with air pressure in tank
Excessive vibration
1. Loose fasteners on pump or motor
1. Tighten fasteners.
2. Belt needs replaced
2. Replace with correct size.
3. Belt alignment
3. Align flywheel and pulley.