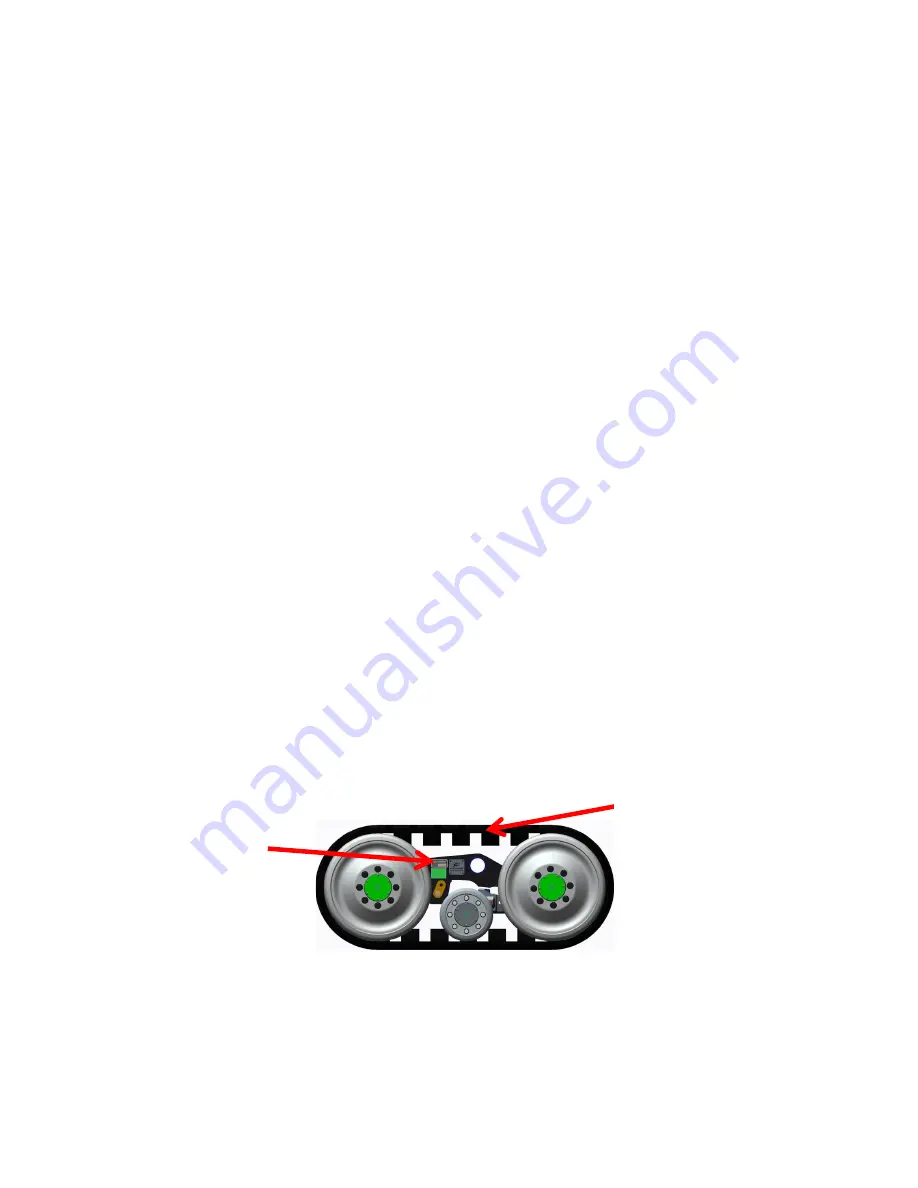
CPB-516 Operation and Maintenance Manual – TTS 30-40-45 Series (excluding 45-1814) (01-2020)
4
1.0 FOREWARD
This manual provides important operation and maintenance instructions to maximize the
benefits of the Camso Trailed Track System (TTS) and to ensure performance in the field
for many years to come.
1.1 Literature Information
This manual was prepared with the latest information available at the time of publication.
Read this manual carefully before operating or servicing the undercarriage(s).
The photos, illustrations, and data used in this manual were current at the time of printing,
but due to possible production changes, your undercarriage may vary slightly. Camso
reserves the right make changes to new production undercarriages as necessary without
notification. This document must be considered as an integral part of the rubber track
system, it must always be available for reference near the machine, even in the case of
sale, and until end of life. Should the operations and maintenance manual supplied with
the track system be damaged or missing, please see your dealer to request another copy
and/or contact Camso immediately.
1.2 Maintenance Intervals
Use the pulling machine hour meter to determine servicing intervals. Calendar intervals
are also shown and can be used instead of hour intervals. Recommended service should
always occur on the interval that occurs first. Under extremely dusty or wet operating
conditions more frequent lubrication may be needed. Perform service on items at
multiples of the original requirement. For example, at every annual or 250 hour service
interval, also service items listed under monthly or 100 hours, weekly or 50 hours, and
daily or 10 hours.
1.3 Camso Product Identification Number
The track system PIN plates will display the model and manufacturing date and sequence
number on both LH and RH undercarriage system. Each undercarriage has a unique
serial #.
If a serialized axle is also provided by Camso, it will also have a plate installed in the
center of the axle. Track part # and serial # are embossed into the edge of the track
carcass for ease of identification.
Undercarriage
Serial #
Model #
Track
Part #
Serial #
(on edge of track carcass)
Summary of Contents for TTS 30 Series
Page 28: ...Camso co Camso 2019 ...